Robotic weed “zaptistas” delivered field-applied plant cell exploding technology at the July 9 Bradford AgRobotics demo day.
Tech entrepreneur David Tao, CEO and co-founder of Ontario-based BH Frontier Solutions, presented a compact BHF ElectricWeeder, and Dutch ag-tech firm Pixelfarming demonstrated a modified laser model.
Why it matters: Energy-based robotic weed removal offers a solution to herbicide resistance and labour challenges for producers reliant on hand-pulling.
Read Also
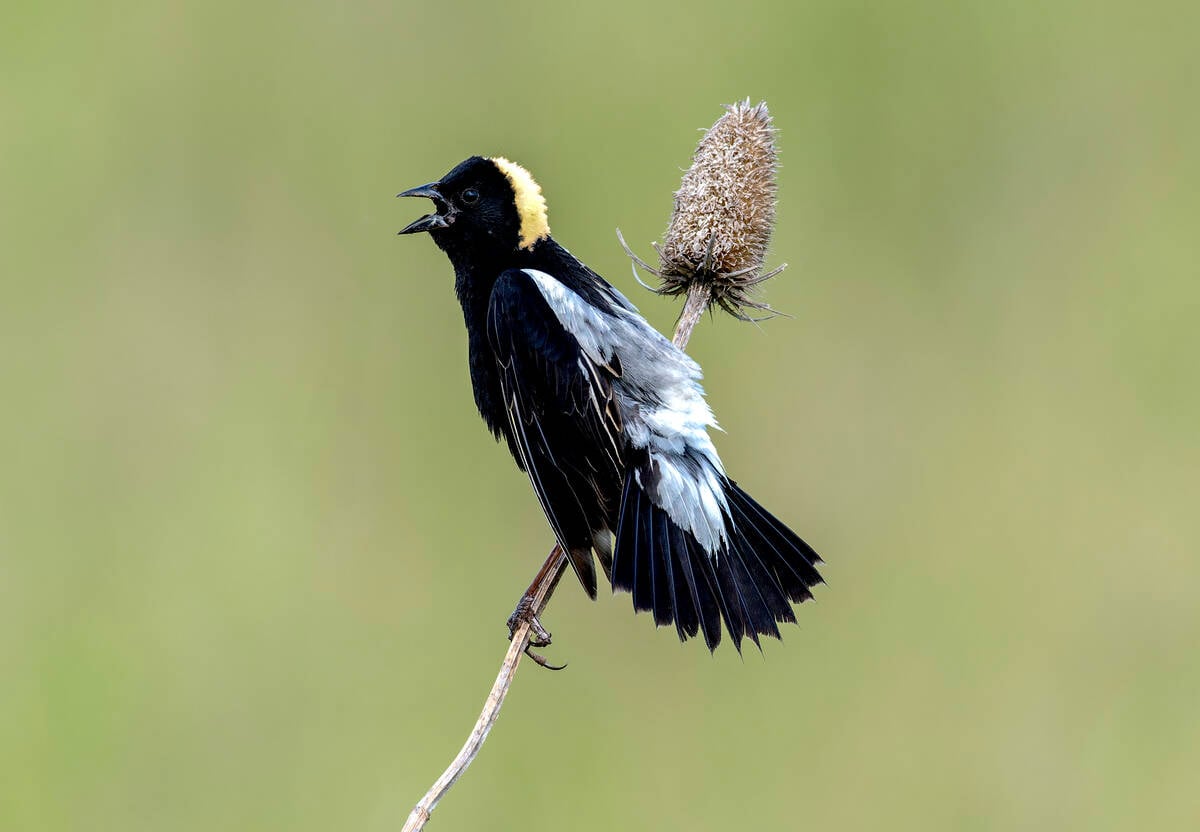
Canada and Ontario invest $14.6M to boost farmland resiliency and sustainability
Canada and Ontario increased investment of $14.6 million to help farmers improve soil, water, and biodiversity through the Resilient Agricultural Landscape Program.
Haggerty AgRobotics president Chuck Baresich explained that the Pixelfarming Laser One–i prototype, adapted for the Orio NAiO’s frame, arrived in March. NAiO is an autonomous field robot in its third year at the Ontario Crops Research Centre in Bradford
It features six laser units that use high voltage to energize a carbon dioxide tube, creating a focused beam that boils the liquid inside plant cells, effectively destroying the plant. “The lasers will shoot forward and back,” explained Baresich. “It will determine the optimum angle as you’re moving forward to hit the various weeds.”
