Autonomous equipment use in Ontario agriculture is growing, but mostly in areas where crop value is high and the challenge of finding human help for crop care has dire consequences for farm profitability.
For example, Haggerty AgRobotics has nine Naio Oz units leased to Ontario farmers, most of them market garden farmers who use the units to do some of the weeding needed between vegetable crops.
Read Also
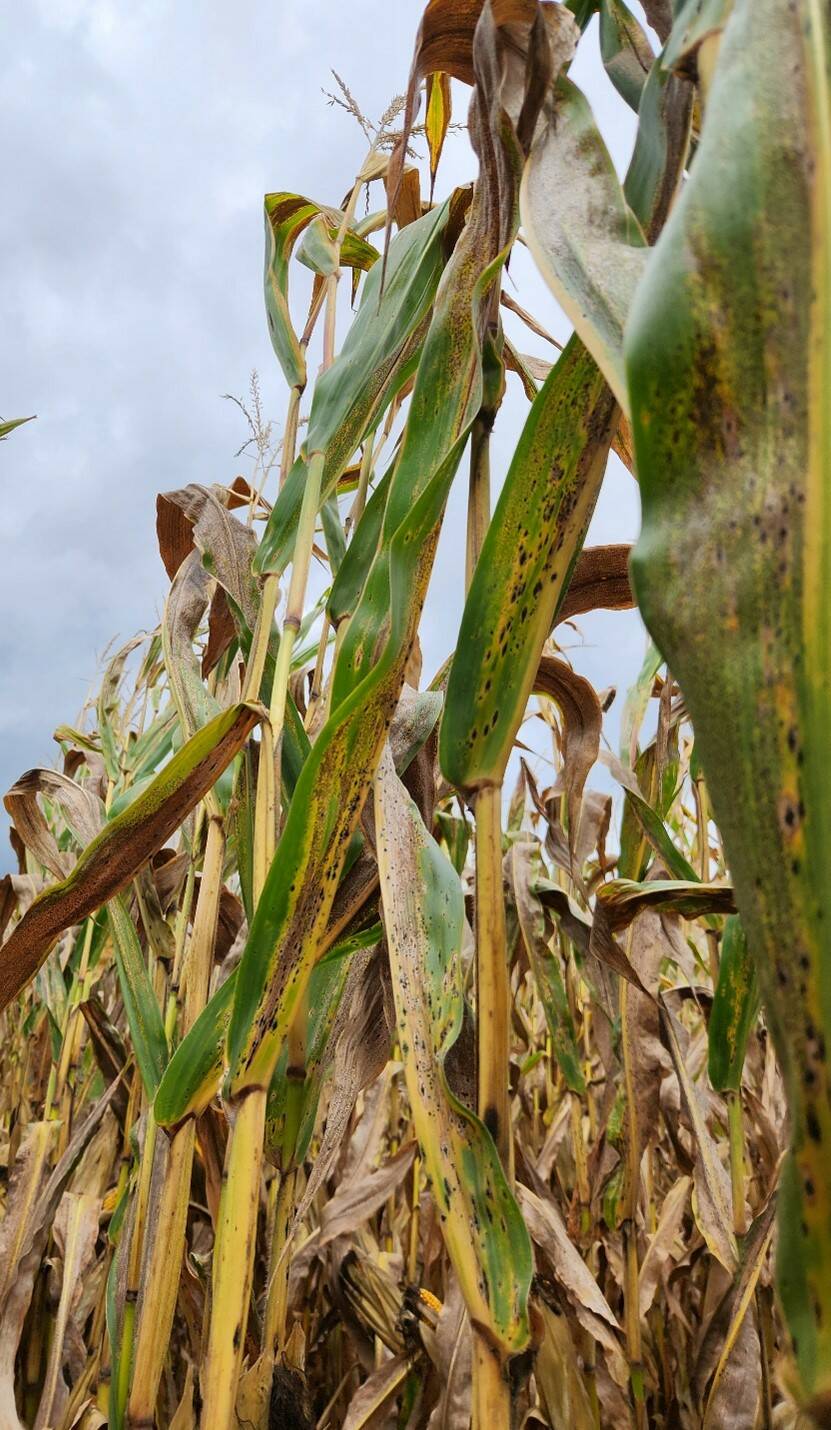
Tar Spot firmly planted in Ontario corn
Scouting is critical for mitigating impact on tar spot, as well as timely fungicide application.
A working group for autonomous equipment, now with 127 members, meets weekly and recently held two tours of farms using autonomous equipment.
Why it matters: Farmers have increasing challenges finding workers, especially for high value crops. Autonomous solutions offer alternatives, although most are still in development.
