A Toronto-based start-up has developed a real-time cattle monitoring system it says will help farmers increase the efficiency of their operations.
Cattle Scan’s Bovine Monitoring Bolus tracks dairy cattle health 24/7 from inside the animal to provide early alerts of potential health issues before the onset of visible symptoms.
Why it matters: Earlier intervention means a shorter recovery time and reduced treatment costs and can minimize or prevent impacts on milk production and animal health.
Founder Denis Tokarev is an electrical engineer by training who designed and built a prototype sensor system to monitor energy infrastructure like transformers, splicers and cables and make the data accessible through Internet of Things (IoT) technology.
Read Also
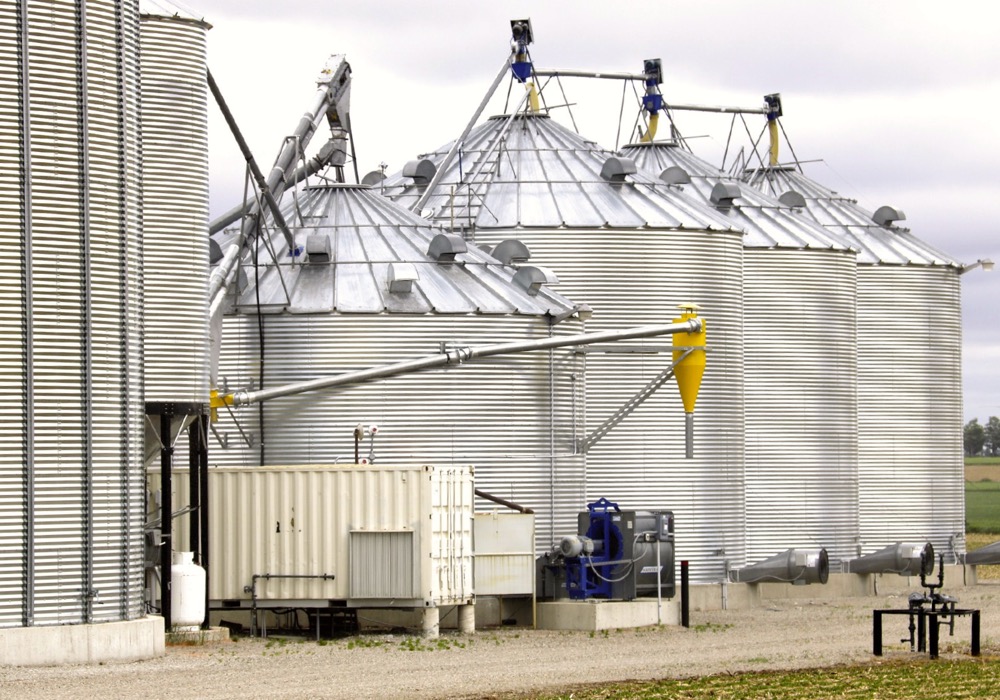
Ontario Agricultural Stewardship Initiative third intake opens in August
Ontario’s Agricultural Stewardship Initiative (ASI)$3 million cost-share program intake opens on Aug. 13 at 9 a.m., helping agriculture, agri-food, and agri-based businesses improve energy efficiency and increase competitiveness, sustainability, and productivity.
According to Tokarev, his solution was ahead of its time from an Ontario energy regulatory perspective, though, leaving him looking for new applications.
“I was looking for an audience with companies that are big enough to gain value from technology but are independent and can make decisions faster – and agriculture is one of them,” he explains, adding he grew up on a dairy farm. “I know how hay smells when I cut it, and to pray for rain to stay away when the hay is on the ground – and I understand pain points (in production).”
He took advantage of the Royal Agricultural Winter Fair by spending the 10 days of the show talking to farmers there about what type of information they would be interested in tracking, and learning about their problems with livestock and how they currently solve them.
