Glacier FarmMedia – Successful technology often arises from figuring out how to simplify something that’s exceedingly complex.
That’s what Casey Forsyth and his team at FeedFlo think they’ve managed to do with their feed pipe monitoring system.
Their model is working in scores of barns in the U.S. hog belt, where it accurately measures whether feed is flowing to pens in the barn and notifies producers if something goes wrong at the bin, in the pipes or with the pigs themselves.
Read Also
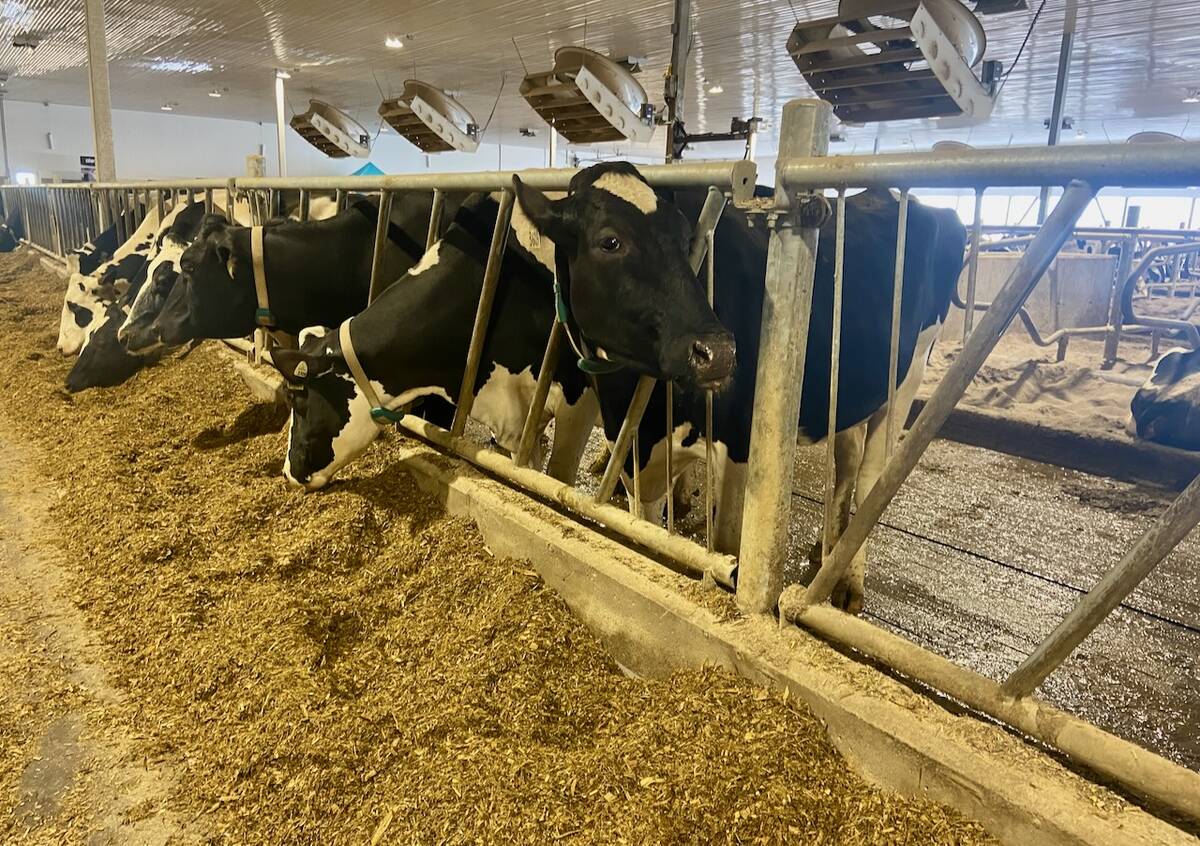
Financial metrics can lead to different dairy decisions
Focusing on dairy farm productivity without proper financial analysis and monitoring could mean less profit, says a Chris Church, a veterinarian with an MBA.
Why it matters: The FeedFlo measures a missing piece in feed management – whether or not feed is flowing through pipes.
