In the third instalment on Massey Ferguson’s manufacturing history in Ontario (read Part 1 and Part 2 here), we examine what it was like to be a combine field test engineer for the company in the 1970s. Here is a compilation of recollections from various engineers who worked at MF’s Brantford plant during that time.
Whenever a brand develops a new machine concept or model, the prototype is put through a rigorous field testing process, accumulating as many working hours as possible in the shortest amount of time. That is how engineers ensure the design is ready for production and delivery to dealers for sale.
During the 1970s, Massey Ferguson engineers were busy turning out a wide variety of concepts for testing, and some field engineers had a reputation for being unconventional in their methods. An infamous story among the ranks of engineers at MF during that era was about an engineer from the company’s early days who particularly embodied that attitude.
Read Also
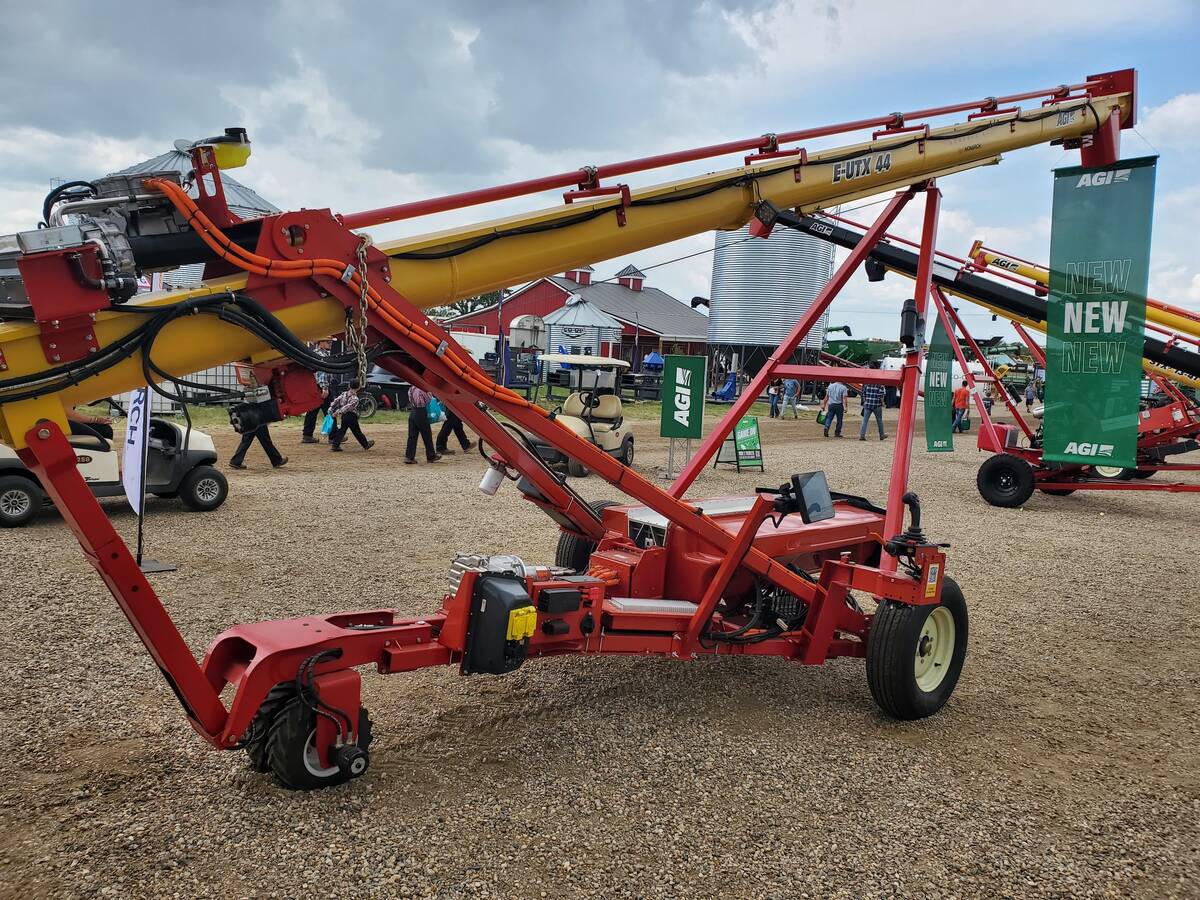
AGI unveils Smart Auger prototype
AGI showed its prototype E-UTX Smart Auger at this summer’s Ag in Motion 2025 farm show near Langham, Sask.