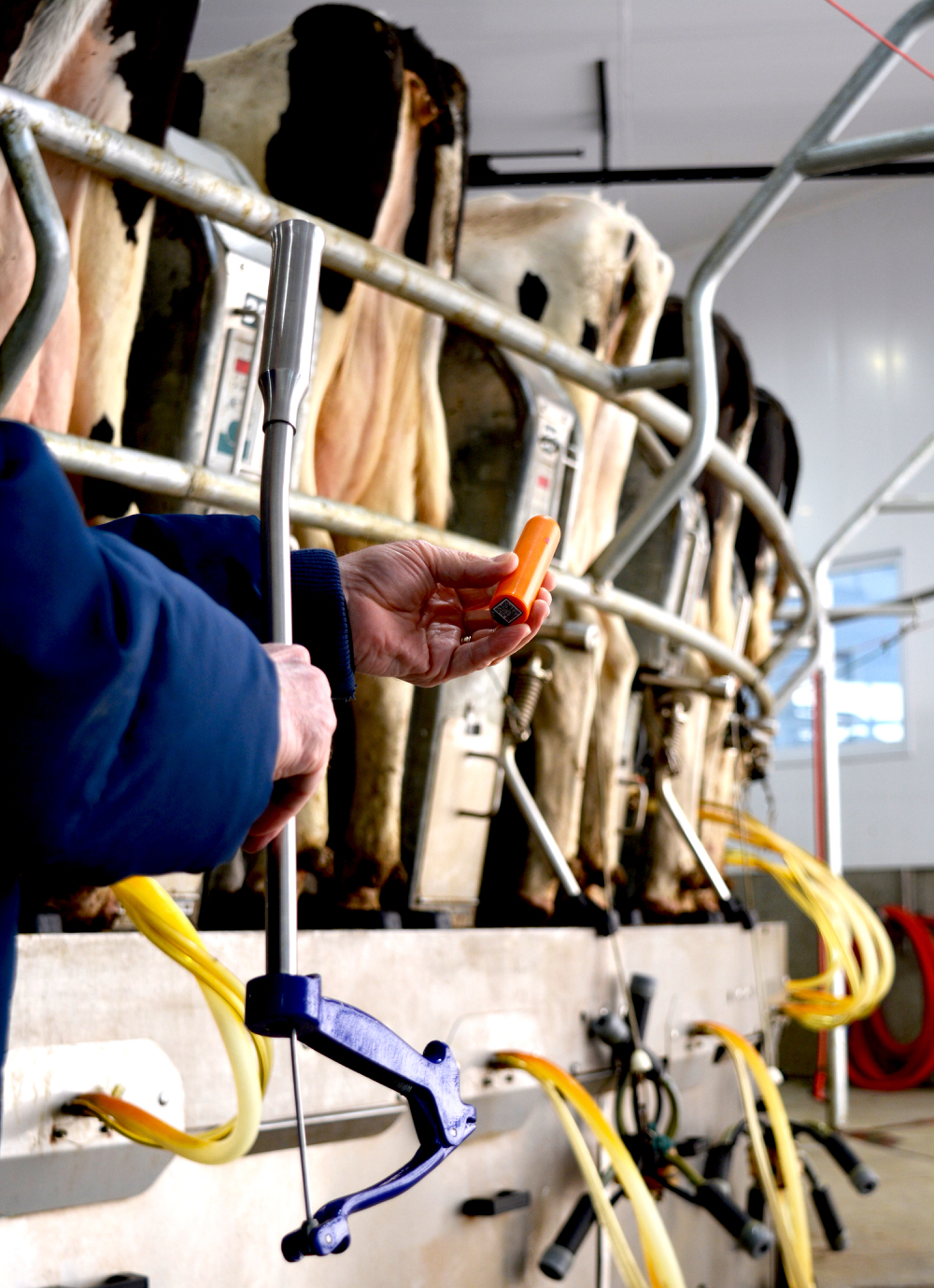
And so, the idea of the monitoring bolus to safely monitor cattle health from inside the animal itself was born. Although boluses in the rumen are used for research, Tokarev says no such technology existed that was affordable and accessible to regular farmers.
The rumen bolus is placed inside the cow orally and can collect and transmit data for five years on its built-in battery. It transmits real-time readings of things like body temperature and water consumption to receivers installed inside the barn. Those receivers transmit the collected data to an on-site computer, and a machine learning algorithm analyzes the data to look for pattern variability.
If something isn’t right, it triggers an alert that is sent to an inbox or mobile phone. A web-based dashboard provides herd-level and individual animal information.
“Our goal isn’t to just create another screen. Farmers have so many screens and attention-dragging systems, we want to take some worries off their plate so that when they’re not in the barn, something is still looking after the cows 24/7 and analyzing what is going on,” Tokarev says.
The ideal time to place the bolus is in a couple of months before first calving. Because that’s such a stressful time for dairy animals, that’s where Tokarev sees the early alert system as providing the most value to a farm. Farmers pay for each bolus and the receivers, as well as a data subscription for the analytics.
Bloemen Farms near Lucan, a dairy milking 500 cows in a rotary parlour, began using the system on a pilot project with Cattle Scan last fall, with 40 boluses placed in dry cows and springing heifers.
“I believe most of the benefit runs around the first few weeks after calving. If you know the internal temperature on the cow or the amount of water she took in, it can be another tool in terms of how to make decisions on the farm around that cow,” says herd manager Hank Janson.
He believes the system’s effectiveness depends on a farm’s size, its systems, and its management philosophies, but would be especially well suited to robotic milking dairies or where farmers split their time between the barn and field work.
For him, an ideal add-on to the system would be for the alert to also trigger an automatic sort of the animal in question for further follow up. Currently, that step must be done manually.
“If you’re going to automate, automate to the max,” he says.