Researchers around the world, including those in Canada, have been racing to create technology that can reduce the workers required on fruit and vegetable farms and in processing plants. But the pace has been slow and the big labour savings so far have been limited.
Why it matters: Finding ways to get the job done on Canadian farms will be one of the defining issues in this country’s future as a food exporter.
In many cases, human workers still make sense from a management and financial perspective. Being on the bleeding edge of technology adoption is financially risky.
Read Also
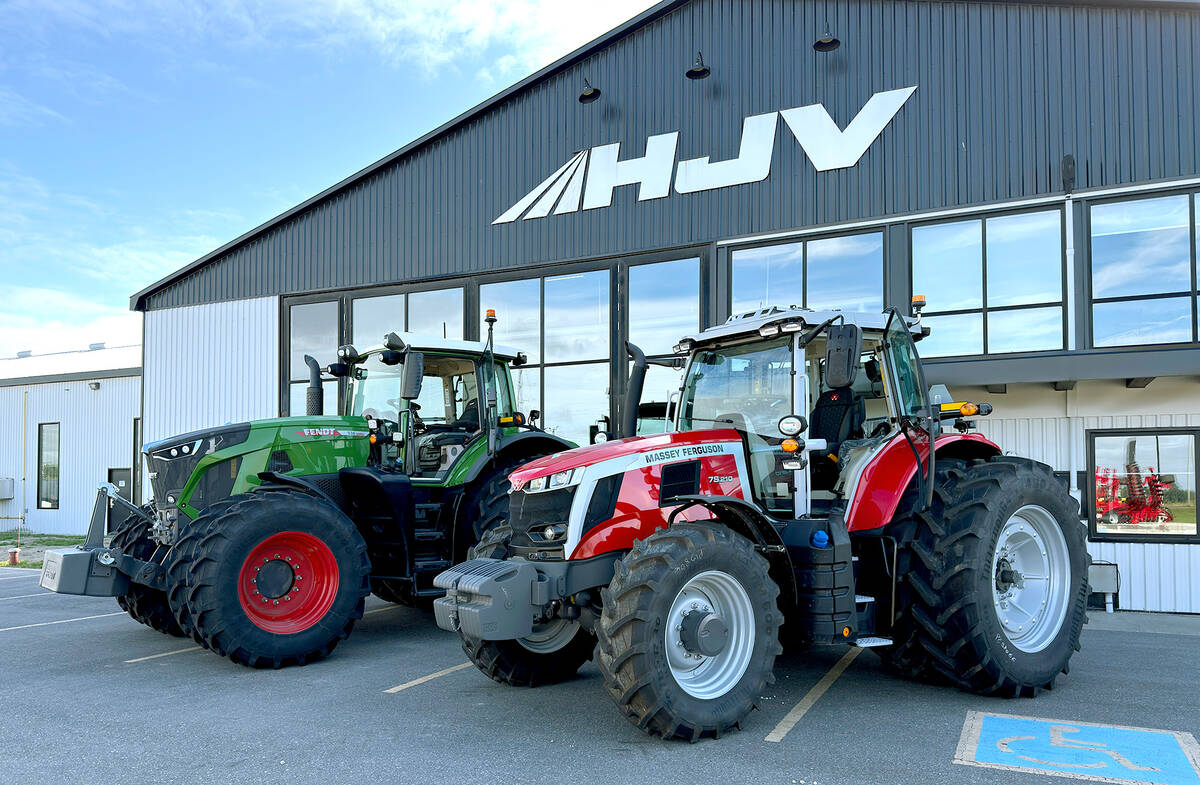
HJV Equipment expands as full-line PTx Trimble dealer
HJV Equipment expands as a full-line PTx Trimble dealer, increasing its capacity to assist growers with advanced agricultural technology solutions.
According to farm technology policy and development experts, automation requires locally available expertise and connectivity to businesses that adopt the technologies.
The rollout of automation technologies heavily relies on localized support systems, says Tyler Whale, president of Ontario Agri-Food Technologies.
New systems require service, repair, and a proven track record of contributing to return on investment. However, that support may not exist if the technology was developed outside the province or country.
