A 2021 University of Guelph study showed that fuel costs are a top concern of those using grain dryers in the province.
Why it matters: Drying accounts for 17 per cent of the cost of production in grains. More efficient and new strategies are required to keep such costs from climbing.
Project researchers William Lubitz and James Dyck, associate professor with the university’s School of Engineering and engineering specialist with the Ontario Ministry of Agriculture, Food and Rural Affairs, respectively, shared results of the study at a virtual event hosted by Canada’s Outdoor Farm Show.
Read Also
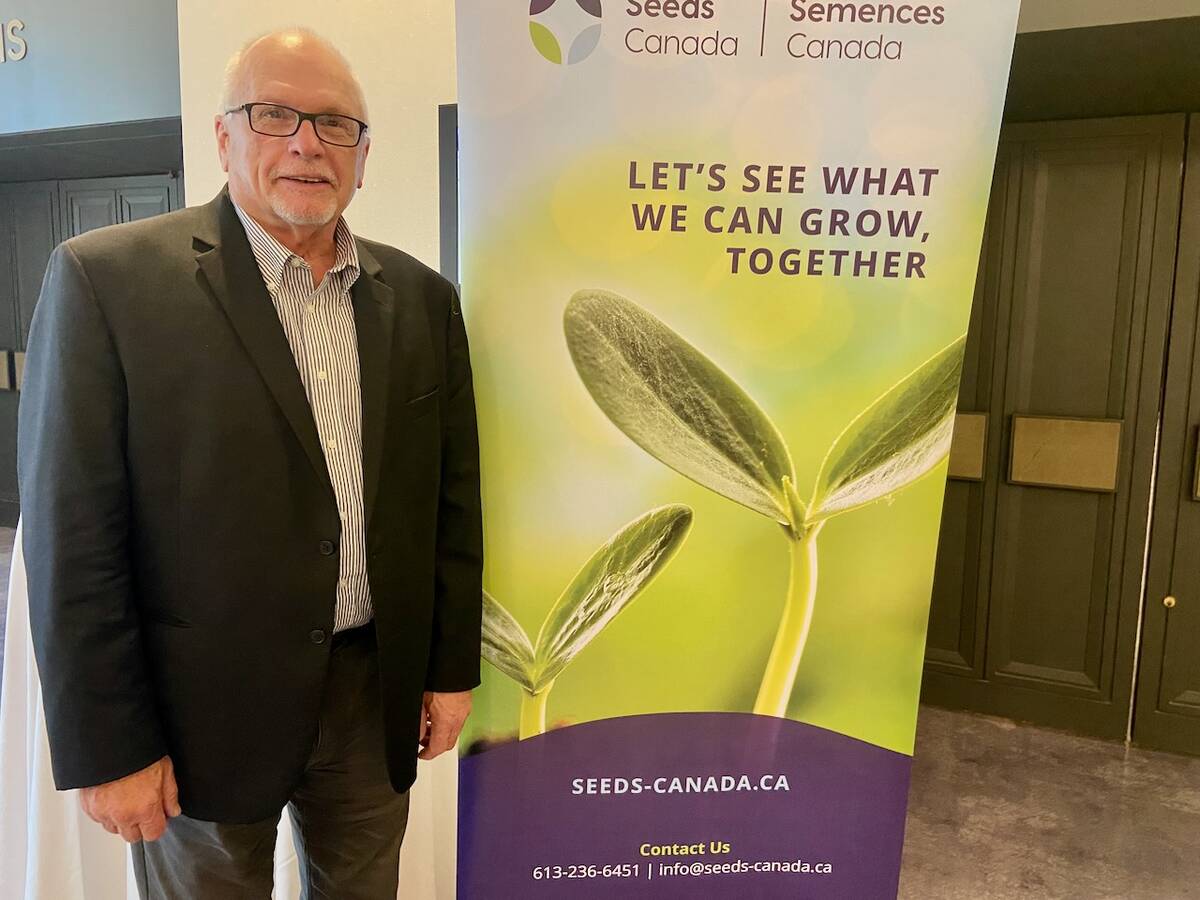
Senft to step down as CEO of Seeds Canada
Barry Senft, the founding CEO of the five-year-old Seeds Canada organization is stepping down as of January 2026.
Statistics Canada reports a total provincial storage capacity of 720 million bushels, with approximately 20 million more added annually. Provincial grain production sits around 600 million bushels.
