The FarmDroid FD20’s silent and methodical movement through seven acres of onions generated many discussions during a recent robotics tour.
“This robot does not have any kind of camera vision. The weeding it’s doing relies solely on a base station and its own RTK GPS,” said Chuck Baresich. “When the plants are smaller, it can weed in between.”
Baresich, owner of Haggerty AgRobotics and co-founder of AgRobotics Working Group, hosted the July 4 tour at the Ontario Crops Research Centre Bradford/Holland Marsh site and at Smith Farms, which grows 350 acres of onions.
Read Also
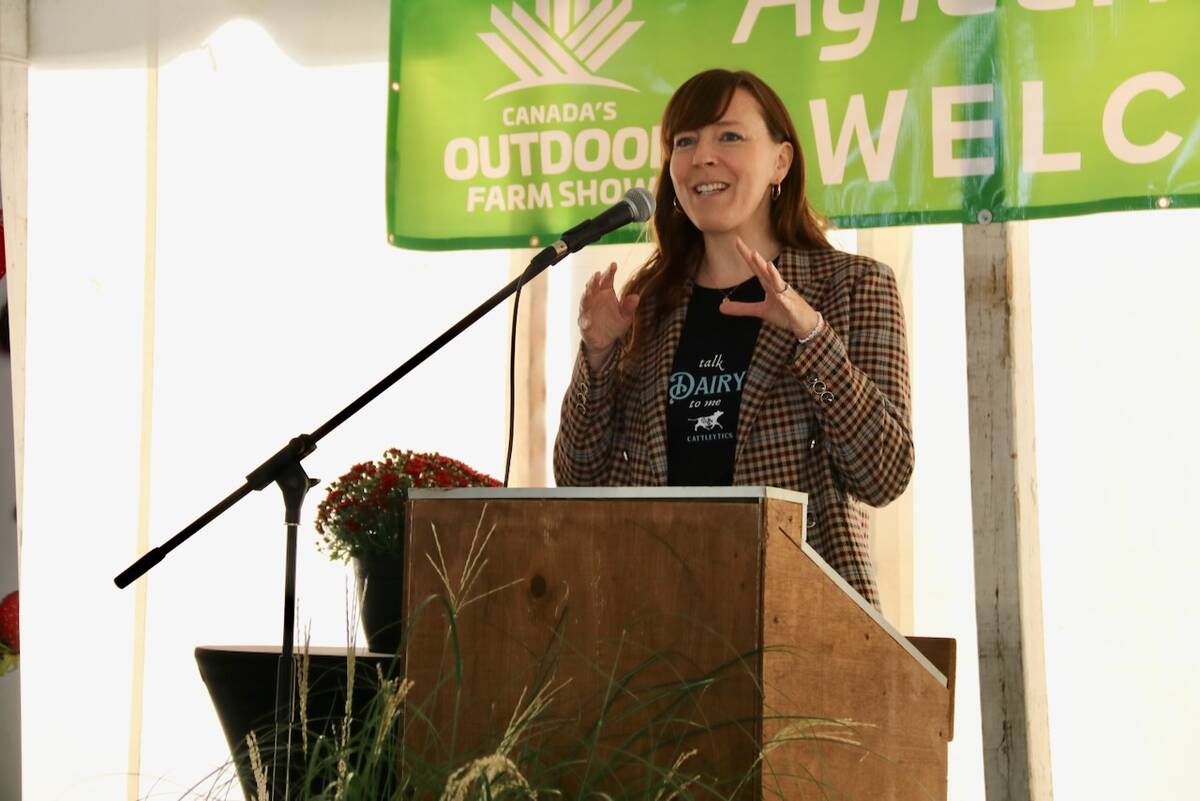
See the latest in agriculture tech at Canada’s Outdoor Farm Show
Innovation programs have become a critical part of Canada’s Outdoor Farm Show, showecasing up and coming technology for farmers.
Why it matters: Farmers are always seeking ways to save labour and pesticide costs and several robots that do that are are in the trial phase in Ontario.
At 900 kilograms, the autonomous solar-powered FarmDroid FD20 provides lightweight, ultra-precision planting and weeding for up to 6.5 hectares daily, potentially increasing yields and lowering labour and environmental impact.
Last year, FarmDroid planted the trial field in three days, running 23 hours with its solar-powered battery, said Kevin Vander Kooi, a University of Guelph researcher at the centre. Half the solar power energy runs the robot and the other charges the battery.
Producer feedback and observation from season one led to development of a 3D-printed three-seed planter, which increased functionality in season two.
“The idea was to put groups of three (seeds) because we know onion transplants grow well at this spacing,” Vander Kooi said. “The nine (per foot) that we put in a single row last year did OK, but we ended up with smaller onions for a variety of reasons.”
Baresich said safety concerns are minimal during autonomous operations with speeds of 750 to 950 metres an hour, unlike some farm robots that require partial or constant human oversight.
The GPS guidance system is accurate to .1 centimetres for planting depth, spacing and placement.
However, without crop or weed identification visuals, FarmDroid is only effective within the fields it’s planted. It can’t move farm to farm or field to field, said Baresich.
“It’s designed to be a systems approach, so it goes in the field and does its thing. They are working on software to allow it to map out what is planted in the field, but they have not released that.”
When touched, the robot’s string “safety bumper” triggers a kill switch, as do rain sensors when programmed rainfall rate is exceeded.
“The good thing is, if something goes wrong, it doesn’t keep going and makes a mess or skips half the field,” said Vander Kooi, adding it then requires in-person resets for safety.
A monitoring camera provides remote operator assessment of other issues via a desktop app. For example, the unit might drag a lost seeding unit or pick up debris, like sticks, explained Baresich. Short of getting stuck or hung up, that wouldn’t trigger an alert.
“Periodic checking is important on these machines because this crop is very valuable. You can’t just let it run unattended all the time. Most of the (human) interventions that happen are either ‘I’m out of seed’ or a mechanical fault.”
FarmDroid accommodates two to 12 rows, of 8.85-inch row widths and up. Globally, 50 crops use the robot on broccoli, spinach, onions, turnips, sugar and red beets, rapeseed and flowers.
Baresich said there’s always a tradeoff between functionality and machine costs. The return on investment extends beyond worker-to-robot evaluations to include higher yields and opportunities to grow different, higher-value crops.
With a complete set of tools and options, including a precision spot application system that can reduce chemical use by 97 per cent, Baresich estimated the ROI of the $130,000 robot at five to six years, depending on the row units.
“Our end game is, if this system can be perfected, Guelph learned something, the farmer learned something, and we end up with the product we can sell,” says Baresich. “We all win in the end.”