A recent southern Ontario tour visited equipment working in fields between Bothwell and Chatham-Kent.
READ MORE: Here come the crop robots
In an organic soybean field near Oakdale, a green and white Naio Dino unit hummed up and down rows, cultivating out weeds. Sharp Farms finds it challenging to keep up with its cultivation of crops in time to manage weeds. The Dino is a partner to help manage their workload.
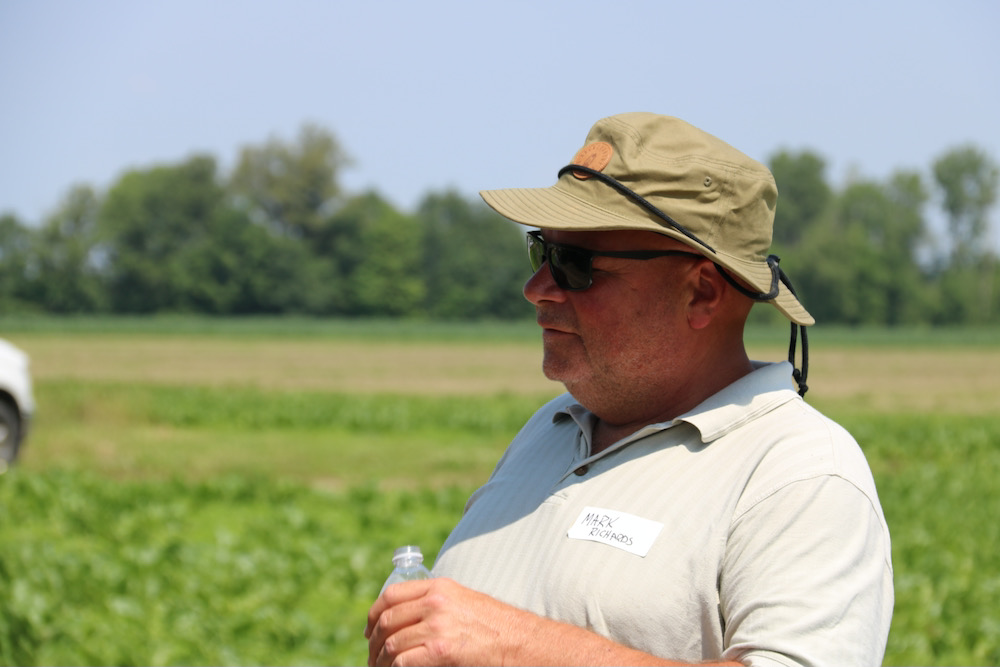
“We have almost tripled the amount of commercially deployed robots,” says Chuck Baresich, of Haggerty AgRobotics, the leading provider of autonomous agriculture robots in Ontario. Baresich hosted the event, starting at the farm supply business he owns with his brother.
“It’s still not a big number, but it’s significant. We are much more confident as to what we can get done. If a customer comes to us and says I have a challenge, we are much more confident in saying yes we’ll take it or no we won’t.”
The robots have improved significantly, but they still need a lot of work and management, says Baresich.
At Haggerty AgRobotics, there were an array of robots shown that are being researched or are working in other areas of the province.
Baresich’s advantage is that he’s agnostic when it comes to the technology. As a supplier, he can bolt on other agtech when needed.
They are putting a Vivid Machines system on a Naio Ted robot destined to help weed in a vineyard so that it can help control weeds and record crop information at the same time. Vivid Machines is another Canadian agtech company that focuses on the crop load on a plant to better understand how much fruit will be available at harvest.
He uses fleet tracking and mapping technology from Intelliculture, another Ontario startup company, to try to bring information from multiple robots into one platform.
“It doesn’t matter what colour a robot we have these mounted on, all of the mapping shows up in the same platform,” says Baresich.
At another stop on the tour, Mark Richards showed the Robotti power unit, which is in essence a 70-horsepower tractor with a three-point hitch – and no seat for a human.
Instead, hardware and software guide the tractor around a farm.
Richards used it for planting sugar beets at his farm just outside of Dresden. He used an old four-row John Deere ground-drive planter that was cut down so it fit inside the frame.
“It worked pretty good, a pretty simple system, a chain drive, seed drops pretty low, very good spacing.”
He had the Robotti plant in between 40-foot test strips planted with his usual John Deere 1790 planter.
Unfortunately, seeds from the conventional and automated planters germinated poorly due to only a half an inch of rain falling within eight weeks after planting, so the field had to be replanted.
In another field, the robot planted 50 acres of sugar beets deeper, and it was a tough field due to dryness, but it will be harvestable.
