Glacier FarmMedia – As better corn headers and straw choppers leave a cleaner surface and eliminate the need for residue-busting tillage implements, cultivators can get back to the job of performing primary tillage.
That’s the premise behind Horsch’s new Omnis FT primary tillage line being launched this fall, says company rep Jeremy Hughes.
Increasingly tough corn stalks have made for the need for increasingly aggressive primary tillage tools, most with coulters. There are now tools which do a better job of managing residue at the corn head, such as corn head stalk choppers.
Read Also
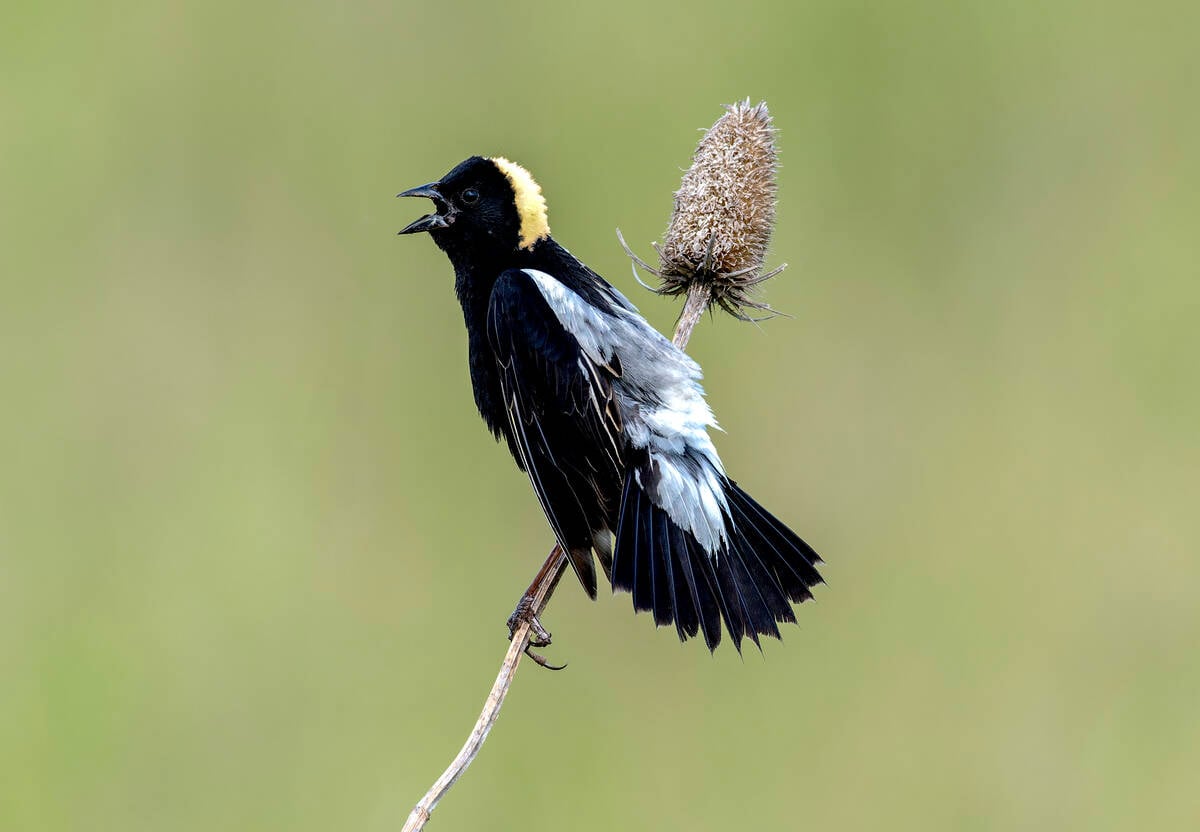
Canada and Ontario invest $14.6M to boost farmland resiliency and sustainability
Canada and Ontario increased investment of $14.6 million to help farmers improve soil, water, and biodiversity through the Resilient Agricultural Landscape Program.
Hughs said the Omnis FT is designed to break up compaction and provide consistent soil tilth in conditions where residue has already been properly sized and distributed by the combine.
“Harvesting technology today has evolved to effectively manage crop residues, whether it be through fine-cut straw choppers or through chopping corn heads. With proper sizing and uniform spreading of crop residues, the combine provides the initial first step of seed bed preparation,” Hughes said.
“After the combine, primary tillage is the next step toward making a seed bed for the next crop. By having residue already sized during harvest, the Omnis FT uses shanks only for tillage.
“We don’t need those big blades on those disc rippers to deal with Bt corn residue because corn producers now have chopping corn heads to size the residue at harvest. In small grain production, we have a new generation of fine-cut, wide-spread choppers on combines. So that has changed everything. The disc ripper is obsolete.”
