Exeter Produce’s focus is in its name, but it’s pivoting to poultry to grow the business for the next generation.
Mike and Jim Veri run the company started by their father, with several of their children now involved.
Why it matters: Succession plans take many forms, but for many farmers that means diversifying into a new sector, like the Veri family has done.
“We’ve wanted to get into (poultry) for probably 10 years, since my son first got out of Ridgetown,” said Mike Veri during an open house hosted at the family’s poultry site east of Exeter. Broilers went into the first barn on the property last September.
Read Also
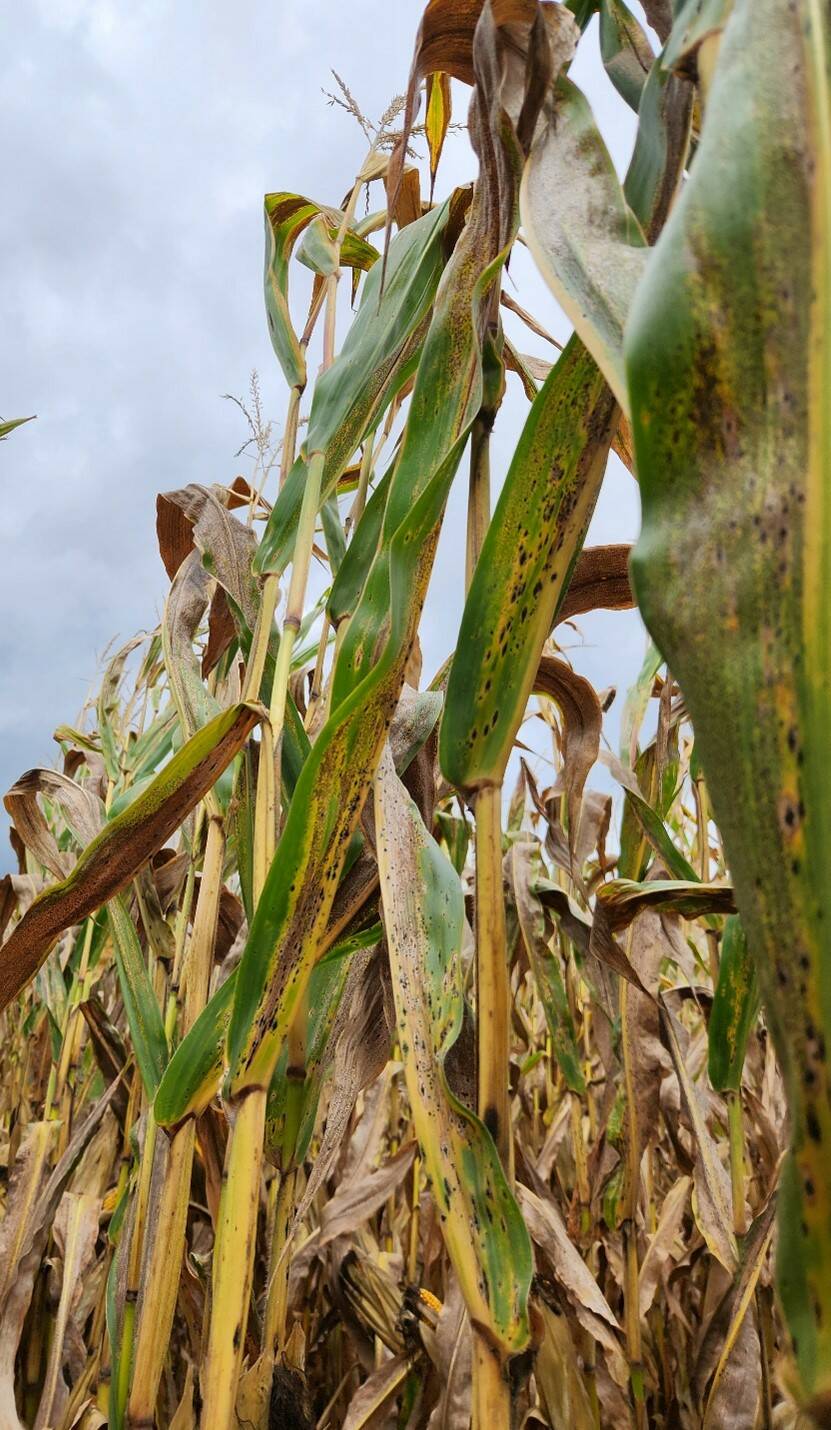
Tar Spot firmly planted in Ontario corn
Scouting is critical for mitigating impact on tar spot, as well as timely fungicide application.
The second barn is empty, but will soon be filled with chickens. During the open house it was filled with neighbours, farmers and tradespeople who worked on the project.
Mike said the family debated between buying more land or buying quota and building poultry barns.
“We decided farm prices are the same as poultry right now, so we went this route, longer term, and set it up more for the kids and the grandkids.”
Veri’s father started out waxing turnips, which at one point was big business in the south end of Huron County. He decided to rent 50 acres, buy a tractor, and grow their own.
The company acquired 2,800 acres in the 1960s which set the Veri family on its way to being a significant vegetable presence, mostly in the former Hay Swamp lands west of Exeter which are great for growing vegetables.
They now farm 5,000 acres and grow cabbage, bell peppers, grean beans, rutabagas and grains crops in rotation.
“This is just another part of the whole mix, the poultry,” says Mike Veri.
The company’s VeriFine brand ships produce across North America and into the Caribbean.
The barn is a typical of most broiler barns built recently, says Herman Gerrits, of Vanden Heuvel Structures Ltd., the general contractor for the building.
There’s more centralized control around how the feeders are raised and lowered, but other than that it’s standard.
The ventilation system is integrated as all the components are from European supplier Skov, says Mark Damsma, who works in poultry sales for County Line, the equipment supplier.
The Skov system, which in this barn involves a cooling wall, tunnel ventilation, side wall vents and ridge vents manages the system automatically and tha algorithm responds to changes in the environment on a curve versus in the step-wise fashion of less-sophisticated systems. This means more gradual changes in the environment for the birds.
When it comes to broiler barn design, “most of the most of the everything revolves around the type of ventilation going into them,” says Gerrits.
When the barn temperature gets to 29.8 C, the cold walls start to open and act like a radiator, with cold water going through the cold walls.
“It’s almost like an air conditioning unit for the barn,” says Veri.
The barns are 330 feet by 65 feet and at that length only need one door for modular loading of chickens, which has become the standard for poultry in Ontario. There’s capacity for 22,000 birds in each barn.
There is room on the farm for two more barns. The first two were paired and share services like a generator, and water and electricity services, says Shawn Kerslake, of Kerslake Brothers Electric, who worked on the barn.
The barn, like most broiler barns, operates with a minimum of labour. Feed and water lines are operated with one main auto winch, as opposed to a winch of each of the line, which is more common.