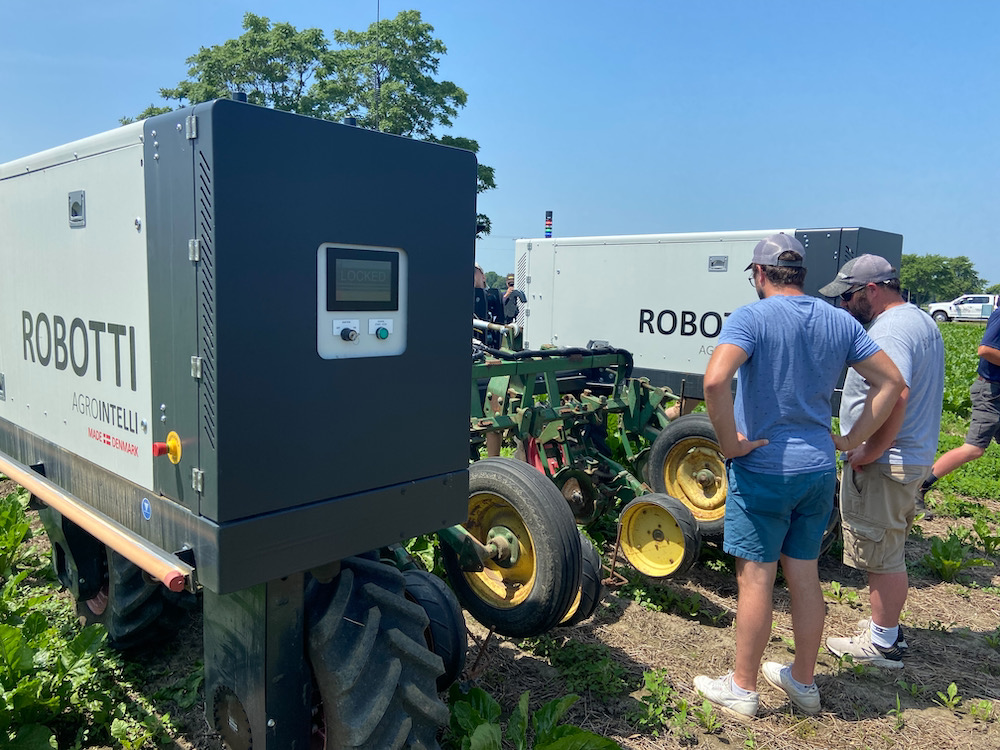
Richards has some funding to replace the planter unit next year with a Precision Planting four-row planter with the works: smart firmers on every row, automatic down pressure with the Delta Force, automatic depth control based on the moisture readings from the smart firmers and vSet electric drive electric vacuum meters.
Remote access to the unit will allow for on-the-go monitoring and changes even when someone’s not in the field.
“We’ll be able to make changes if we want it to plant deeper based on moisture or hold its depth,” he said.
Kearney Planters is helping with the project.
Richards plans to build a two-row strip-till unit for the Robotti for next year as his operation is mostly no-till or strip-till.
He also hopes to soon have a 10-foot sprayer re-engineered for the Robotti, which will band-spray fungicide on sugar beets, which he expects will reduce his fungicide costs by 30 per cent.
“I still struggle with is there a use case,” says Richards. “Is this kind of technology scalable in an operation? We farm about 1,200 acres and we pull a 16-row planter right now at two and a half mile an hour in beets and five miles an hour in corn and soybeans. If you’re going down to a 10-foot planter that will only ever go three miles per hour, there are pluses and minuses to that.”
He says he continues to work on autonomous projects as he sees it as a way to bring new people into farming. He also makes the point that those people have to be technologically savvy, but they will also have to be willing to carry a bag of seed to fill a planter too.
Lots to learn
Farmers who are early to try autonomous equipment are finding there’s lots to learn.
Richards, for example, says to make sure you know whether the GPS systems are anchored on latitude or longitude.
“If it’s longitude, that means a curve of four inches on 2000 feet,” he says. “Don’t ask us how we know.”
The solution was to set an AB line for the field.
At the Sharp Farms field, Baresich says making sure the components are properly set and calibrated is important, especially LiDAR, which is critical to guidance.
But Baresich pointed out that last year during the autonomous working group’s tour, not all the robotics were working, and this year, all were functional and doing valued work.
A new kind of mindset is required for this technology, says Ian McDonald, applied research co-ordinator for field crops, with OMAFRA.
“We’ve got to get beyond what we think it needs to look like, we have to understand what is this problem that we’re trying to define and address and then be able to convey that to the people that are making stuff for us. And those people that are making stuff for us? We’ve seen many of them come to us with a solution, not really understanding what the problem was.”