An automated, 1,100-horsepower carrier unit with interchangeable implements has been developed by Nexat GmbH for broad-acre crop production.
Joseph Jandrisch is an owner of Kalverkamp Innovation, a parent company of Nexat GmbH, and he’s also one of four managing directors who guide product development for the machine.
He said the Nexat is a gantry-style, modular machine that will replace traditional fleets of farm machines.
Read Also
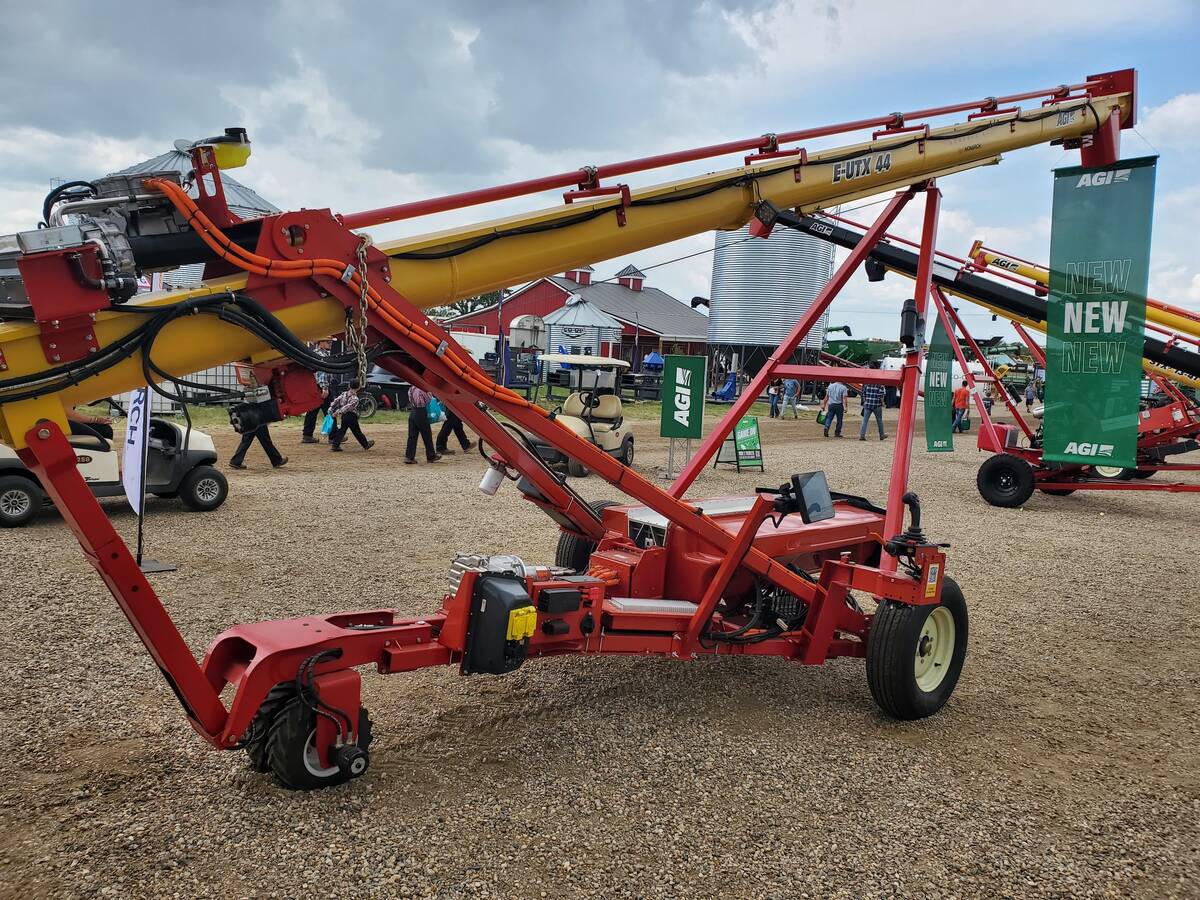
AGI unveils Smart Auger prototype
AGI showed its prototype E-UTX Smart Auger at this summer’s Ag in Motion 2025 farm show near Langham, Sask.
“We feel that a farmer will be able to get into the entire package for $2 million. We’re working with some of the bigger banks to provide financing options. Comparatively, you would need four to five million for similar performance equipment through the conventional system,” Jandrisch said.
A sprayer-nutrient applicator with a 212-foot boom, a combine, planter and tillage implement have already been built for the Nexat system. It takes about 10 minutes to switch the implements.
Nexat has been used in crop production for three years on test farms and it recently won gold at the 2022 Agritechnica Innovation Awards.
The wide-span carrier unit is powered by two independent, 550 hp Liebherr diesel engines that power a generator for the electric drives. The unit is 45-feet wide between the tracks and 10 feet wide when the tracks turn 90 degrees for transport mode.
The wide-span carrier unit is expected to be used in different industries including firefighting, but agriculture will be the focus of Nexat GmbH for the initial production years.
There are four electric drives, one on each of the four tracks, and they all have an output of 160 kwh.
