From growth stage to pest pressure, sprayers run when crops need them. This can pose a problem because ideal application timing does not necessarily coincide with dry field conditions.
Some level of compaction is almost invariably the result, and while steps can be taken to minimize negative impacts, there are few affordable solutions to sprayer-induced compaction.
Why it matters: The decision to spray is driven by more than compaction and soil health concerns, which makes soil damage more of a risk from sprayers.
Read Also
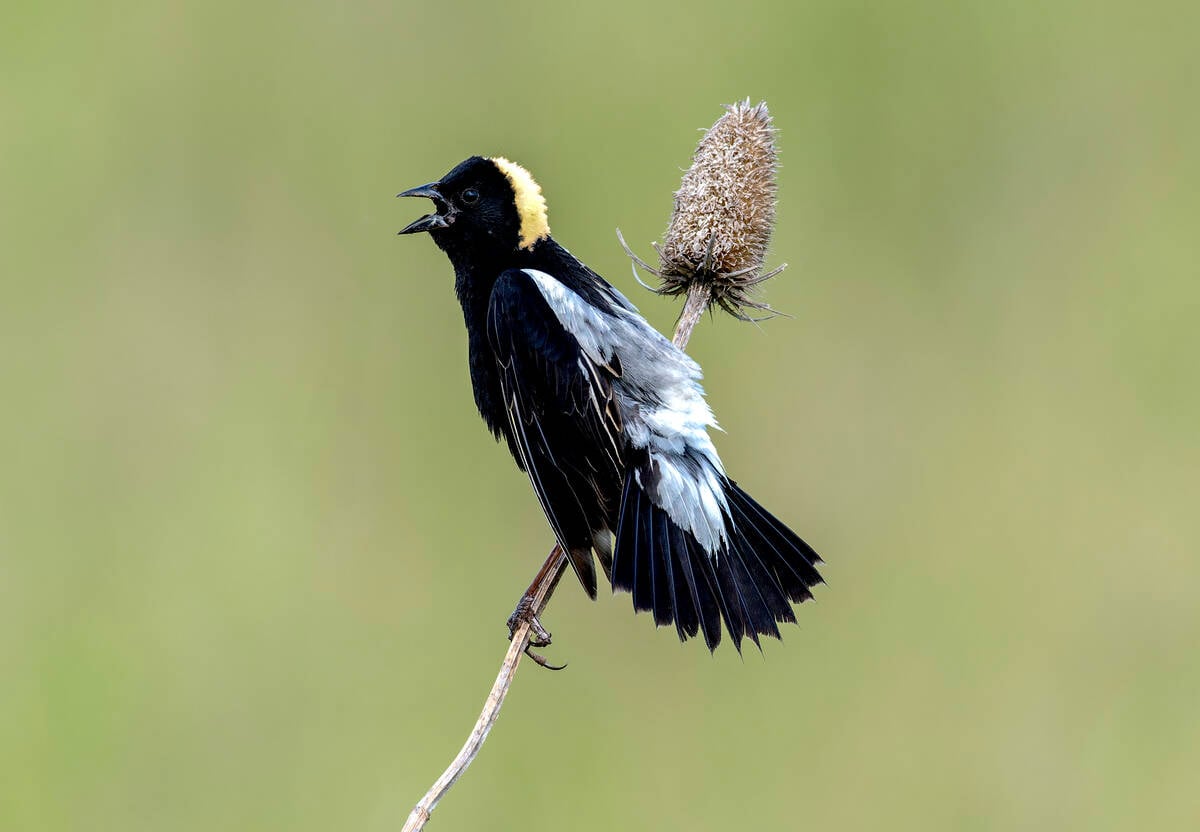
Canada and Ontario invest $14.6M to boost farmland resiliency and sustainability
Canada and Ontario increased investment of $14.6 million to help farmers improve soil, water, and biodiversity through the Resilient Agricultural Landscape Program.
Alex Barrie, farmer and soil management engineer with the Ontario Ministry of Agriculture, Food and Rural Affairs, says the high wheel loads and subsequent tire pressures of most sprayers make soil compaction a definite risk, particularly if operations are carried out under wet conditions.
Typical wheel loads for most high-clearance sprayers sit around 10,000 to 14,000 pounds per wheel, and can vary dramatically when the boom is folded or unfolded. On average, this translates to more soil stress than a loaded combine.
“Pull-type sprayers have wheel loads around 6,000 to 7,000 pounds and are usually on much smaller tires, but can be equally as bad,” says Barrie. The exception is the total weight of the machine will be lighter, so deep subsoil compaction is likely less of a concern.
“Considering all of this, and then taking into account the number of trips through the field, the cumulative damage done by the sprayer can add up quickly.”
Mitigating strategies
The overall problem, says Barrie, is the lack of practical sprayer design solutions free of their own compaction issues.
Smaller or lighter sprayers can reduce weight, for example, but require more passes over the field. Pull-type sprayers might have less downward pressure but they require a tractor. Such a solution, or the requirement to purchase more machinery, might not be practical.
Wider tires or tracks are another possibility, though that also means more trampled crops. Even if vehicles such as helicopters or hovercrafts were employed, applications could result in crop damage and loss such as wind-induced seed loss in canola.
The fact that most application timing is dictated by crop requirements and growth stage means growers just have to live with some surface compaction, says Barrie. Limiting traffic and trying to limit the weight on sprayer axles are the main mitigation strategies.
“If you just got two inches of rain, maybe don’t spray. But that said, if you do wait and your entire crop will be eaten by aphids, you need to make the trade-off,” he says.
“Short of going to a totally different sprayer configuration, but then you’re not saving any trips through the field … I can’t see a way to make sprayers lighter or without driving on more crop. There’s really no good way to do it other than the way it’s currently being done.”
Check tire pressure, remove ballast
Barrie’s perspective is shared by others in the field. At the 2019 Elgin Compaction Day, sprayer axle weight was cited as a significant and often overlooked compaction source by Greg Stewart, agronomy lead with Maizex.
Stewart said keeping booms folded whenever possible on self-propelled sprayers reduces the weight on the axle closest to the boom. He also cautioned against weighting down the equipment with extra ballast.
Regardless of the equipment, Stewart said farmers can prevent compaction by weighing their equipment, knowing the axle load, and checking tire spec-sheets to determine if tire pressure can be reduced.