It does this with little maintenance and provides useful data to barn managers.
“There’s too much stuff to do in a barn already,” said Forsyth, a Winnipeg innovator and a co-founder of FeedFlo, who began working on feed pipe measuring plans five years ago when he was an infotech consultant in the finance and health care fields.
“We wanted to keep the whole thing as simple as possible.”
That was an enormous task, requiring Forsyth and colleagues to combine software design, technology such as lasers and metal detectors, mechanical engineering, 3D printing and machine learning.
But before they could do any of that, they had to understand why hog feeders needed a better way to know if their system was broken or if their pigs weren’t eating.
Fortunately for Forsyth, his co-founder and employer at the time had grown up on a hog farm and understood the critical importance of feed management to commercial operations.
His consulting firm had been working with a hog production company to improve a feed pipe monitoring system. That company decided to give up on it after spending a lot of money trying, and gifted the knowledge gained to that point.
The need for a monitoring system is obvious to some in the hog industry, because feeding systems often break down in the dusty, real-world conditions of the feeding barn, costing farmers days of lost production and undermining the health of the growing pigs.
Creating an accurate and affordable system that wouldn’t require too much management dissuaded most from attempting to build such a thing.
Some systems measure whether feed is coming out of a bin, and it’s possible to measure how much pigs eat at the other end, but there is nothing to monitor whether feed is flowing through the pipes.
Bin monitors are often slow to reveal system breakdowns and many feeding barns don’t measure feed consumption, so animals can go hours or days without feed before anybody notices.
Forsyth worked on various approaches in between his paid consulting projects. After talking to lots of people in the U.S. industry, he concluded it should be possible to create a monitor and sell it to hog system operators.
Forsyth and his employer spun the idea into the company that became FeedFlo and tried to develop a simple system. That’s when things got difficult.
“We were just a bunch of software developers using 3D printing and just rapidly iterating to make up for our lack of mechanical design (knowledge,)” said Forsyth.
Ensconced in temporary digs in the basement of Winnipeg’s main concert hall, they were able to create a “dust room” to mimic barn conditions and devised their first clunky system. It was a box containing a laser and metal detector to measure feed flow and auger spin.
The first model, which they referred to as “the onion,” was a big box that would be strapped to a pipe that had a tiny hole drilled for the laser. Another box full of electronics hung above it. The onion was never intended to work at commercial scale, but was used to test the concept.
Soon the gritty reality of dusty barns became obvious. The lasers were quickly blocked by dust, even with a glass plate in front. The inventors tried using a fan to blow over the glass to keep it clear, but it failed in commercial conditions.
Forsyth remembers the sickening feeling of discovering, on the last day of the World Pork Expo in Des Moines, Iowa, in 2022, that all of the approximately 60 monitors they had recently installed in eastern Iowa were failing.
At that point, they could have quit or tried to tweak the device and sell what they had. Instead, they doubled-down on innovation and dedicated themselves to solving the problem.
“We learned to not be discouraged by failure,” said Forsyth, a lifelong optimist. “This was just another feedback cycle for us.”
He hired a mechanical engineer, and problems began to disappear. Instead of a fan, the engineer designed the glass to exactly fit the curved shape of the pipe so it wouldn’t catch dust.
“It’s so much more elegant,” said Forsyth, who rues the development time wasted before getting the engineer on-board.
With a better mechanical setup, the analytical work could be based on accurate data, instead of a library of information from all sorts of feeding operations.
In January, the firm brought out its new model, installed it in barns (mostly in the U.S.,) and finally found success. After years of being quiet about their system, they began to talk about it publicly and proudly.
Will the North American hog feeding industry, always cost conscious, labour-deprived and operating on tight margins, embrace this technology?
Sow barn operators are willing to invest in high tech systems like electronic sow feeders because of the high value of piglets, but the feeding game is all about lowest cost per pound of pork produced. That could make it a hard sell.
But Forsyth thinks the production gains possible from avoiding feed system failures will create steady demand from producers who see net gains in production leading to higher profitability.
“We think there’s a huge opportunity to retrofit these finishing barns,” said Forsyth.
– This article was originally published at The Western Producer.