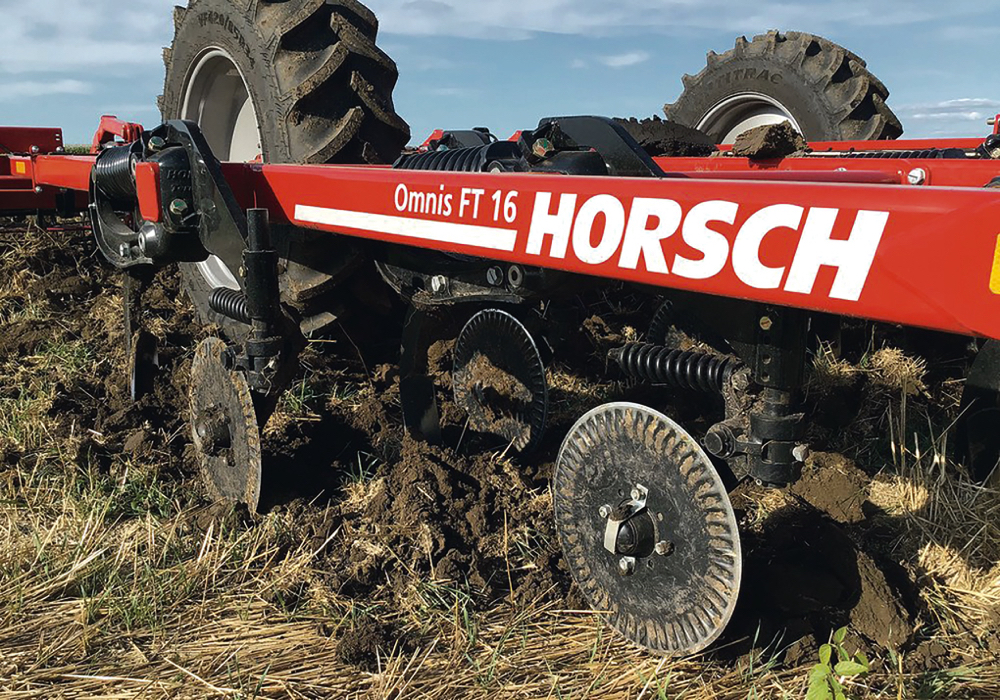
He said in situations where residue has not been handled by the combine, the Omnis’ four-rank design with shanks on 15-inch centres makes a 60-inch in-line spacing that allows all residue to flow through without hanging up.
Hughes said the Omnis FT performs horizontal tillage, which is different than ripping. North American farmers who had seen the Horsch European tillage concepts at work expressed a need for the same horizontal fracture rather than ripping the soil, he added.
“We’ve been working in North America with various European primary tillage techniques along with analyzing domestic technologies for several years. One of the unanimous points of feedback we’ve gotten over the years is the desire for thorough horizontal fracture and tilth versus ‘ripping’ the soil.
“Omnis is an evolution of several different European concepts that we’ve assembled in a domestic platform. Farmers really took a shine to what I call ‘thorough horizontal fracture.’
“When you see some of these big in-line disc rippers at work, they have a tandem disc and a sub-soiler type setup. You may crack a little bit of compaction, but the space between those shanks is so wide that there’s not much horizontal fracture. What you end up with is vertical compaction, which is a restriction for roots. You get a big V, which that wide space shank has created. So yes, you get some loose soil there, but you also have restricted areas in that hard sidewall compaction between the rows.”
Hughes said the act of “ripping” does nothing to promote uniformity in soil structure. With the Omnis FT, soil can be tilled down to 11 inches thoroughly across the entire working width of the machine, giving a fully tilled uniform soil structure. This provides uniform water infiltration, uniform soil warming, uniform residue/soil blending and an unrestrictive environment for optimum root penetration. He said the Omnis leaves no sidewall compaction.
Omnis employs a unique shank spacing compared to other shank-type primary tillage layouts. Horizontal fracture is achieved by four ranks of shanks spaced on 15-inch centres with 1,800 pounds of trip force. Each shank is equipped with Horsch MulchMix shins that aggressively turn and mix soil and residue. This results in uniform soil structure and accelerates decomposition. A variety of tips are available along with bolt-on sweeps.
“The Terra-Grip 3 shank is the product of more than a 20-year evolution. That angle of engagement down at the tip is very important in how you work the soil. We’ve figured out that 35 degrees tip engagement is the ultimate for lifting soil and mixing soil. If it’s flatter, you’re basically dragging your knife through butter. A steeper angle wastes horsepower and has a pushing action in the soil instead of a lifting action.
“You don’t have to go down to 11 inches. If I’m working in soybeans, for instance, and I only need to go down six inches, you can bolt on the wings and go out and get good horizontal soil mixing down to the desired depth. If you need to go deeper in a different field, you just undo the bolts on the wings and you’re good for 11 inches.”
Hughes said one of the advantages of the Omnis FT is its ability to work at different depths. It can go down to 11 inches for breaking up compacted zones or can run shallower, depending on the intended effect. Another feature is the large-diameter tires for transport and field operation.
“One big complaint we hear with primary tillage tools is tires. Small tires on a heavy machine results in getting stuck. Large diameter tires give a tremendous advantage in those unexpected circumstances.”
A range of finishing tools is available for different field conditions, with a choice of rolling baskets, levelling tines or a three-bar heavy harrow for the rear. An optional rear hitch is available for towing a fertilizer caddy or a pull-type finisher.
“When looking at the basics of what we want to accomplish with primary tillage, the first is to accelerate decomposition of harvested crop residues and second is to start the creation of a uniform seed bed soil structure.
“Optional cutting coulters are available if you’re working in longer, less-prepared residue conditions. With the cutting coulter option, one coulter is dedicated in front of each shank. We learned over the years with air seeders that one coulter in front of each shank makes for cleaner residue throughput.”
The Omnis FT was engineered and built at the company’s factory in Mapleton, North Dakota. Sizes include 11-foot rigid, 16-foot rigid, 21-foot rigid, 21-foot folding and 26-foot folding versions.
This article was originally published at the Western Producer.