A dairy farmer is separating the coarser fibres in his corn silage to create feed for the milking and dry cow herd.
He’s now selling the Fodd machine to other dairy farmers to reduce feed costs and improve the ration fed to milking cows.
Why it matters: Feed is one of the largest costs on a dairy farm and a way to make the feed more efficient can help reduce that cost.
Greg Friendsbruh says feeding coarser fibres to his dry cows and the more consistent-sized silage to his milking cows means he’s getting more milk, and with 65 per cent home-grow forage in the ration, reducing his feed costs.
Read Also
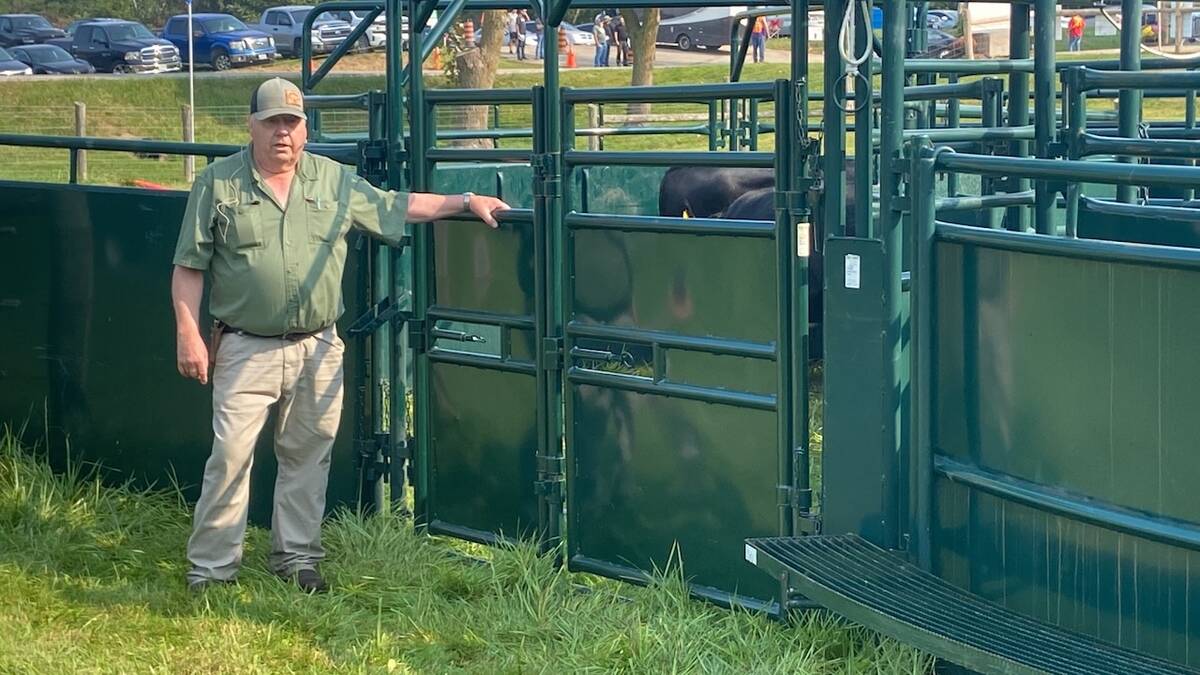
Livestock demos feature the latest in handling and management
Livestock demonstrations feature the latest in handling and management at Canada’s Outdoor Farm Show 2025.
Friendsbrugh has about 1,300 cows and young stock on his farm in Wisconsin and like many dairy farmers fed straw as part of his ration, especially to dry cows. In 2019 the straw he was feeding was of poor quality and quantity and suddenly he needed more forage for the cows.
“Our straw we were feeding the cows was mouldy and expensive,” said Friendsbruh at the World Dairy Expo in Madison, Wi. where he promoted the Fodd system.
He and his consultants decided to try to pull the stover constituents out of his corn silage to feed dry cows.
“Basically we’re trying to pull the corn and the energy out of the stover,” he says.
Silage corn is the least-cost ingredient in his area of Wisconsin, so it has made sense to grow more corn, separate the rougher fibres and create a higher energy diet for the milking cows.
“The economics in the states are pretty sound. We’re saving $150 per head per year in feed costs, and we’re earning another $150 per cow per year in the milk bump that we get.”
Friendsbruh says that the higher energy ration hasn’t resulted in more cows with metabolic problems.
The use of the Fodd silage separator involves a change in feeding process on farms.
A processing centre needs to be created that houses the separator and the separator will have to be fed with silage regularly.
“This machine on our 1,300-cow dairy with young stock runs about five and a half hours and it will sort all the feed that we need for that day,” says Friendsbruh. Without young stock, the current separator model can sort enough feed for 3,000 milking cows. The hopper has to be filled every 45 minutes to keep it going.
Friendsbruh says on their dairy they fill it and let it sort, then go and feed and as they come back for more loads of feed, the separator has created more differentiated feed as they need it.
The dairy has changed how it manages its Total Mixed Ration feed ingredients. Friendsbruh says they bring all the ingredients to the feed centre, including piling the day’s corn silage next to the separator.
“So at that point in the day, when we’re mixing feed, all the ingredients are close and the machine can purr along and do its job.”
The plan is to size the machine down so it will fit smaller herds in the industry.
He points out that most dairies are processing straw for various rations and instead using that processing time to separate silage means there’s no need for processing straw.
Friendsbruh says the dairy’s feed efficiency is high and they’re going to do some research on why that is. He says that more of the separated silage shows up on the middle screen of a shaker box (used to analyze feed particle size), with less on the top and bottom screens, meaning the ration is more uniform.
The separated silage portion might seem like rocket fuel for cows, and Friendsbruh says he was worried about that when they started to feed it. However, he says that starch level isn’t much higher than usual and they haven’t had an increase in acidosis or laminitis.
Friendsbruh says his goal is to have the system pay for itself in 10 months.
“The hope is to keep the price point in that spot so farmers can enjoy the benefits and put some money in their pockets.”