In the hunt for higher yields, equipment manufacturers are combining more digital tech with in-field iron to alleviate a variety of planting challenges – from compaction to uneven planting depth.
Addressing localized compaction
For Shawn Livingston, Eastern Canada regional manager for Precision Planting Inc., the impact of localized compaction on crop root development has been somewhat overlooked by large equipment manufacturers. However, it’s an issue he says can be alleviated by mild tillage just ahead of seeding.
Read Also
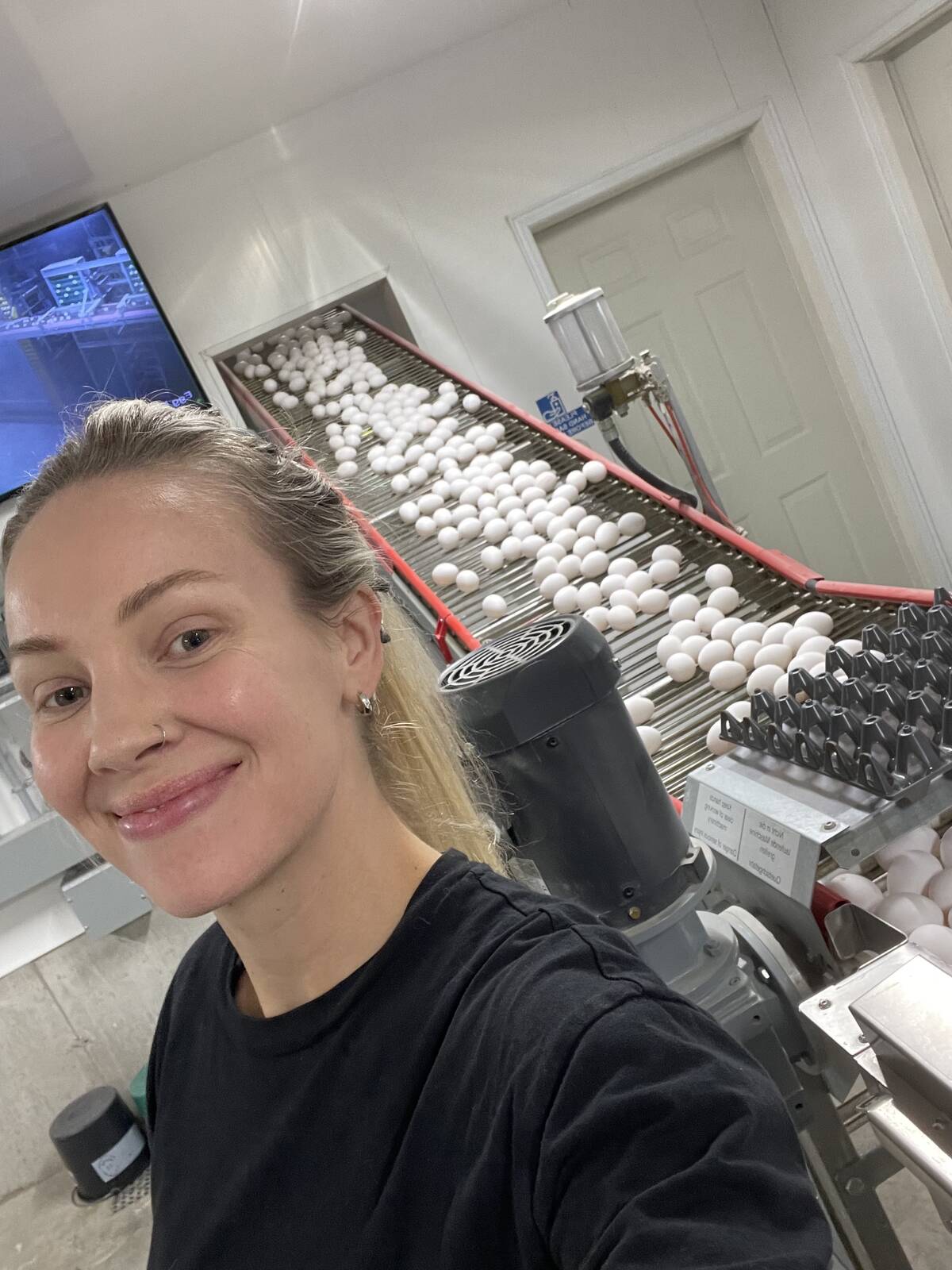
Layer management platform aims to ease record-keeping workload
Timely management of factors influencing egg production can have a significant impact on the ultimate income from a flock.
Based on research at Precision Planting field sites in Ontario and Illinois, his company developed the planter-adaptable Furrow Force as a remedy. The system employs discs on either side of the seed to fracture soil in close proximity to the planting row, while rear wheels apply pressure to firm ground around the seed.
This is done in combination with a load sensor measuring ground contact, as well as weight pressure, which monitors both processes. Rows can also be controlled individually to account for soil variability.
Fendt and its parent company AGCO are similarly trying to address compaction at planting with the Momentum planter and Load Logic weight distribution system.
Introduced to North America in 2020, Fendt says the Momentum planter uses a digital hydraulic system to consistently place seeds at the optimum depth and spacing regardless of variations in soil moisture, soil type, residue levels, terrain or operating speed. It’s also built to help minimize compaction from planter tires, which is accomplished by combining more spread-out tires with an operator-controlled toolbar weight distribution system.
