Glacier FarmMedia – Large farm equipment manufacturers sometimes face disadvantages when it comes to rapid deployment of the latest innovations because they need to maintain brand integrity and so tend to sell proven products.
However, that doesn’t mean they aren’t working on the latest technological developments behind the scenes.
During Agritechnica, John Deere used its Future Technology Zone to show how it is researching and developing farming systems of the future.
“In this area we talk about the future, how it could be, how it will be,” said Martin Stauch of John Deere.
Read Also
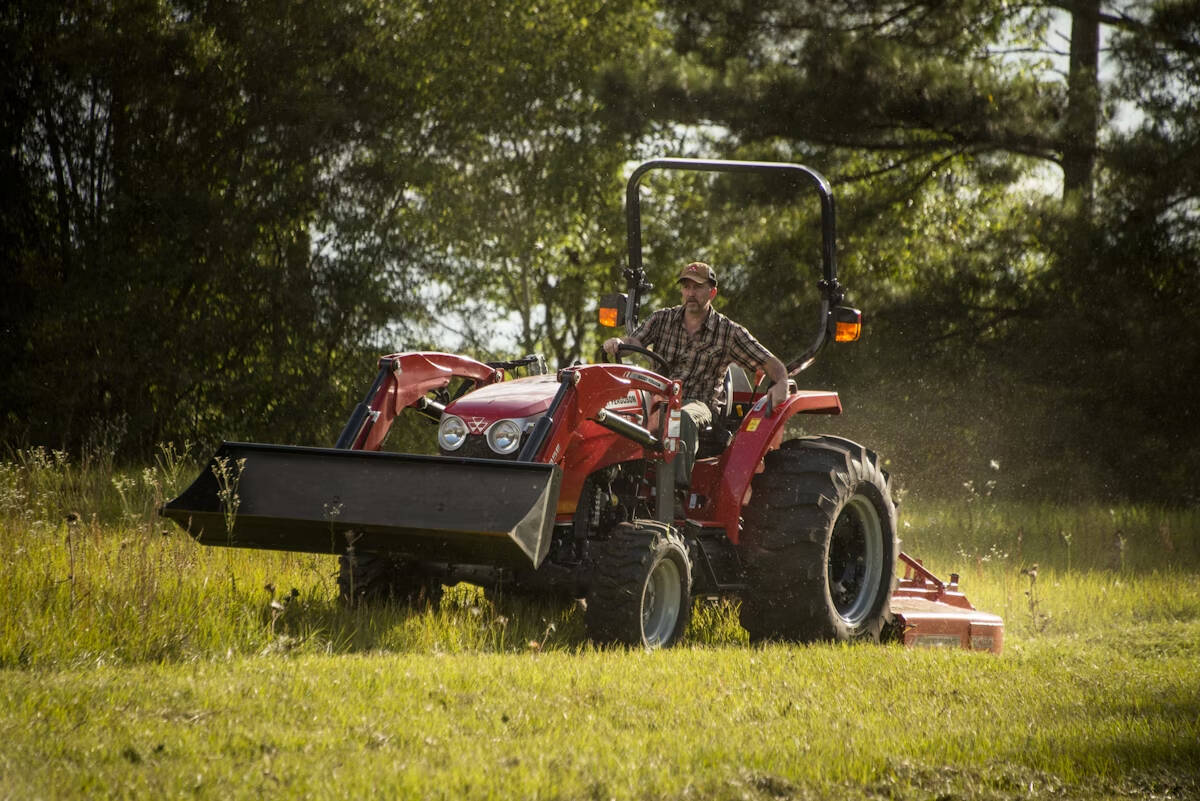
Agco settles legal dispute with TAFE
Agco and Tractors and Farm Equipment (TAFE) from India announced July 1 that they had settled their legal dispute, which began in 2024 over local ownership of the Massey Ferguson brand name and other concerns.
“What you will see is a lot of concepts around electrification, artificial intelligence, automation and autonomy.”