This particular engineer, with his crew, was working out of an airport hangar while field testing a combine. The engineer decided the machine needed to be bigger, so the team put it in the hangar and cut it in half to widen it.
Myth or reality, it was widely circulated among the MF engineers at the time.
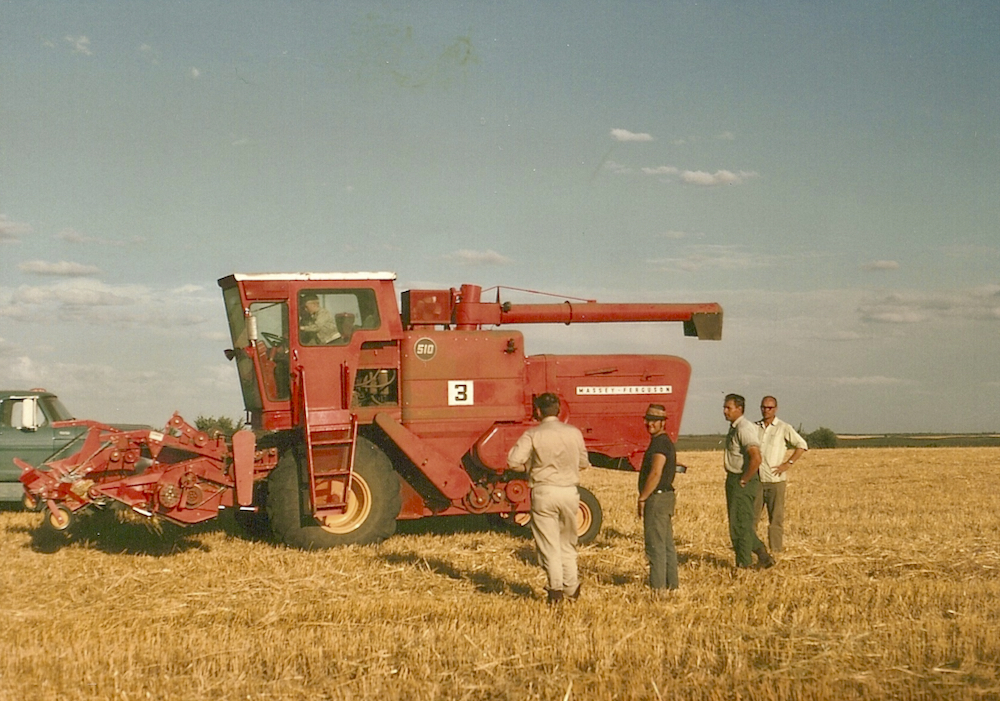
That same pioneering attitude was reflected in some of the projects on the drawing boards at MF in the 1970s. A prototype 700-series machine was created that used a tandem-axle drive system, the same as a road grader; and another looked at the efficiencies to be gained by using two smaller, six-cylinder engines rather than one large motor. One would power the threshing mechanism while the other drove the machine. From a marketing perspective, it had little chance of success, but it did see field testing.
Other manufacturers were also developing concept machines and new components. They all used farmers and custom operators to test their machines, often in the same part of the country.
Sometimes MF’s engineers would find themselves staying in the same motels with other companies’ engineers while they each worked on their own secret projects. Finding out what the competition was up to was the sideline activity of engineers from all companies. Word would eventually get around about who was doing what in the area.
On one occasion in Arkansas, a group of MF engineers heard about John Deere’s engineers working in the same area. One Sunday morning, they hired a man who had the local accent and a pickup truck. Massey engineers always drove white pickups and Deere engineers knew it.
This fellow had an old beat-up truck with a dog in the back. With three of MF’s engineers riding along, the local man drove into the yard where Deere’s test machines were sitting and struck up a conversation.