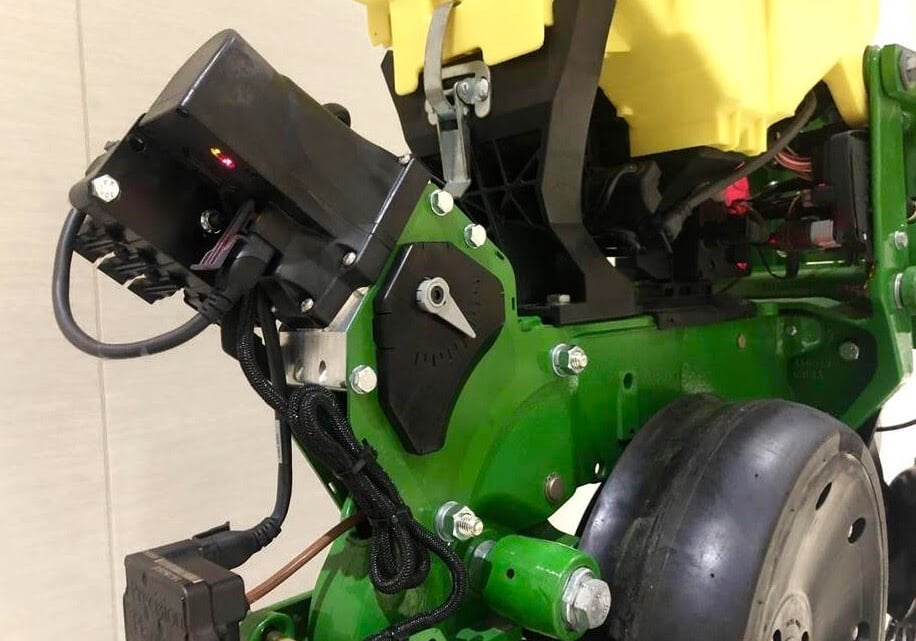
Moisture retention, seed depth corrections
Like AGCO, Livingston says Precision Planting is also trying to find solutions to seeding depth variability – specifically that caused by mechanical wear and tear.
His company’s Smart Depth system is marketed as a remedy to the problem. Designed to fit a variety of planter makes and models, it replaces existing depth setters and calibrates each row individually.
“There are mechanical components on every planter that have metal on metal to stop the depth mechanism…If I have a row set for two inches, my row beside it could very well be planting at 1.5 inches, which creates a lot of emergence issues,” he says.
Moisture variability – specifically drought – and its impact on stand consistency is another area of focus. By developing a system that better seals soil around the seed, Livingston says problems with extended dry conditions shortly after planting are less concerning.
“One of our research plot sites went 27 days without rain after we planted. Moisture retention is huge in that environment. I think that was detrimental this year, not getting enough pressure to seal the ground back up.”
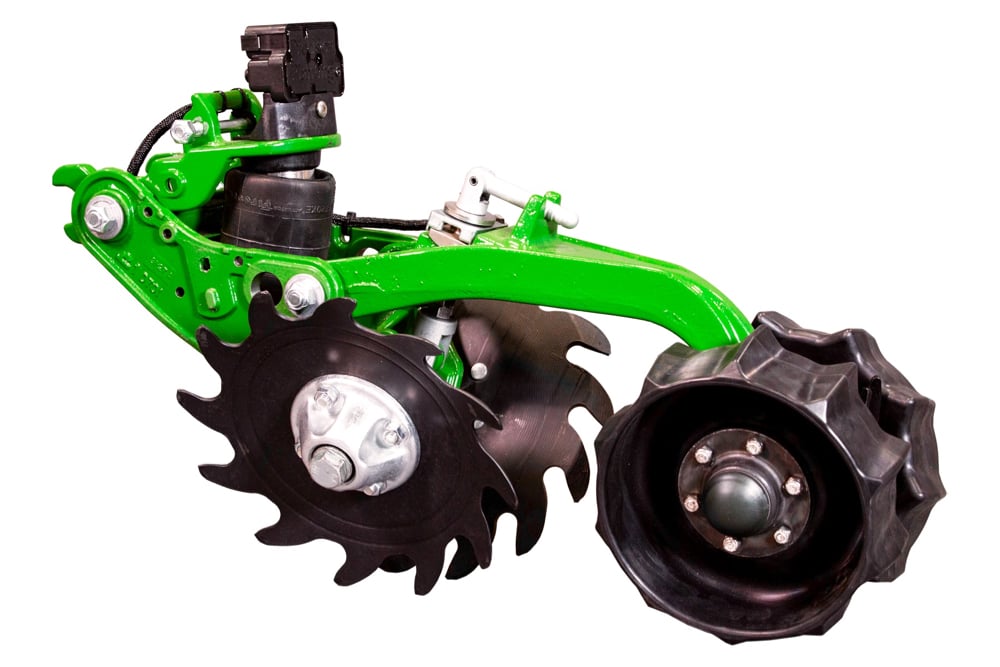
Precision seeds, faster speeds
Refinements in variable-rate continue to be an area of interest for equipment manufacturers as well.
Jeff McGavin, co-owner of McGavin Farm Equipment and chair for Canada East Equipment Dealers’ Association, says most new planters come with electric drives capable of on-the-go changes to seeding populations.
Growers use the capability though GPS – and in conjunction with fertility and yield data – to maximize returns on productive areas, while saving on less productive ones. Further input savings come from row shut-offs designed to prevent seeding overlap.
Proprietary digital systems can still cause headaches, however. The software system used in a red tractor, for example, might have difficulty communicating with a green planter, and vice versa.
“They like to try to keep it as their brand. If they sell a John Deere tractor, they want you to have a John Deere planter,” says McGavin, a New Holland dealer, though he adds manufacturers have come a long way in terms of compatibility.
Other innovations include adjustable row spacing and speed. That is, planters which can change row widths, and operate two to three times faster than older models (10-15 mph instead of 5 mph) without compromising efficacy.