The number of uses for 3D printing in the agriculture sector continues to grow as expired process patents, better materials and greater awareness of the technology allow more people to bypass traditional barriers and inefficiencies in parts manufacturing.
Companies from many sectors have found 3D printing to be a cost-effective method of prototyping new parts and the dollar cost of doing so has continued to decline.
Why it matters: 3D printed products and the computer files of specific items are increasingly being used by large companies and individuals alike, the latter finding value when specific parts are otherwise unavailable.
Read Also
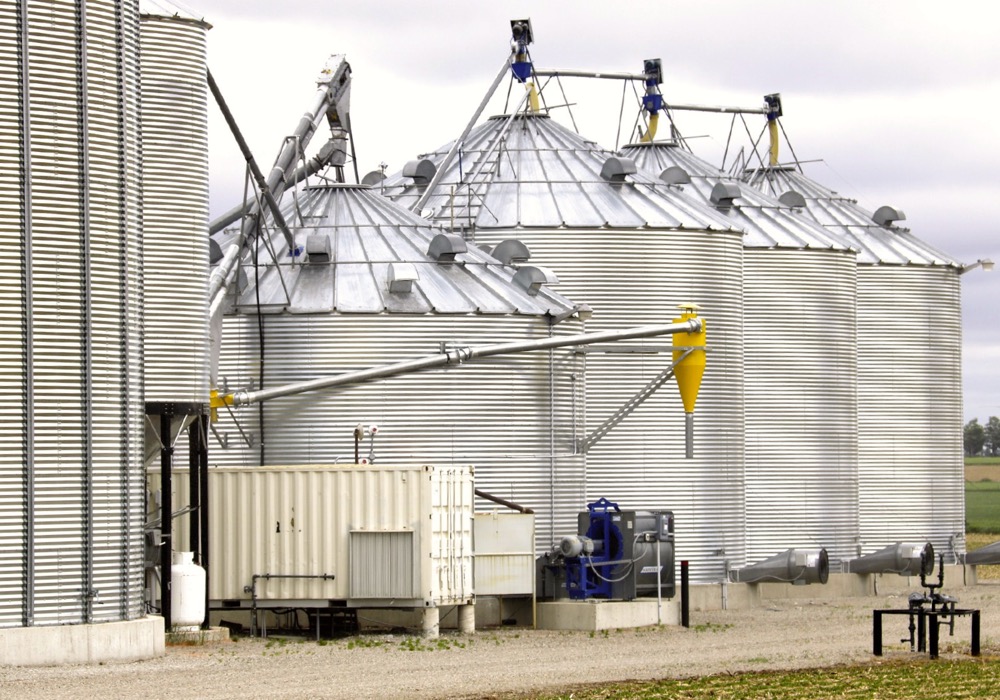
Ontario Agricultural Stewardship Initiative third intake opens in August
Ontario’s Agricultural Stewardship Initiative (ASI)$3 million cost-share program intake opens on Aug. 13 at 9 a.m., helping agriculture, agri-food, and agri-based businesses improve energy efficiency and increase competitiveness, sustainability, and productivity.
Joel Sotomayor is president and chief executive officer of Transport Genie, an Ontario company offering digital monitoring systems for livestock transport. He says the technology allowed his company to bypass the mould-making process when developing more durable in-truck sensor covers.
“It was a pretty seamless process… It doesn’t look like it’s been 3D printed either,” says Sotomayor in reference to work with a 3D printing firm in Hamilton.
“Especially for young start-ups with limited capital, you want to have enough to get feedback from customers without breaking the bank. All you would need is to get someone with knowledge of how to create a 3D printed model. There are many people around. They can help create that part.”
Large manufacturers are no strangers to 3D printing either.
According to Nathan Smeenk, vice-president of operations for Uxbridge-based 3D printing service provider Agile Manufacturing Inc., equipment companies like John Deere frequently use 3D printing and find it a valuable and comparatively inexpensive method of part prototyping.
The process is also increasingly used in direct factory production of plastic parts, with equipment companies maintaining in-house 3D printing capability. It continues to grow in importance as more plastic parts are used in equipment design or when only small numbers of a given part are required.
“The prototype business is worth $5 billion a year. Manufacturing is $5 trillion, so let’s focus on the right area,” says Smeenk, later describing his company’s work on an in-cab floor mat system for John Deere.
“There’s lots of opportunity to produce end-use parts.”
Individuals can also have parts made, or just scanned and mapped digitally. Smeenk provides the example of a tree farmer who employed his company’s services to put together a digital file of a stake-making tool that was otherwise not available.
The grower then machined the part with the file.
Such an approach, he says, could potentially be taken for any unavailable part required on the farm.
Overall, Smeenk says the availability of 3D manufacturing systems has improved as patent protections have expired, leading to more 3D printers being purchased for in-home use.
Actually making a part requires a computer-aided design (CAD) file, and the data for many items are not freely available. And while apps or other digital tools can be used at home to gather data on an object, it still has to be put together as a drawing. Knowledge of CAD development thus remains a barrier.
“It’s not simple. There’s always that extra thing, but that’s what people like us are in business for,” says Smeenk. “There is an educational curve but a lot of it is being addressed by the fact that people are using these printers at home now.”