Despite exponential increases in the technology’s effectiveness — and widespread use in other industries — battery power and charging challenges continue to limit the scalability of electrically-driven farm equipment.
That doesn’t mean diesel will always reign supreme, though.
According to three Ontario Ministry of Agriculture, Food and Rural Affairs (OMAFRA) technology experts, electric motors have the potential to play a major role on the farm if approached strategically and on a smaller scale. That is, looking at what equipment one has, if it’s being used efficiently, and whether electric technology can improve that efficiency.
Read Also
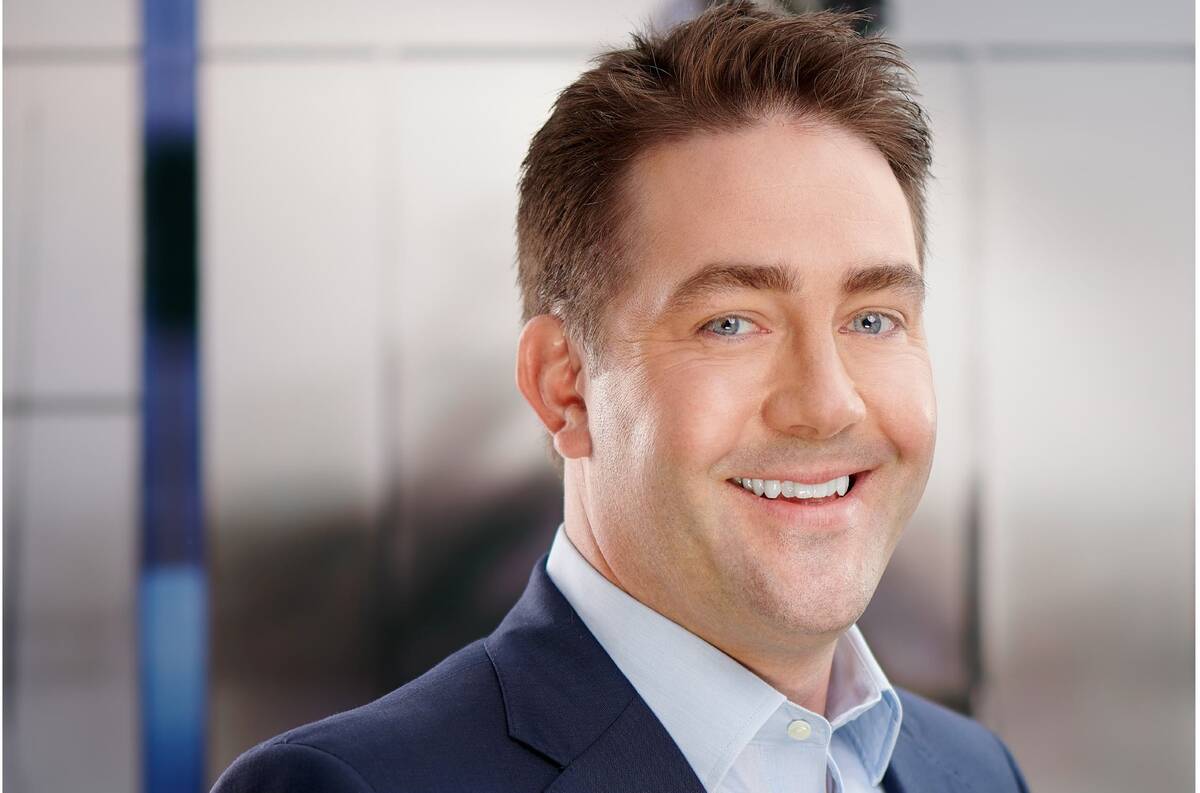
Now is the time for Canada to rediscover its agricultural edge on the global stage
With the right policy support for precision agriculture adoption, Canada can reclaim its place as a global agricultural powerhouse.
Electric not yet suitable for heavy-duty field tasks
Electric power for industrial applications is not new, says James Dyck, crop systems and environment engineering specialist with OMAFRA. Most modern railway locomotives, for example, are hybrid vehicles driven by diesel-powered electric generators. This is because electric motors have a “distinct advantage of high torque at low speed,” which suits the work required of locomotives as well as tractors. There are also fewer moving parts associated with electric motors in general, which Dyck says can reduce equipment weight and overall mechanical issues.
Why it matters: Scaling-up electric-drive technology for large tractors and higher-torque work is not currently feasible. However, strategically swapping diesel for electric power on a smaller scale is. With the right price point, this saves money.
But it all requires energy storage, and that continues to be the major barrier.
“Battery life is dictated by load. Mowing the grass in an orchard, for example, is low load so the battery could last a while. Pulling a tank of liquid manure or a piece of tillage equipment is much higher load, and the battery will run out much quicker,” he says.
