Signs of soil compaction are evident across Ontario this year due to persistently wet weather during the harvest and wheat planting seasons in fall 2021, crop consultant Peter Johnson told attendees of a Compaction Day on-farm demonstration in Rostock Aug. 5.
Under soil conditions purposefully manipulated to mimic a wet spring, a recently harvested wheat field was subjected to numerous heavily loaded machines as the Perth County chapter of the Ontario Soil and Crop Improvement Association (OSCIA) welcomed nearly 200 people to the demonstration.
Fred Knechtel hosted the morning event while lunch and the afternoon discussion took place outside the Rostock Hall, within sight of the Knechtel farm.
Read Also
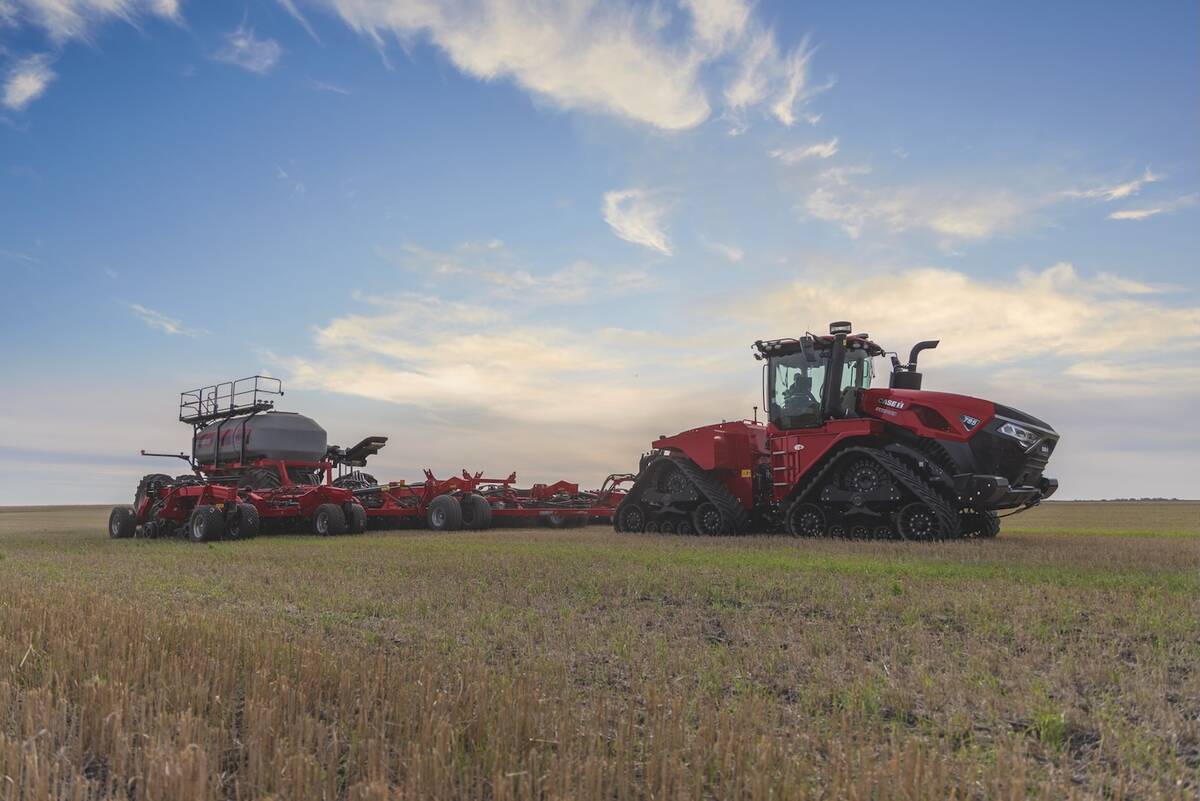
Case IH unveils its new giant: the 785 Steiger Quadtrac
Case IH’s new Steiger 785 Quadtrac tractor, due out for delivery to farmers next summer, uses the same basic chassis as the 715 — but under the hood its drive train has been beefed up to accommodate the added power.