Most of the products displayed in this booth are nowhere near commercialization, but they are all at least in the prototype stage and being researched in field conditions.
Of these products and concepts, the closest to market is the new John Deere eAutoPower transmission, which is the first electro-mechanical power split transmission that makes tractor-implement electrification possible.
The German Agricultural Society awarded the eAutoPower transmission the only Gold Medal for new product at Agritechnica.
There was a working model on display, which is also the durability test hardware the company uses to test how the system holds up when installed in a John Deere 8R tractor.
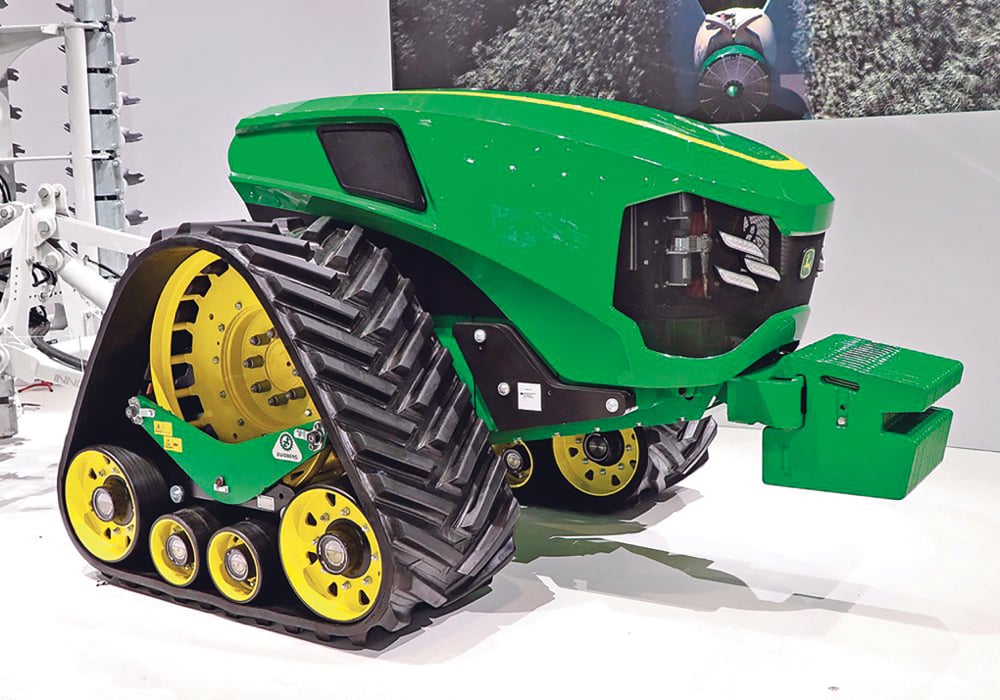
“This is more than just a model at Agritechnica. We’re in test and going to production within a couple years,” said Curtis Jensen, John Deere program manager for E-auto Power.
“Essentially, we replaced the hydro module, and we replaced it with two permanent magnet electric machines that you see on top of the transmission. The electric machines are powered by the inverter. The top inverter actually provides the control and power for the electric machines on the transmission.”
The bottom inverter is used to take up to 100 kilowatts of power off-board to power implements such as the Joskin manure spreading trailer.
“We call them motor generators — MG1 and MG2,” Jensen said.
“MG1 is connected to the engine shaft and MG2 is connected to the inside of the transmission to provide the variability. They can both act as motors or generators.”
He said in terms of efficiency the transmission is comparable to a hydro-mechanical transmission.
“But there are certain operation points where when you’re running with a partial load like you are with a hydraulic IVT, that this will be significantly better,” Jensen said.
A design feature has power shifted from the tractor to drive implement wheels.
In the case of the Joskin trailer, the electric engine is connected to a drive shaft that powers the trailer’s two axles.
However, implements such as seeders could also be fitted with electric drives on their wheels to increase traction.
“You can now take ballast, say up to two to three tonnes of ballast off the tractor, and leverage the ballast on the trailer, and go from maybe a six metre to up to a nine metre tool,” Jensen said.
