Glacier FarmMedia – Track systems built for agriculture applications have come a long way during the past decade, but as with anything, they require maintenance.
There used to be a larger variety of styles of tracked machines equipment manufacturers sold to farmers and they each had different maintenance demands.
Now though, most track systems are similar.
Read Also

HJV unveils split grader with Tomra Optical Sorter at Potato Field Day
At Ontario’s Potato Field Day, farmers got a first look at HJV’s Split Grader prototype. Paired with a Tomra 3A optical sorter, the system removes green potatoes and debris at 100 tons per hour, improving storage quality and reducing labour needs.
“Most of them are pretty much a light viscosity oil bath with mechanical seals,” said Marc McDonald of Soucy Track in Drummondville, Que.
McDonald has worked with tracked systems for more than 20 years and he said careful pre-season inspections and repairs will keep things moving when time is critical during planting.
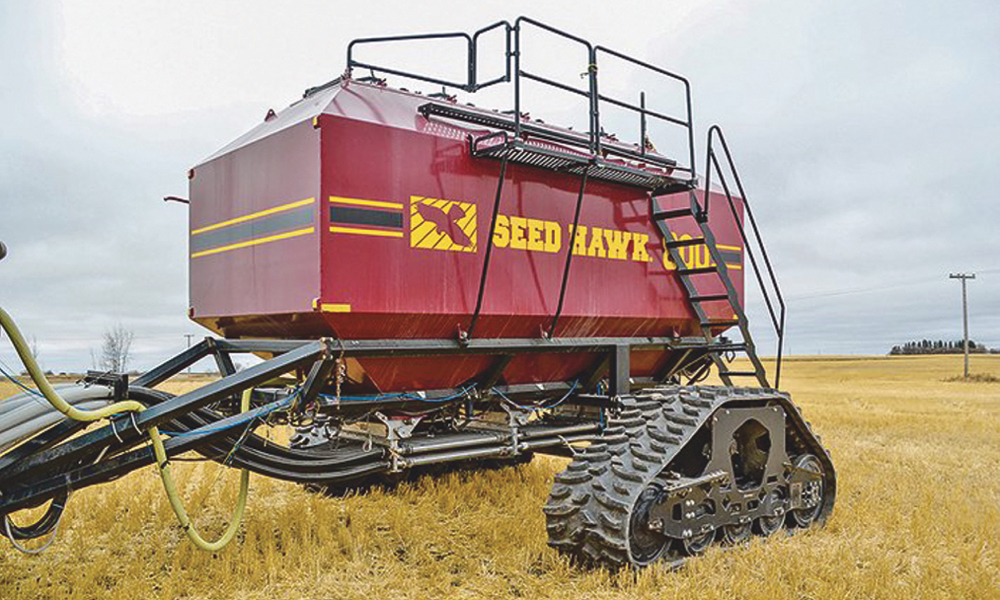
When it comes to checking the oil in the planetary hubs McDonald said it’s best to move the machine around a bit before checking the oil levels and quality.
“After you run it around and you’ve mixed up the oil inside of it, check the oil and make sure that you don’t have water contamination or dirt contamination or rust,” McDonald said.
“Obviously, it’s easier to take that wheel off and inspect it and clean it and service it if necessary than trying to wait until it becomes a problem when you’re not ready to work on it.”
Each track manufacturer has its own maintenance schedule for when oil should be changed, but McDonald said it’s a good idea to change the oil yearly for track systems that get put under a heavy load like high horsepower tractors.
Before moving tracked equipment at the start of the year, McDonald encouraged operators to first perform a thorough visual inspection.
“You’re looking for bearing seal issues, looking for oil leakage, or maybe looseness in the bearings when making a preliminary inspection. Secondarily, making sure that there is not a lot of material ingestion including mud or debris or whatever may be the case, and then clean it up before you get started.”
He said track systems are basically conveyer belts and there are not a lot of moving parts that are placed under a high load.
“It really just comes down to the idler wheels, the bushings in the front wheels, and as well as the bearings seals of the bogie rollers.”
It’s also a good idea to watch the tracks make a few revolutions to make sure they are tracking straight and there are no alignment issues.