Corn makes up the bulk of grain that is dried within Ontario’s total storage, followed by soybeans, wheat and other grains.
Researchers want information on the most common types of dryers, their age and location, the amount of drying that occurs on farms as opposed to commercial operations and a variety of other data.
They made calls to farmers, commercial dryers and equipment dealers and did an online survey. With additional information from the grain sector, results indicate Ontario has:
- 381 commercial drying sites.
- One or slightly more than one dryer is the per site average.
- An average of 56,000 bushels are dried per year on each site.
- Natural gas predominates on commercial sites and propane is more commonly used on farms.
- Commercial elevators generally opt for high-capacity continuous-flow dryers.
- Bin dryers constitute the bulk of on-farm drying, though a higher-than-expected number of continuous flow systems were reported.
- For every 100,000 bushels of grain dried, elevators had a 240-bushel per acre capacity. For farms, the number is 500.
Lubitz says many results were not surprising. The preference for natural gas, for example, is understandable given its comparatively low per-bushel drying price (13 to 14 cents for natural gas, or 22 to 23 cents for propane.) Lack of natural gas infrastructure likely accounts for the prevalence of propane in some settings.
Given the high number of bushels dried annually, Lubitz says the data, gathered from 32 elevator operators and 49 farmer respondents, shows results represent grain farmers much larger than the provincial average.
Fuel costs stemming from greater carbon regulation were reported as the most significant concern “keeping operators up at night.” Variability in fuel costs took second place.
Concerns in descending order were: non-fuel related operating costs; labour and service availability; maintenance and reliability; and other concerns. Dust and noise were the lowest concerns.
Farms and commercial elevators generally expressed the same problem hierarchy. Regardless of size and volume of fuel used, the reported per unit cost of drying was consistent.
“No one is really getting a volume discount,” Lubitz says.
Given the rising costs of propane and natural gas, Lubitz says next steps involve evaluating alternative heating technologies and ways of reducing energy use without compromising efficacy. Researchers will also evaluate best management practices for noise, dust and other drying-related concerns.
In the meantime, Dyck encourages operators to seek ways to improve efficiency by investigating their own drying data. This can include comparing fuel quantity with the amount of moisture being removed from grain, or more specifically, water removal with the amount of grain dried, plus fuel consumption.
Best management practices such as cleaning grain and storage areas, keeping to a maintenance schedule, not over drying and retrofitting for heat recirculation, when possible, can go a long way.
Drying tech Q & A, with James Dyck
Q: Could biogas be used for grain drying?
A: Yes. The burner on the dryer would need to be configured for it (proper orifice size, etc.), so it’s not as simple as just connecting to a new fuel source. But it is very possible if you have available biogas to use. If you use an upgrader to bring it to the quality level of regular natural gas, then no burner modifications would be needed.
Q: Since continuous flow dryers are the most popular for farms and elevators, are they the best type of dryer?
A: It’s not really surprising they are the most popular. Continuous flow dryers are available in a wide range of sizes and capacities, so they are well suited to farms of all sizes as well as large elevators. “Best” could be defined in many ways. A good dryer operator knows their dryer (whatever the type) and knows how to operate it efficiently. That said, continuous flow dryers do have some opportunities for increasing efficiency by making use of heat recovery.
Q: How do these costs compare to the drying charges paid by farmers at their local elevator?
A: We didn’t make direct comparisons of total costs. Those aren’t really something people can respond about in a survey. Of course, fuel costs are also included in the costs the elevators have to charge … What’s interesting from the data is that the farms and elevators are paying essentially the same fuel costs. For your own operation, the real question is how your own overhead, equipment costs and labour costs to dry your own grain compare to your local elevator.
Q: What’s the easiest/simplest way to improve the efficiency of an existing grain dryer?
A: Don’t overlook simple maintenance. Keeping the dryer in good condition (and clean) goes a long way towards better efficiency.
Another important point — drying slower has been shown to improve test weight more than high temperature. We usually see a test weight bump when drying, as the water being evaporated is less dense than the grain dry matter. However, slower drying allows moisture to migrate out more gradually, resulting in a slightly denser final grain. It can be a good option if test weight is a concern.
– James Dyck is an engineering specialist with the Ontario Ministry of Agriculture, Food and Rural Affairs.
Updated Oct. 12 to fix an error related to temperature and drying efficiency and to change a title.