Dyck adds autonomous battery-powered tractors could automatically go back for charging, but additional tech to monitor battery condition, tractor location, and other factors would be required. The down-time during long recharging periods is another factor to consider.
“Electric motors are a fairly mature technology. There are always small changes and efficiency improvements, but improved battery tech and charging speed are two of the main opportunities which would lead to more widespread adoption of electric power,” says Dyck.
Opportunities at lower scales
Dragging iron through the field isn’t the only job on the farm, however. Indeed, picturing electric-drive technology solely in this respect ignores other opportunities where electric motors could make a significant — and immediate — difference.
In a joint interview, Ian McDonald and Alex Barrie — crop innovation specialist, and project engineer (in training) in the engineering development program with OMAFRA — agree the ability of diesel to move an implement through the soil is hard for electric power to match. Problems with electric engines in cold weather, they say, are also not unheard of.
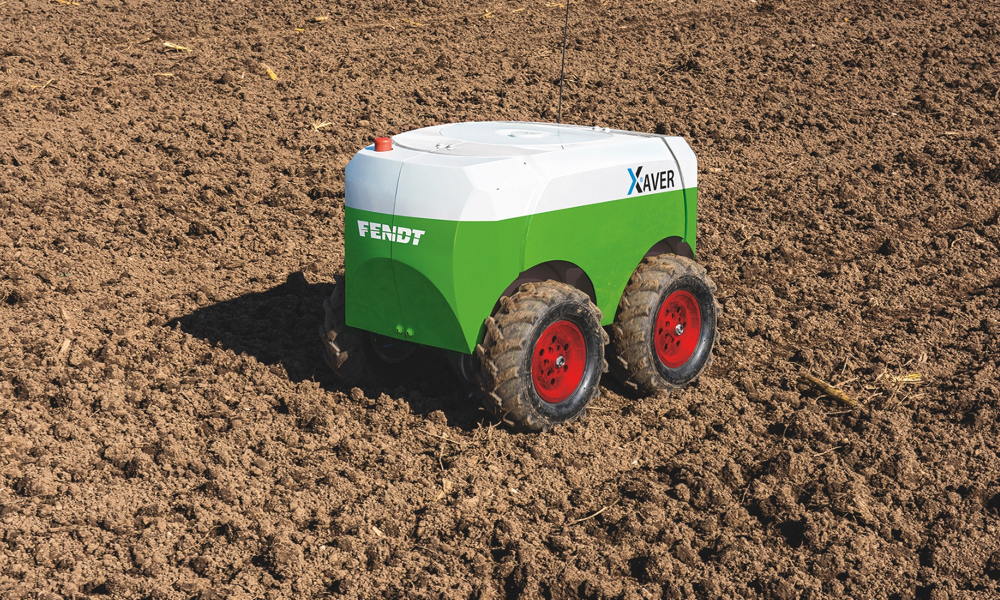
However, they believe electric motors are perfectly suited for low-duty tasks, such as operating manure pumps and shuttling implements around the farmyard.
“You don’t need to tie up a tractor for that kind of job,” Barrie says, adding other sectors like the automotive industry have a long history of adopting electric motors in this way. McDonald adds scalability issues will also continue to decrease as smaller, autonomous machines (such as the DOT Power Platform or Fendt’s Xaver “swarm farming” units) become more common.
“We are on the cusp of a disruptive scale change in farm equipment and this little stuff will be solar electric and won’t have to, for instance, dig a trench along the entire length of a field to plant corn. It will just poke individual seeds into the ground at predetermined places,” says McDonald.
Dyck, McDonald, and Barrie reiterate electric motors are already replacing things like traditional hydraulic systems. This is a very low-scale example, they say, but it also highlights how the technology can be used in non-tractor form. There are also many opportunities for farmers to employ stationary electric motors where tractors might otherwise be used.
A livestock producer, for example, could use a standing electric motor in place of a tractor to scrape lanes within the barn. A grain grower could use one to run augers and other power-take-off systems. Both examples would free a piece of equipment for use elsewhere.
Pound for pound, McDonald and Barrie say more can be done with electric power on this scale.
Cost-effectiveness critical to adoption
Developing a true cost-benefit analysis on what equipment is being used, how much it costs to use it, and how else it could be employed is critical. Barrie says factors such as fuel consumption costs and reducing how many hours a piece of machinery accumulates while idling should be accounted for — particularly the latter if trying to maintain higher resale values.
Fundamentally, the cost of the apparatus, whatever it might be, is the other limiting factor. In order to really take off, says Barrie, electric motors need to be in the 60 to 100 horse power range, while being cost effective.
“I don’t want to buy something that can’t handle [the job],” he says.