An OMAFRA project is exploring how farmers can apply the kind of practices that made Toyota a world leader in car manufacturing to improve farm profitability.
The ministry’s Environmental Management Branch has been working with farmers and food manufacturers to see how conducting Lean principle audits of their operations can help efficiency and productivity.
Why it matters: Many manufacturers have benefited from the Japanese-inspired Lean principles, making their businesses more efficient and predictable and in some cases more profitable. But farming is different — or is it?
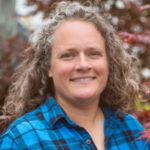
Jacqui Empson Laporte, an OMAFRA environmental specialist who covers Huron and Perth counties, says that the new provincial government is pushing Lean principles internally to reduce costs and find efficiencies.
While it may seem strange to have the Environmental Services Branch delivering this type of business management advice, Empson Laporte said there are several good reasons.
Lean principles are usually aimed at increasing efficiency and profit, which is good for a farm business. However, making Lean changes can also solve environmental issues, decrease resource use and therefore environmental impact.
John Van de Vegte, an engineer who now works with the ministry of Agriculture Food and Rural Affairs has a background in manufacturing outside of the agricultural sector. Empson Laporte credits his experience and willingness to question the way things have always been done in agriculture with helping to drive some the changes in process on farms. He’s been involved in the case studies created by OMAFRA.
Read Also
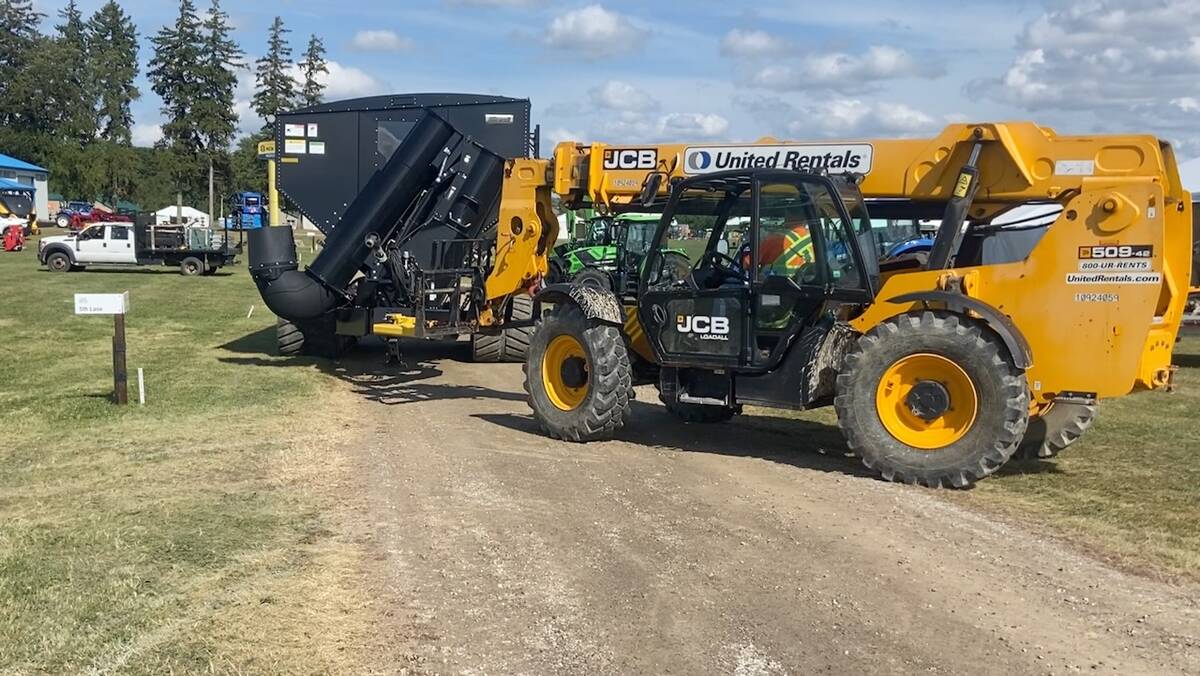
What to see and tips for 2025’s Canada’s Outdoor Farm Show
The Canada’s Outdoor Farm Show 2025 site was changing every day in the week before the show with equipment, people and tents arriving.
What are Lean principles?
According to the book The Lean Farm by Ben Hartman, it was principles developed by Taiichi Ohno, considered the father of the Toyota production system that spawned the worldwide Lean trend. Depending on the source, there are between five and seven principles.
In his 2015 book, Hartman included:
- Figure out precisely what it is that your customers value. This is beyond the product, but also can include presentation, timing and packaging, for example.
- Identify the value stream for each product, meaning the steps in the process that create value.
- Find how to make value flow without interruption. This means removing waste.
- Let the customer pull value from the producer. In other words, don’t over-produce.
- Pursue perfection, which means continuously work to improve.
- Respect workers and harness the wisdom from your workforce.
Hartman, a small vegetable farmer from Goshen, Indiana credits Lean processes for improving the farm’s profitability to the point where he and his wife can work full time on the farm.
