As Europe aims to slash herbicide use, some equipment developers are looking to weeding robots as a solution.
Those developers, however, say misalignments between individual farmer needs and equipment designs need to be addressed.
Why it matters: As in Canada, ensuring robots match the needs of farmers working in different conditions, and that adequate support is available, are major challenges for European developers.
Such sentiments, reflective of ongoing discussions in Canada, were presented during a June virtual seminar featuring European ag-tech company representatives and their opinions on the state of autonomous field technologies.
Read Also
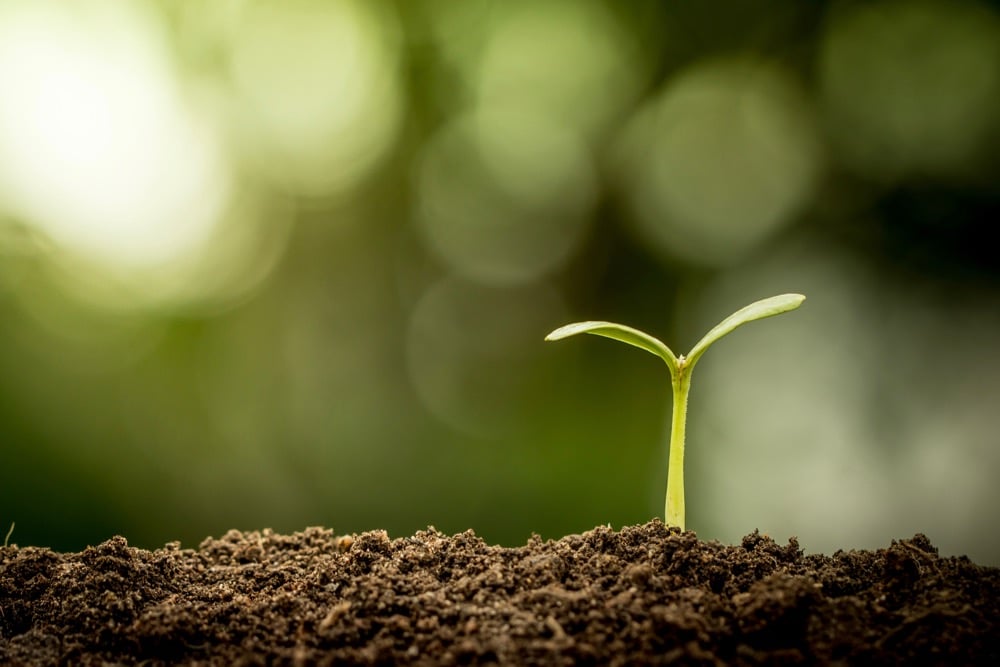
Ontario’s agri-food sector sets sights on future with Agri-Food 2050 initiative
The first-ever Agri Food 2050, a one-day industry event dedicated to envisioning the future of food and farming in Ontario,…
According to event organizers, the subject of mechanical weeding in Europe has “increasingly been in the spotlight as a true alternative to herbicide application.”
They add while such systems have become more sophisticated and progress is rapidly increasing, limitations for these and other technologies still exist.
Two questions were posed: Which robotic systems are closest to practical application, and what are the biggest obstacles hindering broader adoption of such tools in crop production?
Answers to the first question were varied, though a general understanding that scale — both of field and of equipment — is a critical factor.
If the two match, that is, Europe’s farmers will buy. If not, they won’t.
René Jorgensen, chief executive officer for Danish robotics company FarmDROID, says more than 50 of his company’s FD20 autonomous seeding and weeding robots are in operation on Danish and German farms. Each solar-powered, 24-hour operating-time unit is designed for fields up to 20 hectares (50 acres), and left in the field rather than moved between areas, although the latter is possible.
“That’s the whole concept, to free the farmers from manual weeding…. If you don’t need to move it, you can just leave it there,” says Jorgensen.
“It’s 450 to 950 metres-per-hour speed. Compared to traditional farming equipment we drive at a slower pace but for a long time.”
For fields on the smaller side, a reality in many parts of Europe, he says different-sized units are likely required. The same applies to substantially larger fields.
“Farmers have said they had success with larger areas than 20 hectares. We are looking to expand that with new designs.”
