Glacier FarmMedia – A new spray boom recirculation valve promises to reduce sprayer clean-out time to five minutes, and eliminate dumping rinsate and active product on the ground.
The Sectional Recirculation Valve (SRV) was developed by the Drift Reduction Technology (DRT) Corp. in Wisconsin. The company focuses exclusively on improving the safety and accuracy of applying crop protection products.
Although Original Equipment Manufacturer (OEM) boom recirculation systems have been around for a while, the SRV2 maintains aggressive recirculation when it’s needed most, during spray application.
Read Also
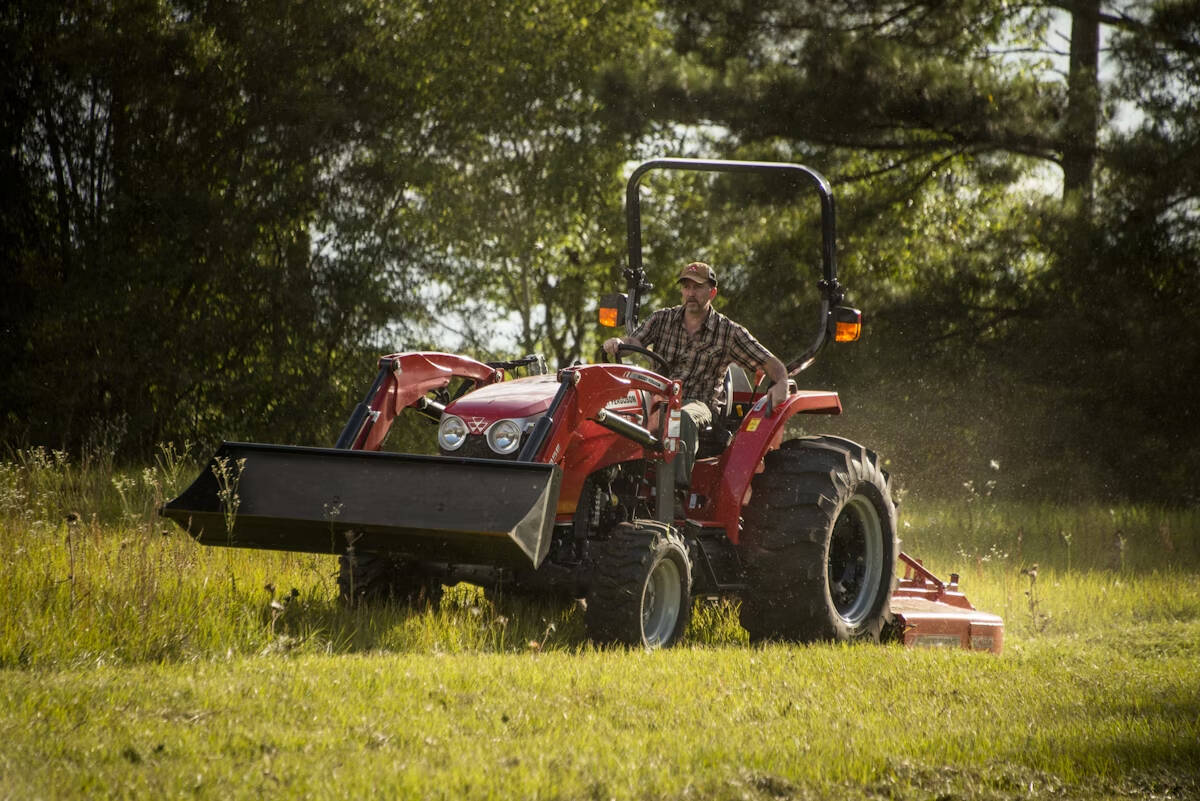
Agco settles legal dispute with TAFE
Agco and Tractors and Farm Equipment (TAFE) from India announced July 1 that they had settled their legal dispute, which began in 2024 over local ownership of the Massey Ferguson brand name and other concerns.
A main benefit of the SRV2 is that the operator does not leave a 30- to 50-gallon patch of chemical mix on the ground. All clean-out liquid is sprayed out on the field for which it was designated.
