The high-clearance sprayer represents some of the most advanced agricultural technology that we have today — except for that obsolete guessing glass gauge we depend on to sight-estimate liquid volume in the tank.
It’s time to get rid of the clear sight gauge.
Why it matters: A digital gauge is far more accurate that conventional glass gauges on sprayer tanks, which helps farmers ensure they are getting the proper mixes.
Most farmers and custom applicators agree that the sight gauge takes the word “precision” out of precision farming, says Steve Simon of Simon Innovations in Rodney, Ont.
Read Also
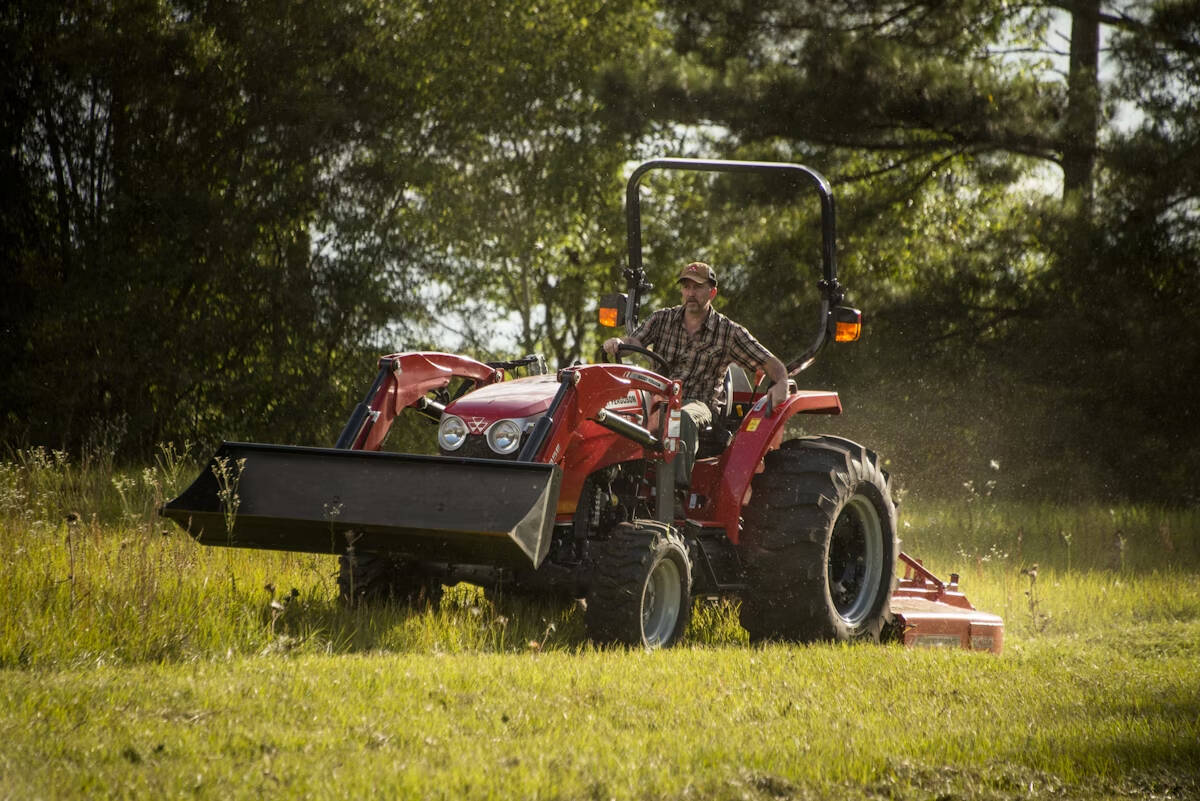
Agco settles legal dispute with TAFE
Agco and Tractors and Farm Equipment (TAFE) from India announced July 1 that they had settled their legal dispute, which began in 2024 over local ownership of the Massey Ferguson brand name and other concerns.
Simon develops and manufactures a range of aftermarket alternatives for high-clearance sprayers. His alternative to the conventional glass gauge is a fully digital system called Accu-Volume, which measures liquid volume down to one-gallon accuracy and gives the information to the operator on a display screen.
“The Accu-Volume system does for spraying what precision planters did for seeding,” Simon said.
“It’s a live display of every single gallon of solution within your sprayer’s tank.”
The digital display shows the operator every gallon in the tank.
“Typical technology on a brand new half-million dollar sprayer is a clear plastic hose running next to a sticker up the side of the tank,” he said.
“That’s all we’ve had for the past 50 years. Nobody’s even come close to making it accurate or making it digital.
“So six years ago I developed this Accu-Volume system. It’s a single sensor mounted in the bottom of the sump, and it weighs the solution in the tank. It doesn’t matter what angle or slope the machine is on, the display shows the operator every gallon going into the tank so he can load it precisely. If he needs 876 gallons in his batch, the operator can load that exact volume instead of guessing from a sight tube, which can be 50 or even 80 gallons out on any given day.”
Simon said the system measures the pressure exerted on a sensor at the bottom of a column of solution. More gallons produce more weight. Different solutions have a different weight.
To compensate for that fact, the system includes an integrated density conversion chart within the system that calibrates for different products. Simon said only two basic calibrations are needed to cover all products. The sensor is not affected by foam in the tank or tank angle.
“(It) is hard-wired to the display because radio signals, like this cellphone we’re talking on today, just can’t be relied on,” he said.
“It’s about an hour and a half to install and another 40 minutes to calibrate. For US$2,900 you can eliminate all that guesswork on liquid volumes.”