“A lot of people don’t really draw a parallel between electric output and diesel engine output. But we start with the 1,100 hp, and we translate 95 per cent of that to the drives. The balance of the output is conveyed to a (power take-off) shaft and additional generators,” Jandrisch said.
The power take-offs from the engines power some functions of the implements.
He said where possible, components for the Nexat were sourced from established manufacturers, but some systems have been designed in-house, including the communications system.
The sensors system on the carrier unit and implements, as well as the environment monitors and user interface, have been developed by the Nexat engineering team.
Nexat has a cab where the operator can either run or monitor machine operations. However, Jandrisch said the primary purpose of the cab will be to transport the machine between fields or jobs.
Autonomous operation was a design focus, including the use of a digital twin representation of the farming environment. A digital twin is a virtual representation that serves as the real-time digital counterpart of a physical object or process.
“Our system uses lidar and radar to plot the field and plot the headlands and then we take that back to what we call our Terrakamp Digital Twin division, and we use machine learning and artificial intelligence to plot the best pathway through the field. The tracks that we lay out will be the only area that we compact, and everything between those wheel tracks is never subject to compaction again,” Jandrisch said.
“You can actually sit down at your kitchen table and watch a rehearsal of the machine going through the field in real-time speed or multiple times speed. You can tweak the path small amounts so that by the time the Nexat gets into the field to do the planting, it knows exactly where it’s going to go.”
He said the team developing machine learning capabilities has a goal to understand how the system affects carbon sequestration on a metre-by-metre basis.
Through the use of controlled traffic farming, where only five per cent of the field sees tracks, significant saving on inputs can be achieved because the tramlines are not planted or fertilized.
Nexat had been testing in Ukraine and Germany but has been forced to move some of the testing to North America because of Russia’s invasion of Ukraine.
When it comes to implement development, Jandrisch said they work with established equipment manufacturers when possible.
However, the company was unable to find a company to partner with for the combine attachment, so it was developed in-house.
At 1,1000 hp, the Nexat combine is by far the most powerful combine being produced, with Deere’s X9 in a distant second place with 690 hp.
“We’ve designed our own combine with a much larger throughput (compared to competitor combines). We can do approximately 70 per cent more acres per hour if you’re harvesting wheat or canola. We can harvest almost 80 per cent more bushels an hour of corn,” Jandrisch said.
The combine attachment can hold about 1,000 bushels in the grain tank, which can be unloaded in less than a minute.
He said the large grain tank and fast unload speed allows grain carts to be filled at the end of the rows, which helps reduce compaction on fields. Grain separation is done the width of the machine with two 20-foot rotors.
“Because we’re not using the conventional push or pull chassis-type design, we could turn those rotors parallel (with the cutting bar),” Jandrisch said, “whereas the distance between the axles in a conventional style combine is limited, maybe to eight feet. We don’t have limitations. We have over 40 feet between the tracks. And so that’s what allowed us to have such a huge increase in capacity.”
The Nexat combine attachment has been designed for direct combining, with the 45-foot header feeding to one feeder house.
“Rapeseed is much bigger and bushier and tougher than North American canola, and so we were successful with a bigger tougher crop. This will be the first year that we harvest North American canola. We’re scientists and engineers, and until we’ve proven it to ourselves, we’re not going to say we perfected it,” Jandrisch said.
The planter was developed with Vaderstad, and Jandrisch said there will be many options for growers to choose from, including seed singulation, multiple opener and packing styles.
“With our tanks system we can provide one, two, three tanks … some for seed and some for nutrient application. We can side-band, we can design anything that the farmer needs.”
He said an advantage the Nexat planter has compared to traditional systems that pull commodity carts, is that all the weight is held over the openers so it’s easy to have equal down pressure.
It also reduces compaction where the crop will grow because all the weight is kept on tramlines.
A sprayer-nutrient applicator with a 212-foot boom has already been used on the 2,500 acre and 1,500-acre test farmers in the Ukraine, however Jandrisch said smaller booms will also be offered.
He said the 45-foot-wide chassis of the Nexat prevents boom swaying, which helps the system achieve a uniform application.
“Our tank will be up to 5,800 gallons,” Jandrisch said. “With that and with it operating autonomously in the evening, we can provide chemicals at a much greater rate than traditional sprayers.”
Farmers will have the opportunity to customize their sprayer with the latest technologies.
The fourth implement that has already been developed is a tillage implement.
However, there will be many options, from deep ripping with the ability to apply nutrients, to implements for residue management.
“We will have some standard applications available pre-configured, but this is an open-source system. If a farmer decides that they want to use a specific tool that’s not in our list of applications, they’re welcome to adapt to it,” Jandrisch said.
“We really believe in the open architecture concept. It’s the farmer that owns it. They can modify it as they see fit. We will support their efforts and extend that to the data.
“We think that the farmer and landowner really should own all the data from every aspect of farming.”
A hydrogen-based power plant is also being developed to replace the diesel engines for some customers, and there will be wide-span carrier units available with wheels instead of tracks.
Nexat GmbH is entering the fourth year of testing this summer and plans to begin production in 2023.
“Soon we’ll be collecting orders for 2024 delivery. It’s going to take us at least a year and a half to complete our distribution and field support network. But our website will soon open to orders,” Jandrisch said.