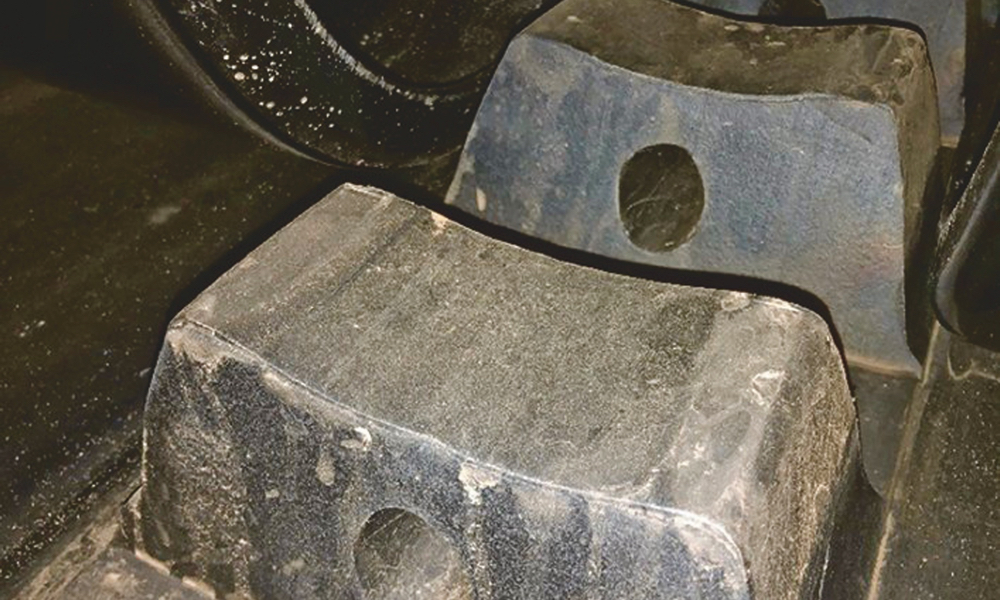
McDonald said if you don’t see anything rubbing when you’re watching it move forward or backward, you’re probably in good shape, but you should also check for heat generation on the track lugs after they’ve been used.
“Probably the easiest way of checking heat generation is your hand itself. The temperature of the track itself shouldn’t get over 165 F. That is pretty much the magic number. It’s about all your hand can stand to touch.
“Take it out for two or three miles and you touch your hands on both sides of the lugs and if you can keep your hands on the lugs you probably don’t have any problem.”
If one side of the lugs is warmer than the other an alignment problem is likely.
Mike Friesen of Elmer’s Manufacturing in Altona, Man., said track systems do not require a lot of maintenance, but checking track alignment is key to ensuring the longevity of the rubber track.
“This is done by checking that the inner guide lugs are running evenly between the pairs of idler and bogie wheel sets, or a simple drive test on flat ground. Inspection of the inner guide lugs for any excessively uneven wear from one side to the other is also another indication of a potential alignment issue,” Friesen said.
“Alignment can be adjusted by checking track frame alignment to the chassis of the cart and adjusting the front idler wheel angles.”
He said there will always be some wear on the guide lugs because of the friction between the lugs and wheels.
Low or high track tension can contribute to track misalignment as well as creating extra stress on track components.
Tracks with a hydraulic tensioned track system will have a visible pressure gauge to allow for easy pressure confirmation.
“Most hydraulic systems use an accumulator, which also should be maintained. An easy indicator is a quick spike in track pressure while simply driving the track. An accumulator low on nitrogen can lead to over tensioning as it has little cushion for debris, dirt or ground contours,” Friesen said.
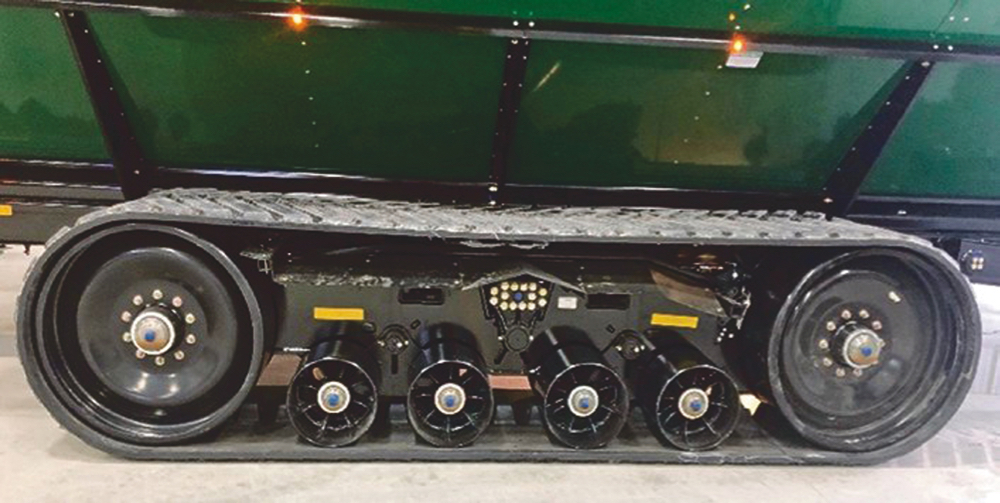
Preseason maintenance for track systems should include checking welds on all structural components for cracking, checking the torque on all bolts and nuts, and greasing all lubrication points, and checking for loose hubs and worn bearings on all hubs, Friesen said.
“Observe if any noticeable damage to the bearings or locking components have moved. Lastly, a quick check on the inboard side of the hub will reveal any potential oil seal leaks despite the oil level being maintained.”
Friesen said operators should pay special attention to any cuts or rips in the rubber that expose the inner steel cords, when they are looking for loose or missing internal guide lugs and external treads.
“Once the cording has been exposed, but not visibly damaged, it’s important to have the track repaired as quickly as possible before the damage impacts the structural integrity of the track itself.
“If the track’s structure has not been compromised, check with your dealer or manufacturer for repair options. These repairs can entail replacement of the inner guide lugs, exterior lugs or cuts, tears or rips in the tread itself.”
This article was originally published at The Western Producer.