Why it matters: Soil conditions and axle weight on equipment can influence the level of compaction.
Ontario Ministry of Agriculture, Food and Rural Affairs (OMAFRA) engineer Alex Barrie, who spent much of the previous two weeks preparing the Knechtel site, said that three weeks before the event, during a long stretch of dry weather, he couldn’t force a soil probe down even 12 inches. He watered the small plot extensively to get moisture at depth. And then came nearly two inches of rain two days before the Compaction Day.
“The water definitely lubricated that soil profile,” he said with a smile.
For the compaction demonstration, Barrie placed sensors at six-, 12- and 20- inch depths, and various implements were driven over the spot. The audience could see the pressure applied in real time as the sensor data was transmitted to OSCIA’s new mobile trailer screen.
According to Barrie, readings of 15 psi at six inches mean there is potential for compaction. And with anything above 7.5 psi at 12 and 20 inches, there’s also a good chance of compaction.
A fully loaded combine was first to drive over. Even though most combines appear to carry more weight toward the front (due to the header and bin), it was clear the rear axle, typically with a smaller diameter tire, brings the biggest risk of compaction.
“So, you’re seeing more and more big duals on the rear axles and that wasn’t even thought of until we started doing these compaction days,” said Johnston.
In the Aug. 5 demo, the rear axle caused just over 20 psi at six inches with the sensor placed between the two duals on the left-hand side.
A tracked grain buggy with multiple axles was next. Johnston noted that, with successive axles on an implement going over in a short time, there is a percussive effect and the soil is weakened by the time the final axle passes over.
The next two implements highlighted the value of central tire inflation systems (CTIS). A double-axle spreader with tires inflated to road conditions at 58 psi, pulled by a tractor inflated to 29 psi, caused significant pressure at all three depths. Jake Kraayenbrink, a CTIS innovator who developed a system for his own company, was operating the unit.
For a second pass, Kraayenbrink deflated all the tires while seated in the tractor cab and drove over again with the sprayer tires at 26 psi and tractor tires at nine psi.
Barrie said that closer to the surface, tire pressure is the dominant factor in whether there’s an increased risk of soil compaction.
It’s not because the tire spreads out laterally. A good sidewall and effective bead on the rim prevent that from happening. Instead, there’s less compaction because there’s a greater lengthwise surface area of the tire or tread in contact with the ground.
At the 12- and 20-inch depths, the dominant factor is axle weight.
“You just can’t lay down enough surface area by spreading out that tire to protect the soil from too much axle weight,” said Johnson. If the equipment is heavy and the ground isn’t ready, “you’re really reducing the ability of the water to drain if you see compaction at those lower depths.”
Next up was a sprayer with tall and narrow tires inflated for road use. The numbers showed a high compaction risk. Even if those tires are deflated within manufacturer recommendations, Johnson said, “whenever you take a sprayer into the field, it’s just about impossible if you have skinny tires on it to not do a lot of damage.”
“There’s really not much you can do about it when you’re using row crop sprayers.”
To put sensors to a final test, organizers subjected them to a traditional gravity wagon, fully loaded, with four tires inflated to 55 psi. After numerous implement passes, a significant depression had already developed over the sensors but the gravity wagon rendered the six-inch sensor useless by bending the steel tube attached to the sensor into a horseshoe shape. The monitoring equipment at the lower depths was also bent.
Barrie said that there’s still a lot to learn about the effects of heavy equipment on wet fields.
“What you’re seeing (from this demonstration) is the load on the soil. But we’re missing the information on exactly how much compaction this actually causes because in some cases it can change even throughout the day as (the soil) dries out.”
The OMAFRA engineer also noted there is solid research showing compaction of a different orientation can occur due to the horizontal torque applied by tractors or self-propelled implements in wet soil.