The MF engineers didn’t open their mouths for fear their accents would give them away. The Deere engineers were working on a cutter bar with broken pieces all over the place. As they nonchalantly wandered around, the engineers watched the Deere people struggle through a repair. Then they left, apparently leaving the Deere engineers unaware of the spying.
But turnabout is fair play. Despite the fact that MF, too, tried to keep its test machines well hidden from onlookers, it wasn’t always successful.
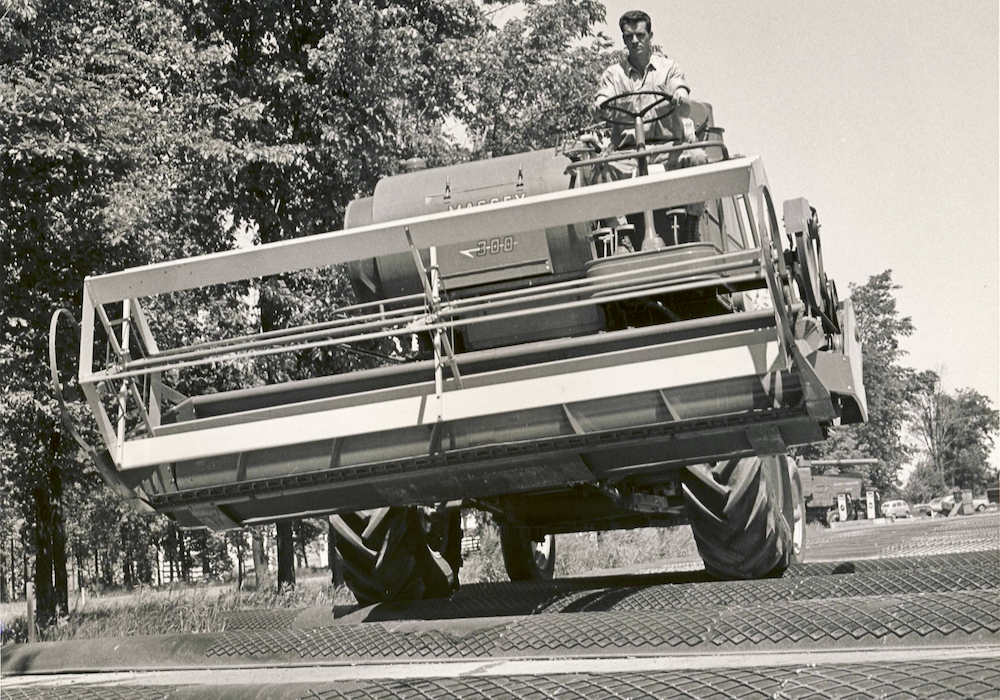
In the days before digital photography, the Polaroid camera was the easiest way to get quick pictures. When MF’s engineers came out in the mornings and found the white strips of paper from Polaroid pictures, they knew the competition had been looking around the night before.
The crew of the MF “Harvest Brigade” that followed the custom harvesters on the annual route from Texas to Canada, and supported them with parts and service, didn’t focus on using them to test machines. Other engineers did.
Getting a custom cutter to put a lot of hours on prototypes was critical in perfecting the design of new combines for all manufacturers. That was the only way engineers could put several years’ worth of work on a machine in just a few months.
On one important occasion that arrangement worked to the advantage of both MF and the cutter.
MF had given some 760 models to a custom cutter, but he wasn’t interested in using them. Although the cutter only had to supply the fuel and operators to use them, the combines were sitting idle.
MF staff decided to collect their machines and give them to another custom operator in the area. Sam Wiggins, who had been struggling with some older 510 combines, took advantage of the MF offer to use the 760s.
Wiggins parked his own machines and ran the 760s non-stop. The next year, when the 760 went into production, Wiggins bought a large fleet of them. He went on to become the biggest custom cutter in that area, thanks in large part to the use of those original 760s. That started a long-term relationship between Wiggins and the MF engineering staff, who went back to him year after year for testing.
In the next instalment we’ll focus on MF’s development of a rotary model and the beginning of the end for the Brantford assembly plant and MF’s entire combine manufacturing days.