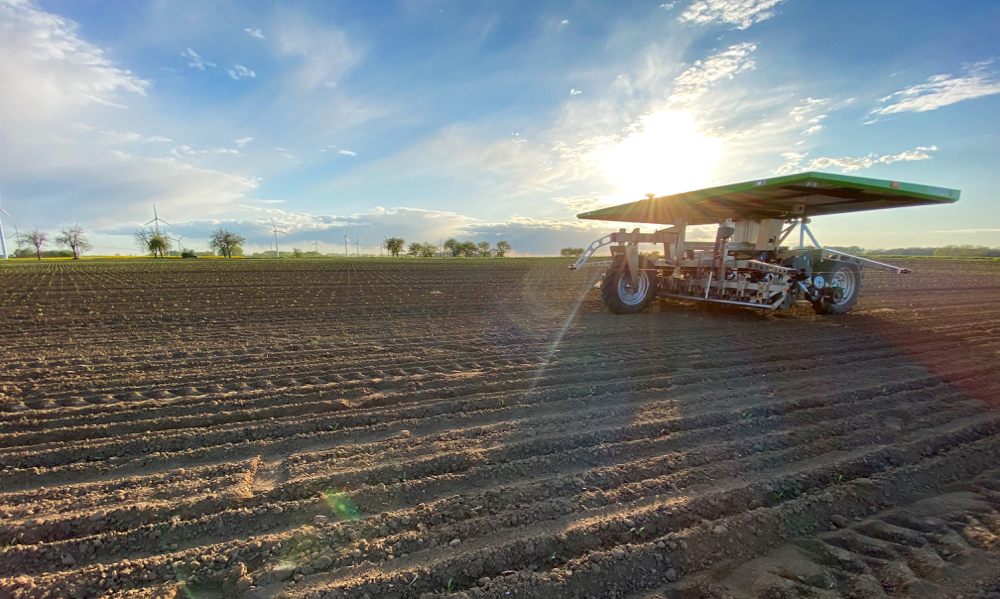
Another designer, Christian Kirchhoff, speaking for German ag-tech company K.U.L.T, emphasized “swarm” style technologies are increasingly popular in jurisdictions where farm sizes are comparatively small. He specifically highlighted France as an example, where domestic subsidies support small-holder farmers buying such equipment.
“The robotic world is not only small machines… We have to include big units,” he says.
Rather than buying entirely new units, Kirchhoff says augmenting equipment already owned by farmers continues to be a common method of incorporating robotic systems. This, and scaling technologies to the appropriate size for buyers, are a focus for his company.
“A business idea for us is to sell all kinds of robotic weeding tools to other companies,” he says. “It’s very important to know what farmers can use and adapt tools to their local conditions.”
European and Canadian adoption obstacles
As in Europe, the issue of scalability is often mentioned as a barrier to adoption in Canada. The specificity of tasks for which robotic equipment is designed is another problem in both jurisdictions, particularly given the price of new technologies.
The price of FarmDroid’s FD20, for example, is €65,000 (C$100,000).
While some European growers have found enough savings to invest in it, for many others, traditional methods of seeding and weeding are preferred.
Jorgensen says the cost makes sense for farms of 10 hectares (25 acres) or more, but not for less than that. Discussing acreages of that size keeps the technology more within high-value production, like vegetables.
However, even if the cost of the new technology pencils out, support issues remain.
Arno Ruckelshausen, a physicist and university professor specializing in agricultural technology, asks whether developers have considered all the nuances required for farmers to actually use them with efficiency and proficiency.
“Let’s assume the robots work perfectly…. If the robot is left on the field, will it be there the next morning? Is there a charging station at the field? Remote service? What is needed? What has to be solved?”
He pointed specifically to the FD20, which requires an in-field charging terminal, installed and serviced by FarmDROID, in order to continuously operate.
Several speakers say they are continuing to address practical concerns like serviceability. Some operational problems can be fixed remotely, such as with the Canadian-developed DOT Power Platform.
Jorgensen says the physical limitations of their products are considered in sales, where distributors visit sites to determine whether robots can meet requirements. Steep slopes can be a problem, for example.
Through the entire discussion and question period, concerns about farmers being able to support themselves were expressed by presenters and viewers.
As well, many expressed concerns about adopting new technologies before such questions are answered and before new technologies are refined.
To paraphrase another contributing speaker, the early days of milking robots showed what can happen if something is adopted too early — some farm businesses ditch them in favour of older systems, while others simply fold. However, after years of refinement, milking robots are now commonplace around the world.