There are several long-standing programs that promote the use of Lean principles, including Six Sigma, which was used for years by Maple Leaf Foods and Kaizen strategies promoting continuous improvement and efficiency.
One farmer on Twitter recently called these types of strategies “common sense.”
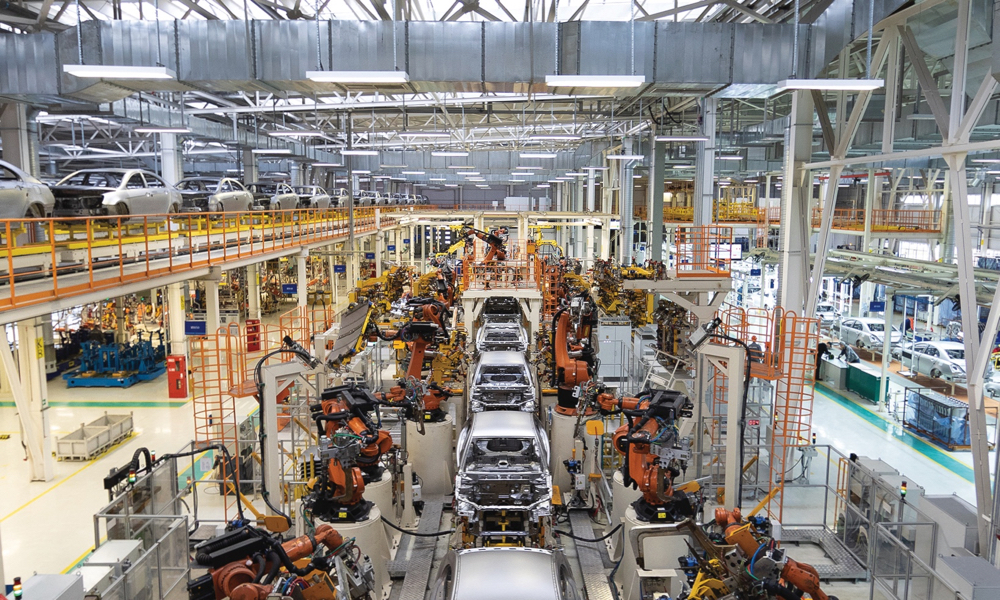
Harnessing these approaches, however, requires a careful study of existing processes on the farm.
While universities have experts in Lean manufacturing, there haven’t been many farm programs that have encouraged it. However, a British Columbia program used funds from the Canadian Agriculture Partnership to fund Lean training for food processors.
Test cases
Empson Laporte spoke at the recent Ag 4.0 conference put on by Grey County in Hanover. She talked about some of the test cases they have undertaken so far.
“We’re driving farmers and agri-food businesses to look at expenses and how to do things better,” she said.
For example, OMAFRA used Lean analysis to help a carrot farmer evaluate how washing processes on the farm affected water consumption and waste.
The previous process brought carrots in from the field and washed them all before they were sorted, culls removed and the keepers packaged. Washing all the carrots before sorting was the biggest source of the extra dirty water.
The farm installed a shaker at the field, so more dirt stayed in the field where it belongs. The carrots are now sorted before washing, resulting in a reduction in dirt volume and the amount of water needed. A 10 degree change in the position of a splitter plate also resulted in more even flow through the process and a reduction again in waste.
Finding solutions in this case meant stopping and evaluating what was happening in every step of the process, says Empson Laporte.
“Sometimes we have to do the counting and that’s a little painful,” she said.
OMAFRA officials are also working with a maple syrup operation that wants to increase the amount of syrup bottled from 10 per cent to 30 per cent. Making improvements to the bottling process would increase the operation’s value-added returns.
Simple process improvements
Empton Laporte said the changes don’t have to be big ones.
For example, a farmer watching a combine being fixed in his shop one day observed how the workers had to crawl out from under the combine several times during the job to get their next tool from across the shop. The farmer’s toolboxes are now on wheels and can be taken to where the job is happening.
In another example, a dairy farmer decided not to use the usual custom operator to move manure and do the job using a skid steer with a small bucket and a small manure spreader, because they had some time that day.
Empson Laporte questioned whether the farmer was making the best use of time using smaller equipment versus hiring a custom operator. Attaching a value to his time would likely have shown the custom operator provided better value.
As well, Empson Laporte said encouraging manure application efficiency makes better sense for the environment.
Frauxmagerie, which makes a vegan cheese-like product from cashews, credits working with Empson Laporte on Lean processes before expanding helped keep the rapidly growing operation on track. In two years they’ve moved to four locations and have gone from making 200 cheeses per month to 8,000. They’ve recently signed on a new buyer, which means they have to grow to 40,000 per month.
Looking for process waste
There are many places to find waste in a business or manufacturing process.
Jacqui Empson Laporte says there are nine forms of waste in a process. Examining them is part of the Lean-system process. They include:
- Energy
- Correction
- Over-production
- Movement
- Motion
- Waiting
- Inventory
- Processing
- Under-utilized people