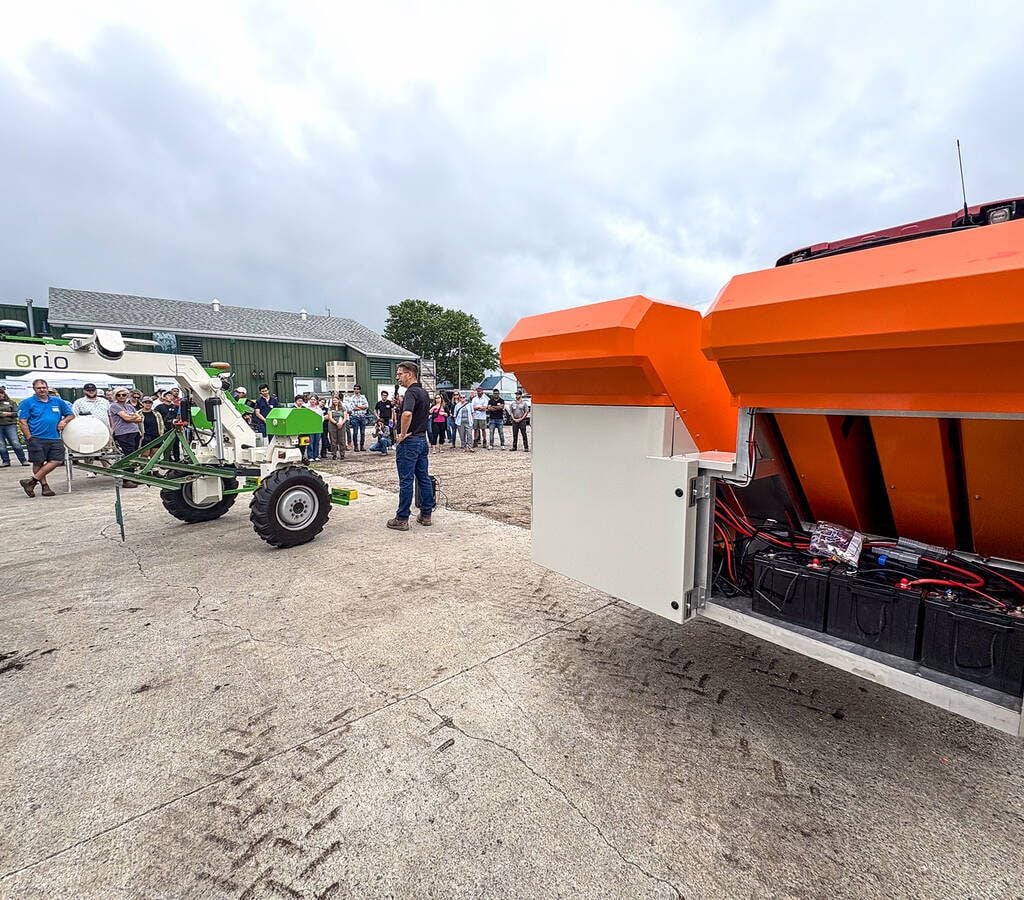
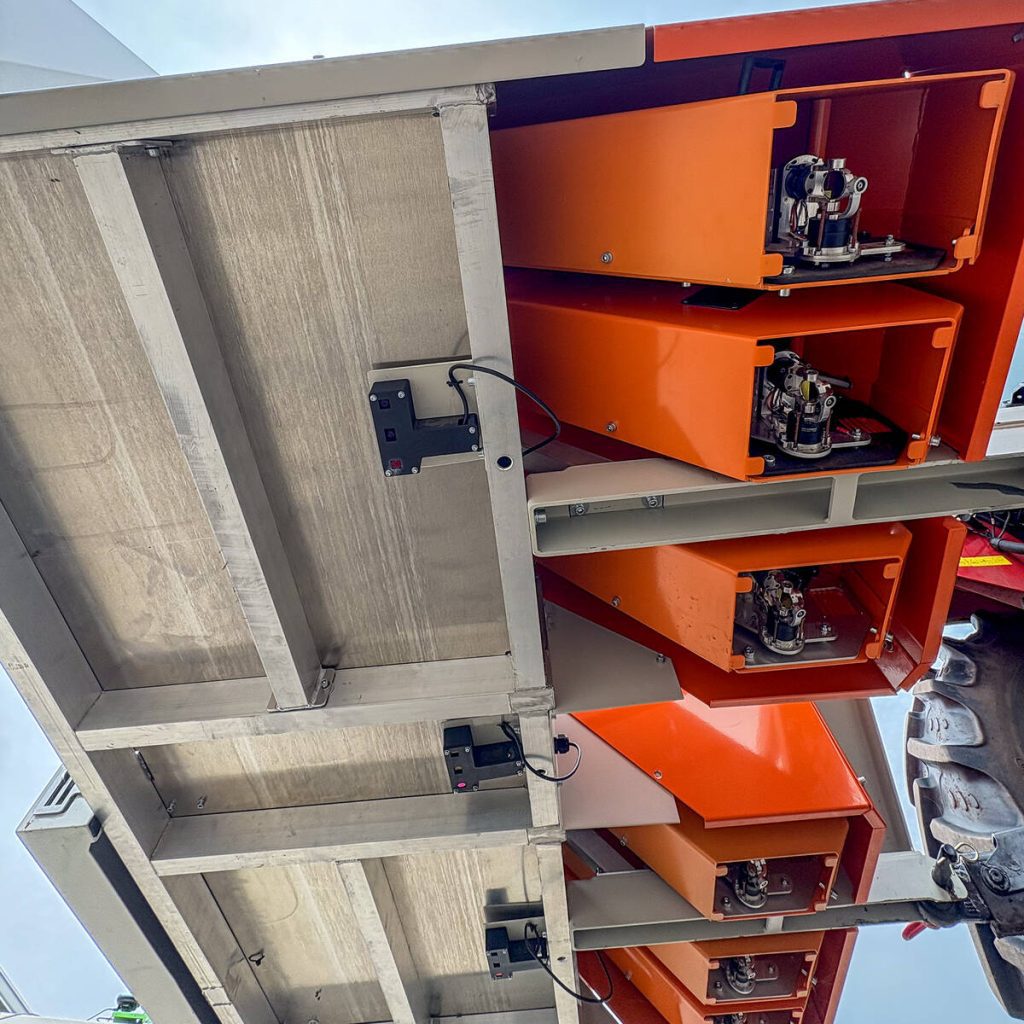
Rydan Chalmers, Haggerty AgRobotics Systems Engineering intern, used 35 images of multicoloured confetti to demonstrate how easy it is to programme the interface’s crop module to target specific plants or, in this case, confetti colours for eradication. Baresich clarified that plant images at various growth stages and under different lighting conditions are necessary to develop a comprehensive crop model, noting that the rapid pace of technological advancement and the availability of open-source tools are accelerating the process.
“You can load five (models) at a time,” Chalmers explained. “We have a few examples we’ve been testing in the field. And you want to make sure you have the right laser selected, (and) how much energy is going to each laser.”
For the demonstration, Chalmers set the lasers to 80 per cent, which, while producing a satisfying flame-out, was excessively high because most weeds and grasses are effectively terminated at between 25 and 40 per cent power.
Baresich warned that there is a low chance of starting a small fire if a field is dry or of damaging a neighbouring crop if the heat isn’t properly adjusted.
The LaserOne–i’s speed and effectiveness are optimized for dime-sized plants or early emergence, as larger plants slow the machine significantly.
“When you have a very, very tiny weed, it takes only milliseconds of heat to cook that,” Baresich explained. “That’s how you get the speed of the machine up.”
Field trials comparing 90,000 weeds to a million weeds per acre showed a significant slowing of the machine due to the number of shots per second/ac., a common issue when dealing with grass because it’s prolific, Baresich said. Depending on the heat level and dwell time required to eliminate a plant, the three lithium phosphate batteries provide a four-hour runtime, with the ability to add additional batteries.
BHF ElectricWeeder is an autonomous robot that selectively kills weeds with high-voltage electricity. It is guided by artificial intelligence using an integrated multi-camera computer algorithm that differentiates between weeds and crops.
