One of the most difficult decisions dairy farmers face when building a new free-stall barn is determining the best ventilation system.
Naturally ventilated freestalls have been popular for decades, with lower-profile fan-ventilated free-stall barns growing in popularity in Ontario over the past couple years. A concept from Wisconsin combines some of the advantages of both.
Why it matters: Dairy facilities with proper ventilation delivered efficiently can boost milk production and farmer profit.
Read Also
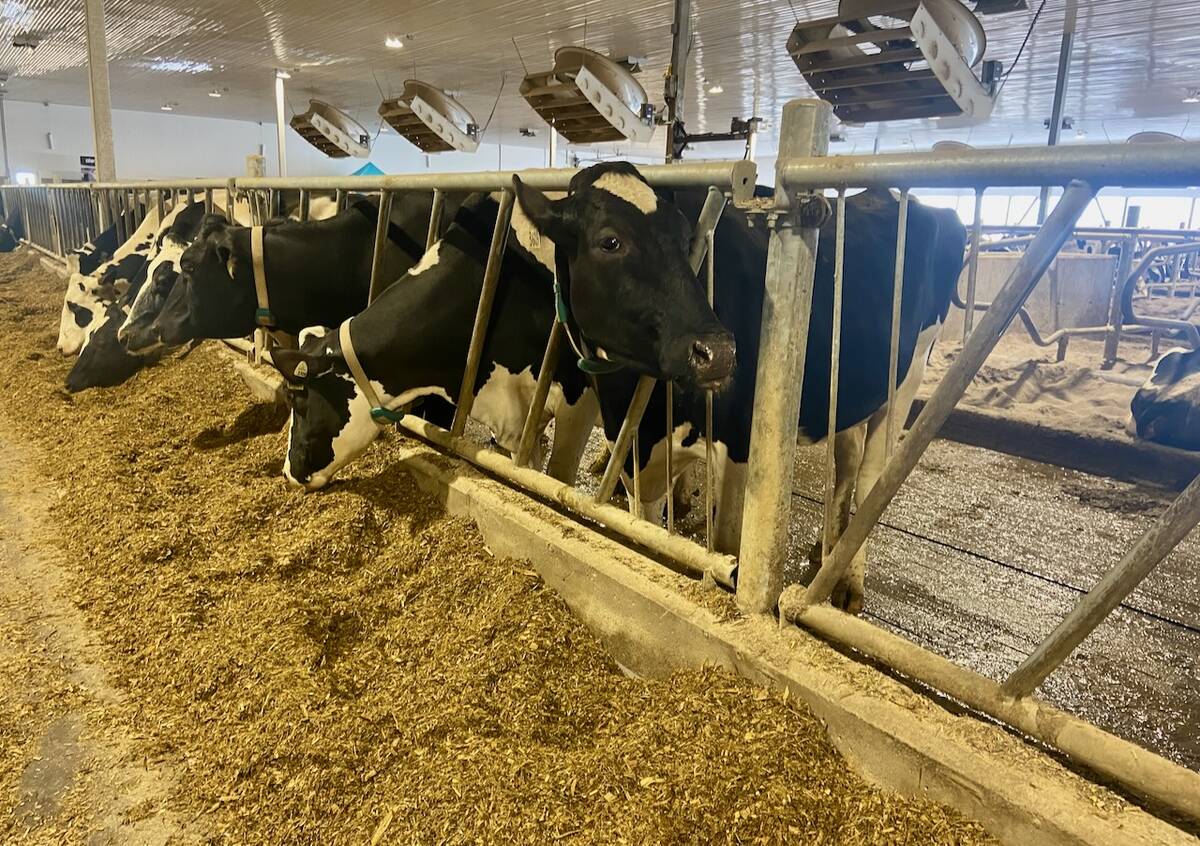
Financial metrics can lead to different dairy decisions
Focusing on dairy farm productivity without proper financial analysis and monitoring could mean less profit, says a Chris Church, a veterinarian with an MBA.
Historically, ventilation was done with a wind tunnel concept. However, as dairy barns got longer, there became limitations on how much air could be pulled the length of the barn.
In barns where the air couldn’t be pulled to a constant speed the length of the barn, some of the cows breathed lower-quality air. To tackle this issue, a cross-ventilated system, with fans placed at intervals along one side of the barn, was developed. But even with this system a cow closer to the fresh-air side had advantages over one at the exhaust side. In addition, there are significant costs associated with both of these mechanical solutions because they require fans to run year round, although they run at much lower levels in winter, versus performing a cooling function in the summer.
To tackle these challenges, a year and a half ago Wisconsin veterinarian Dr. Gordie Jones developed an “all-seasons hybrid” barn that he recently presented to a Canadian group of dairy farmers.