He said the draft force for ground-engaging tools goes up exponentially as the rate of travel increases.
So if the tractor travels slower, it’s able to pull a wider implement.
“We’re seeing up to 30 to 40 per cent more productivity, at maybe a 15 to 20 per cent lower cost because we’re not wasting the power in slip,” Jensen said.
“If you get a tractor like this and you’re going up a hill, for example, and you can’t pull the load, that’s wasted energy.”
The controls of the implement drives are integrated into the tractor controls.
“The operator will simply push a button,” he said.
“Do I want low, medium or aggressive traction? So you can dial in to, say, have two per cent wheel slip, or if you don’t want it that aggressive, you can dial it back a little bit.”
He said they accidentally demonstrated during the test phase that when the tractor gets stuck, operators can pull themselves out with the implement simply by backing up.
Much further away from being commercially available is the autonomous electric tractor concept that John Deere had on display.
The compact electric drive unit, which requires 500 kw of power, was shown with an integrated tillage attachment.
“Two hundred and fifty goes to the tracks, 250 can be off boarded to other components of the systems either by p.t.o., or hydraulics or off-boarding in case the tool can use electric power as well,” Stauch said.
The autonomous tractor can be equipped with either wheels or tracks, have five to 15 tonnes of ballast, and will rely on energy sent to drive wheels on the implement for traction.
The idea of this research project is to see what a tractor would look like if the diesel engine and operator were subtracted. There is no fuel tank, transmission and cab, yet the concept tractor can deliver the same horsepower as a John Deere 8RX tractor.
“Our study, where field work is done by a swarm of a lot of smaller units instead of big units, is a research project together with some universities and several other countries,” Stauch said.
A big piece of the puzzle that has yet to come together is where the electricity will come from.
The current prototype uses an expensive cable that is rolled on and off a large drum on the edge of the field, and it would take a huge mass of batteries to supply enough power to the tractor.
Much closer to a viable option is the concept of taking a current production model tractor and outfitting it with autonomous technology.
The autonomous tractor research project “takes a current tractor machine form and provides the sensors needed to operate it safely in an environment like producing olive trees or wines, so that you can run an orchard sprayer safely in this environment.”
Stauch said operators can switch the tractor off autonomous mode and drive it between fields, so very little would need to happen before this could be deployed in terms of new laws or insurance for autonomous equipment on roads.
The autonomous sprayer being developed and tested by John Deere is set on tracks with a 1.5 metre footprint and has variable clearance that goes as high as 1.8 metres, a nine metre boom and a 560 litre tank. It can also travel up to 15 km-h.
“What we’re trying to do is improve the time that we spend in the field, and part of that is a machine that’s very light weight, so we can get in when the soils are wetter, so we can get more run time.”
The robotic prototype uses John Deere’s ExactApply application system, is outfitted with a gas power-plant and uses hydraulic drives on the tracks and electrical actuators to move the boom.
The drone swarm spot-spray concept uses a scout drone and spray drones, as well as a portable base station that automatically refills the drones and changes their batteries.
“One drone leaves, it flies at about 50 metres, scans the field, locates all the weeds in the field and returns. It transmits the location of all the weeds to the rest of the drones,” said Aaron Wells of John Deere.
Once the prescription and flight patterns are received, the spot-spray drones will then automatically pull in the correct chemical for a specific job from one of the three 60-litre tanks, as well as water from the 1,000 litre water tank in the bottom section of the base station.
The base station can be loaded on a trailer and transported to the field, or it can be set in a permanent location, such as beside existing water- and chemical-handling facilities.
Wells said the spot-spray concept is scalable.
“You can also have as many or as few of the drone boxes that would make sense for the operation, as it’s scalable to right size it to whatever your operation looks like,” Wells said.
“The idea is that you could deploy these around your operation in the morning and pick them up the next day, the next night, two days later, however long it would take them to accomplish the job you had for them.”
This article originally appeared at the Western Producer.