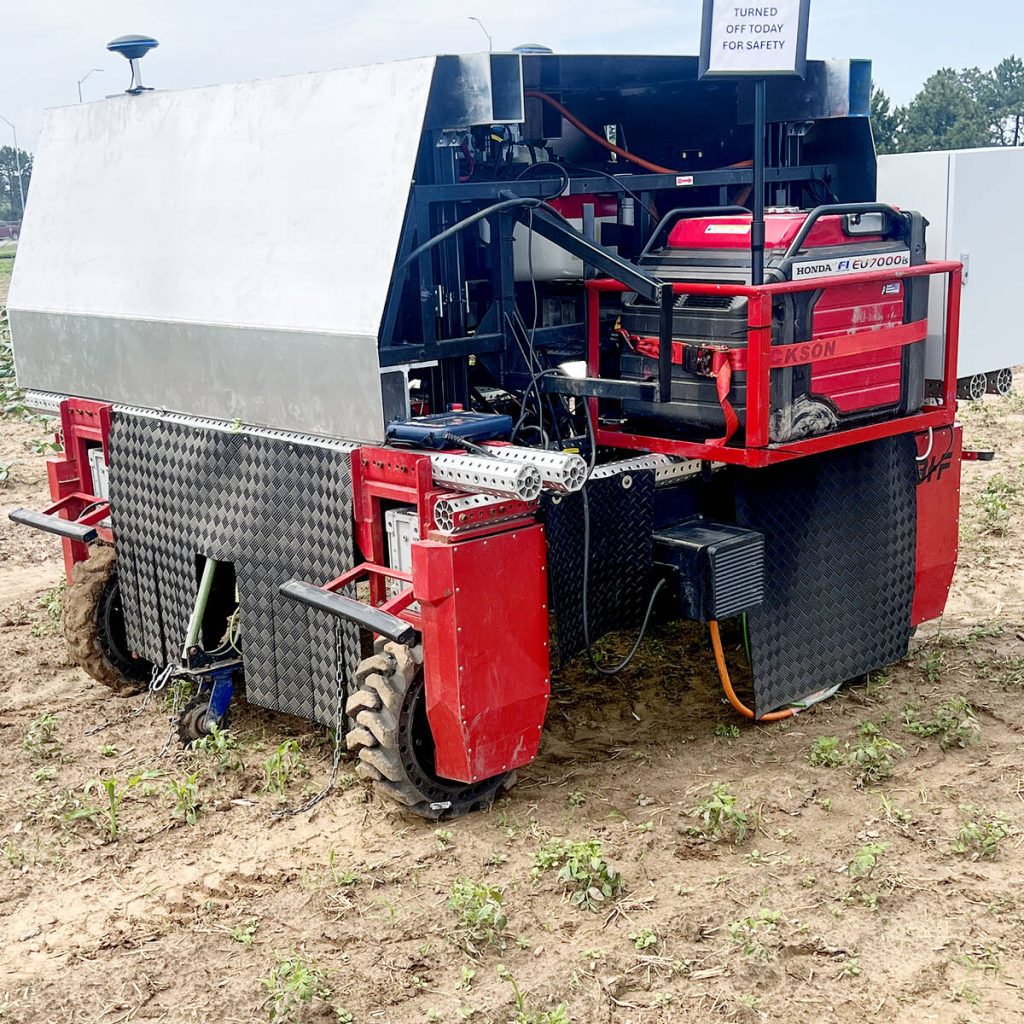
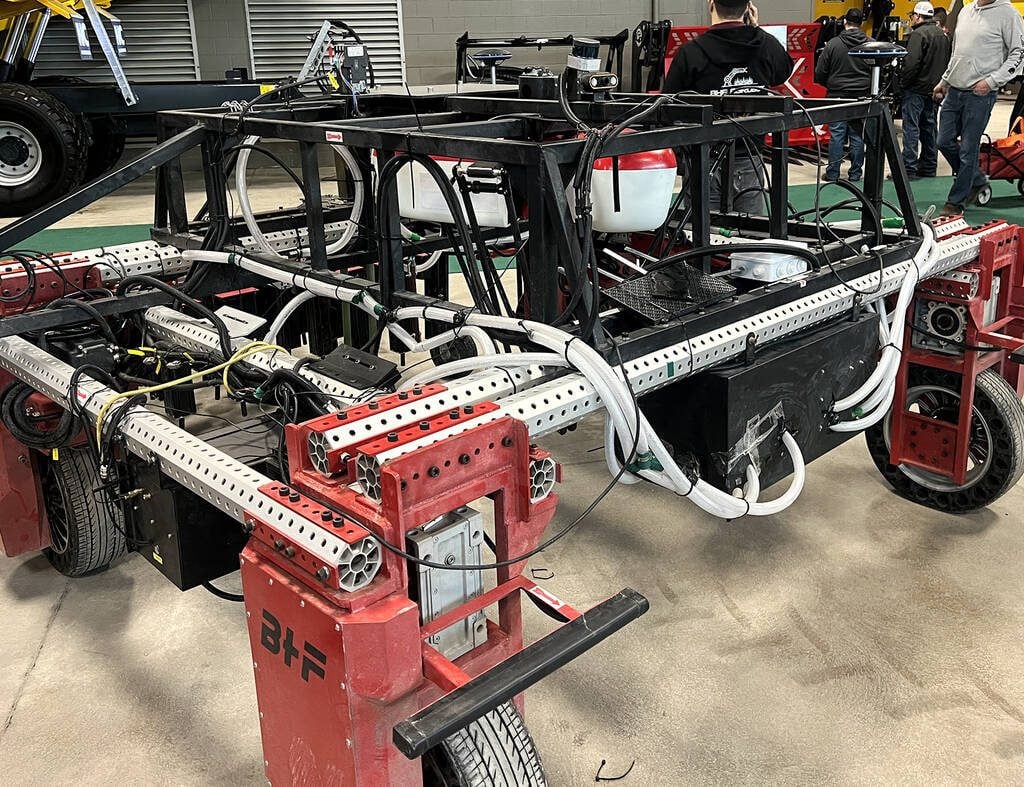
“The algorithms are trained to recognize the crop; anything different from that would be considered a weed,” Tao explained, adding that the crop model trains with 100 images, with shape and morphology changes requiring additional training.
The robot collects data automatically, improving the AI’s accuracy and increasing its speed without the need for farmer oversight outside of the initial RTK to plot out the rows.
“Once it detects the weeds, it will guide the robot arms underneath and basically target the weed and zap it,” explained Tao, adding it’s part of an onion crop trial at the research centre.