The project began when Jones teamed up with a Wisconsin dairy farmer who was building a new barn. Initially, the farmer wanted to build a cross-ventilated barn, but Jones convinced him to try this new approach.
The goals of the new barn were:
- No heat stress above 20 C;
- No cow bunching (a problem with naturally ventilated barns);
- No frozen manure.
In a nutshell, the barn is naturally ventilated below 20 C and mechanically ventilated above 20 C with 40 to 60 air exchanges per hour (comparable to other mechanical methods).
“No power and no fans are needed below 20 C. Once we are below 20 C, the side walls are opened and it’s a naturally ventilated barn,” Jones said.
“Once we reach -10 C to -15 C, we start to close the exhaust of the barn and we make four continuous air exchanges per hour. The cows heat up that air and we have no frozen manure.”
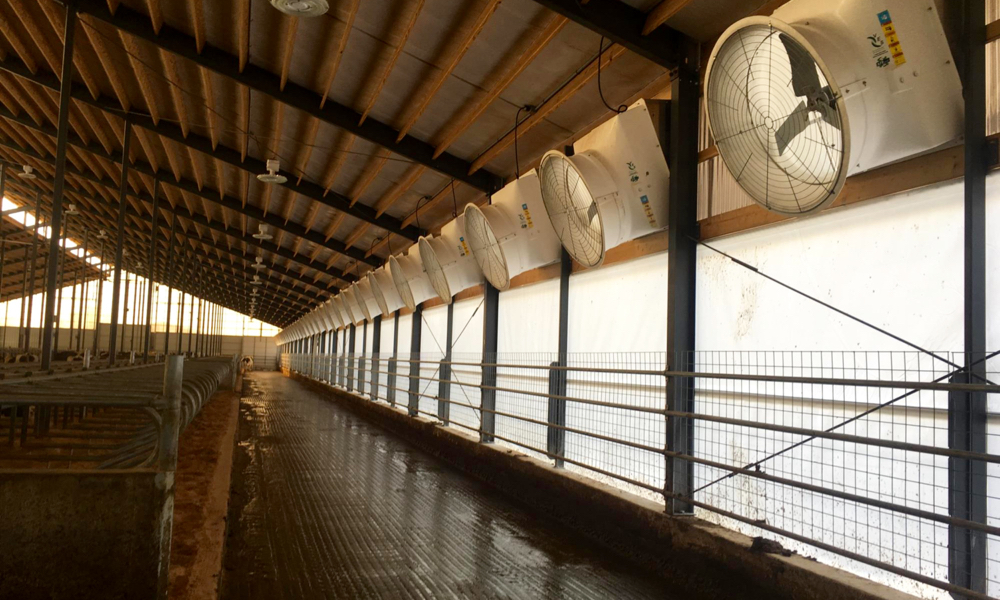
The temperature inside the barn can be as much as 30 C higher than the outdoor temperature (without steam becoming an issue). So, even in a severe cold spell, when temperatures reach -40 C, the temperature will be -10 C in the barn and manure will not freeze (of course, water will have to be insulated and heated with electricity to keep it from freezing).
The design they landed on had five-metre side walls, an insulated ceiling, a one-metre overshot roof vent, thermostat-controlled curtains, and one-metre-diameter fans placed every three metres (angled at 22 degrees) along both sides of a four-row barn.
“What that now means, is we have one fan for every four beds,” Jones said.
The fans blow across the stalls so there’s no need for a fan in the feed lane. Air speed of 34 km/h at the fan, results in air speed at the bed space of 12 km/h and at the feed lane between 16-22 km/h.
In addition, every 18 metres, there is a big, low-speed, high-volume ceiling fan that’s used in the winter to blow warm air down and keep manure from freezing.
While some of the elements of this barn add to construction costs over more conventional designs, when the operating costs were analyzed by the University of Wisconsin, the all-seasons hybrid, showed impressive efficiency. At US$18.60 per cow/year to run the fans, it was comparable to the US$18 a naturally ventilated barn (with cooling fans over the feed lanes) delivered for the same-size herd.
A cross-ventilated barn is more than twice that at US$42 per cow and the wind tunnel ventilated barn costs almost three times as much (US$56/cow).
So far, the new barn has met all the goals. With recorded external temperatures reaching as high as 34 C and as low as -33 C, all cows are getting fresh air, there was no heat stress, no cow bunching and manure didn’t freeze.
However, the most important data is the effect this new barn had on herd productivity. Keeping in mind that the new facility addressed a 30 per cent overcrowding issue, the dairy’s productivity increased 26 per cent (from 38 kilograms to 48 kg per cow per day) after the upgrades.
“It turns out that if you cool cows off and if you give them fresh air, they eat more, and ultimately, they milk more,” said Jones.