For example, Whale says incorporating a German-designed biodigester into a farm brings many benefits. But if repairs are needed, service technicians must be flown in from Germany at the farmer’s expense. The same problem applies to automation equipment, much of which originates in Europe.
“Farmers are business people. Tech gets adopted into agriculture very slowly because you have to displace something that’s already working and they trust,” says Whale, identifying the reliance on foreign labour as one such system.
Karen Hand, director of data research strategy for the University of Guelph’s Food from Thought research program — as well as president and founder of ag-data consulting group Precision Strategic Solutions — expresses similar sentiments. However, she says automation technologies are often not well matched to differing objectives and conditions among businesses.
Where automation technologies are being adopted, she says, that rate is understandably slow as business owners incorporate one thing, then verify its practicality before moving to the next. The technology may not be fully mature either, meaning the cost of further research and development is frequently transferred to the farmer.
“I’m not convinced farmers or industry understand how to, or how often, technologies need to be calibrated, if the calibration itself is valid or if it can even be accomplished,” says Hand. “In general, we don’t have a clear understanding on the best use of tech on a farm.”
Whale and Hand both say the “uni-dimensional” nature of automation technologies (for example comparatively slow and expensive weed robots) only exacerbates the lack of automation in some parts of the sector.
“A robot meant to pick rocks should be able to do other things. Cutting grass, moving supplies, things like that,” says Whale. He adds automation technologies are generally not cheap, and often bring a steep learning curve.
Together, these factors make potential investments feel more like financial speculation.
Hussam Haroun, director of automation for the Vineland Research and Innovation Centre, said the automation possibilities for greenhouse and other indoor farms might be greater than they are for other types of operations. However, the lack of adequate support networks has been an issue. Generally, this has helped direct automation investments toward more easily managed post-harvest processes.
But fundamentally, automation technologies still have difficulty competing with the efficiency and deft touch of human hands.
“From a Vineland point of view we’ve been spending a lot of time on robotics and machine learning,” says Haroun. “We have growers very interested in post-harvesting solutions…. If you look at it on the picking side, that’s a much more difficult challenge.”
Barriers to interconnectivity
Piecemeal adoption is a problem, says Hand.
The Internet of Things – the connection of many objects with transmitting and data record abilities – is not yet a reality. The fact that these data recorders can’t communicate with each other is a barrier to implementing automation on farms and to improving efficiency.
Automation can only be adopted task by task, and business by business.
“They’re not really providing the amount of ROI they could, had we taken a more systems approach,” she says.
“We really need to take more of a systems view of how technologies are working…. We need concerted leadership to look at the entire system and help implement technologies post-COVID.”
Still, Canada is not a technological backwater. Whale stresses the significance and commonality of “behind-the-scenes” automation and semi-autonomous technologies, such as any piece of internet-connected sensing equipment, and stresses the opportunities in applying them to menial and repetitive tasks.
Automation doesn’t always have to be “smart”
Machines that cut and transport crops like celery, for example, can eliminate the need for one or more people from the harvesting process. Whale says there are examples of farms in other jurisdictions, notably California, which cut labour needs in half by adopting these technologies.
“Automation could be a conveyor belt with motors, just things to save steps,” Whale says. “We often get caught up in the idea automation has to be super advanced and smart. There is a lot of automation going on that might not be recognized, and a lot of developers of these systems should think of making semi-autonomous systems.
“A big part of adoption will be growing support systems here at home. We need to look in the value chain for more opportunities, and hopefully land some of those automation jobs here.”
According to Haroun, currently available technology could significantly reduce labour costs in the enclosed horticulture sector. Advances in machine learning and other artificial intelligence streams also mean the reliance on labour for more delicate tasks will eventually lessen.
Rethinking how automation fits within farms, however, is another opportunity.
Rather than building machines to fit current farm infrastructure, says Haroun, the growing process of a given farm could instead change to fit the technology — moving plants between stationary robots rather than mobile robots moving between plants, for example.
“The industry is now seeing how soon we need automation,” he says, in reference to the ongoing pandemic.
Hand reiterates many automation opportunities are not new, and COVID-19 has brought a sobering view of our collective labour dependence.
“We were not ready across our supply chain. Strategic incorporation of automation technologies didn’t happen, and now we’re paying the price for it.”