During the demo, the robotic arms moved swiftly and methodically through the crop, unleashing an electric current that often produced a visible puff of vapour as the weed’s cells burst.
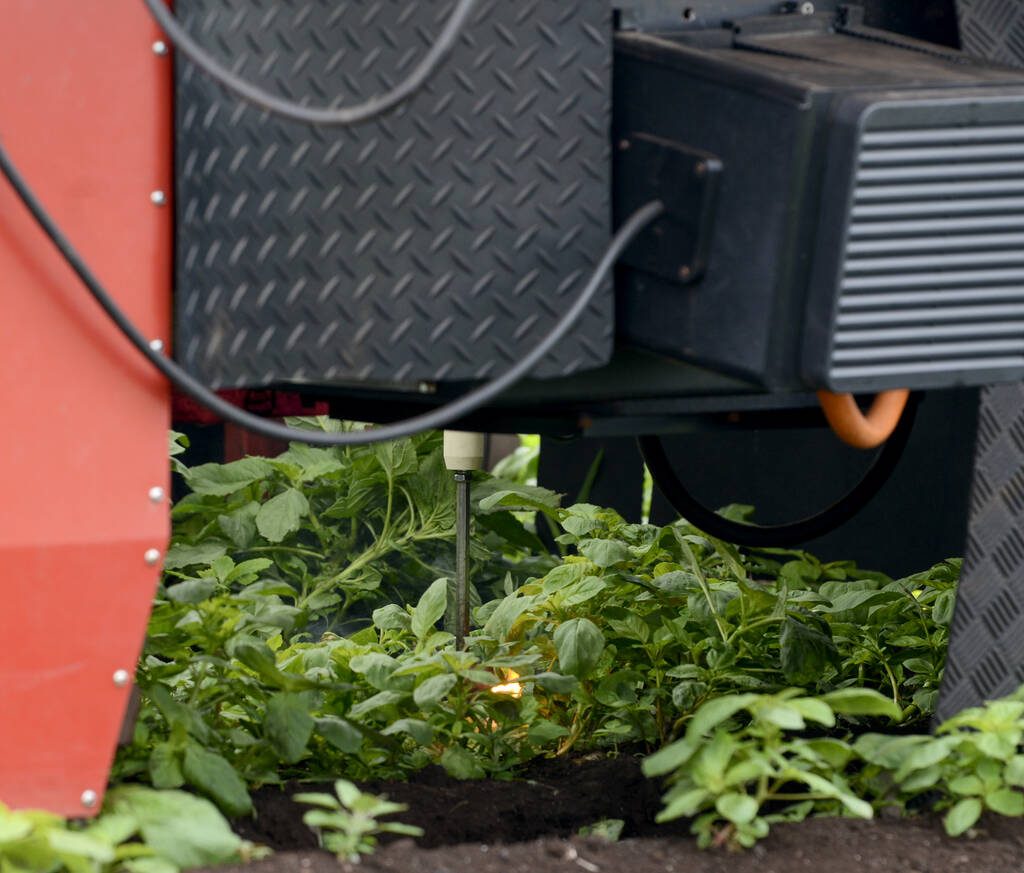
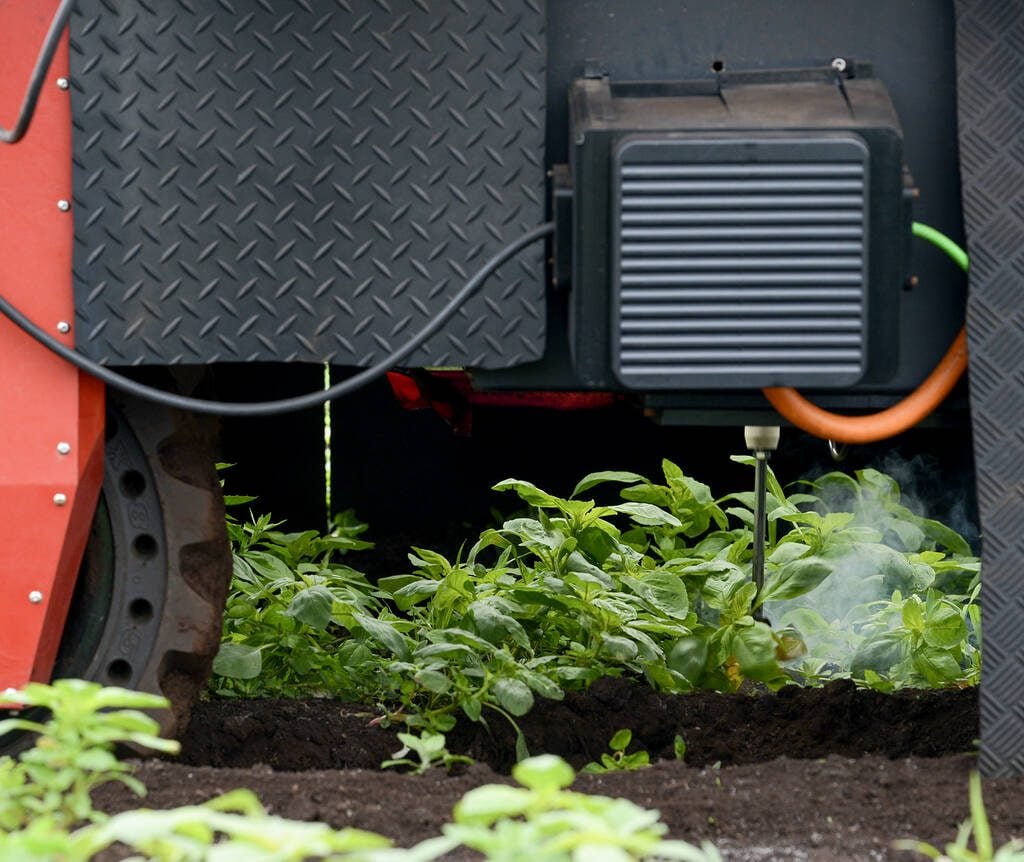
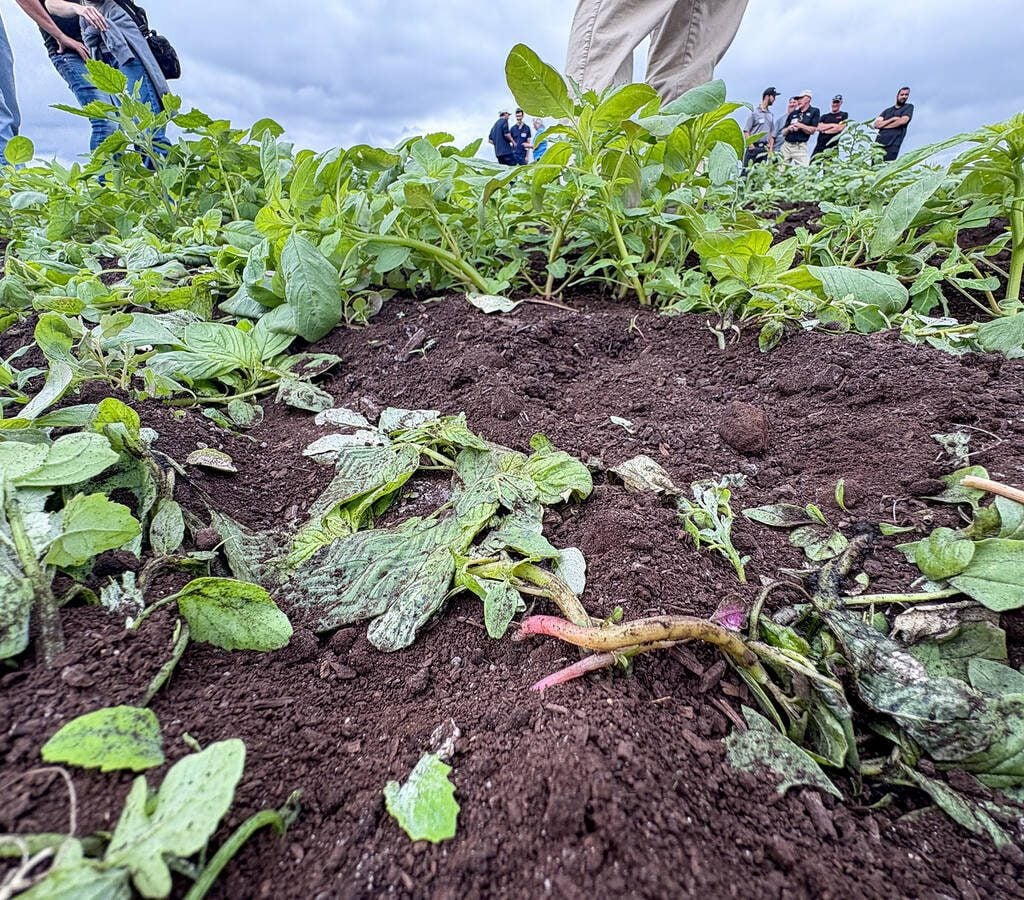
The key difference between the ElectricWeeder and other robotic options is its ability to dispatch weeds at any size and growth stage.
“It has two modes of operation tailored towards both low weed density fields and high weed density fields,” Tao explained. “It will maintain the same efficiency at killing weeds.”
The 1.2-ton machine can weed up to 10 acres an hour and operate in most weather conditions 24/7, but like traditional iron, mud can be problematic.
“A bit of rain, a bit of drizzle, a bit of moisture is fine, but not too much,” he said. “Not like a muddy kind of pouring rain where you have ponds in the soil.”
The ElectricWeeder comes in autonomous, tractor-pulled, and tractor-liftable models, with coverage from five to 20 feet and swath widths of 60, 120, and 240 inches, plus an adjustable row spacing of 60 to 88 inches. The sub-millimetre precision and 99 per cent weed kill rate make it more efficient than a 100-person hand crew.
Tao said the US$150,000 commercial versions will ship near the end of the year.
Ontario’s rainfall leads to very high weed pressure across much of the province, with a three to seven-day window for a new weed flush, which means robot weed control will never be a one-time pass, said Baresich. “Part of the economics of the machine is how many times do I have to go through that same field, and can I get it done?” he shared. “In comparison to hand-weeding crews, where the costs are $500-$1,000 an acre, these are very economical to run.”
He admits that chemical weed treatment remains cheaper; however, in cases of herbicide resistance and hand pulling, the ROI of laser or electric weeders pencils out.
“I think the reality is that even though the ROI might not work, we’re going to be forced into the robotic technology just because of weed resistance,” said Baresich.