According to DRT, in the time it takes an operator to get out and physically open all flush valves or remove end caps on a conventional system, the entire machine using SRV2 technology can be thoroughly flushed and ready for the next field.
Rinsate can immediately and responsibly be sprayed on the field. Cleanout takes only a few minutes, even with dicamba or other highly volatile products. The operator is never exposed to hazardous materials, says DRT owner Kurt Kamin.
The heart of the system is the SRV2 valve installed in the line feeding each boom section. At the two ends of each section, the end caps or flush valves are eliminated and replaced with 180 degree end sweeps that shoot the fluid back to the central SRV2 valve. Sweeps eliminate areas where chemical may want to hide during cleaning.
Spray fluid enters through the SRV2 valve on the way into the boom section. DRT’s 180-degree sweeps turn the liquid around and send it back to the valve through polyethylene hose. The design uses polyethylene because it won’t retain any residual chemical.
Kamin says, “The fluid comes back to our valve, where the inductor actually does the work. The inductor creates the suction to bring the fluid back around while you’re spraying. We have about a two-pound pressure drop across the valve while it’s spraying. That’s the amount of energy the system gives up to make this all happen.”
To verify that his system performs as claimed, Kamin hauled a sample boom section outfitted with SRV2 valves, from Wisconsin up to nozzle guru Tom Wolf of Agrimetrix in Saskatoon. Wolf observed the demonstration and later reviewed the trial results.
Kamin says, “We’ve proven with testing we’ve videotaped that three minutes into running clean water through that section, we’ve diluted the dye down to 20,000:1 parts per million. That’s the ratio they’re calling for on dicamba and 2,4-D. Once you’re running clean water through the valve, you just run it out through the nozzles in the field. The valves can have the sprayer clean and ready for the next chemical in the time it normally takes to get out of the sprayer and down to the ground.
“EPA (U.S. Environmental Protection Agency) says you can have 30 parts per million per square foot. If you dump raw chemical on the ground, you’ve just exacerbated that number by 10 million.”
Kamin says the system re-circulates while it’s spraying. Once the liquid enters the boom through the SRV2, nothing goes back into the tank. It also has a high-flow bypass built into the SRV2 valve. Fluid always goes through the inductor. In situations where high volume is needed, such as 32 per cent at 30 gallons per acre on corn, the valve can accommodate that.
“The real breakthrough will be our direct injection into each individual section. We’re developing a system to change the chemical rate right down to the section level. As the fluid goes racing around a boom section, we meter in appropriate chemicals on the go. You won’t create that huge V-pattern,” says Kamin.
“The valve has merit to stand on its own, simply as a quick and thorough clean-out device.”
Installation is a matter of loosening a banjo clamp, spreading the hose lines apart two inches, slipping the valve into place and then tightening two banjo clamps.
The basic SRV2 valve is available now. The model with a direct chemical injection port is expected to be on the market in July, although COVID-19 may delay those plans.
The system can be retrofitted to any new or used field sprayer. It’s installed with one kit per boom section.
The price is US$595 per section, which includes all hose and hardware. For further information visit: drt.ag.
How the SRV2 works
This SRV2 valve allows for constant recirculation in a closed loop at the section level. While spraying, the fluid recirculates around the section keeping constant agitation.
Cleanout of the section is accomplished by flushing the section with clean water and spraying the product out on the field where it belongs. This eliminates flush valves and/or end cap maintenance.
If chemical injection is used the system can be cleaned out and switched to a new chemical in about four minutes.
Water comes in from the tank at the top of the valve. The next hole down on the left side is for chemical injection. The larger hole on the left side is the return from the end of the section lines. This is plumbed with polyethylene lined hose. The hole on the right side is for the high flow bypass valve. That provides for high gallonage applications, such as nitrogen fertilizer. As the fluid bypasses the inductor, it is returned below the inductor. This high flow bypass is done with a spring-loaded pressure relief valve, not shown.
This article was originally published at The Western Producer.