Glacier FarmMedia – Hog barns’ loadout docks are key entry points for PED-carrying dust, and they require close attention, says a Manitoba veterinarian.
“All of our hog barns are essentially gigantic vacuum cleaners, and the warmer the conditions outside, of course, the greater the suction of our vacuum cleaners,” said Dr. Tony Nikkel, director of veterinary services with the Progressive Group of Companies in Niverville.
Why it matters: Porcine epidemic diarrhea (PED) virus can affect pigs of all ages but is often fatal to young piglets. There is no cure, so adhering to strict biosecurity protocols is the best defense against the virus.
Read Also
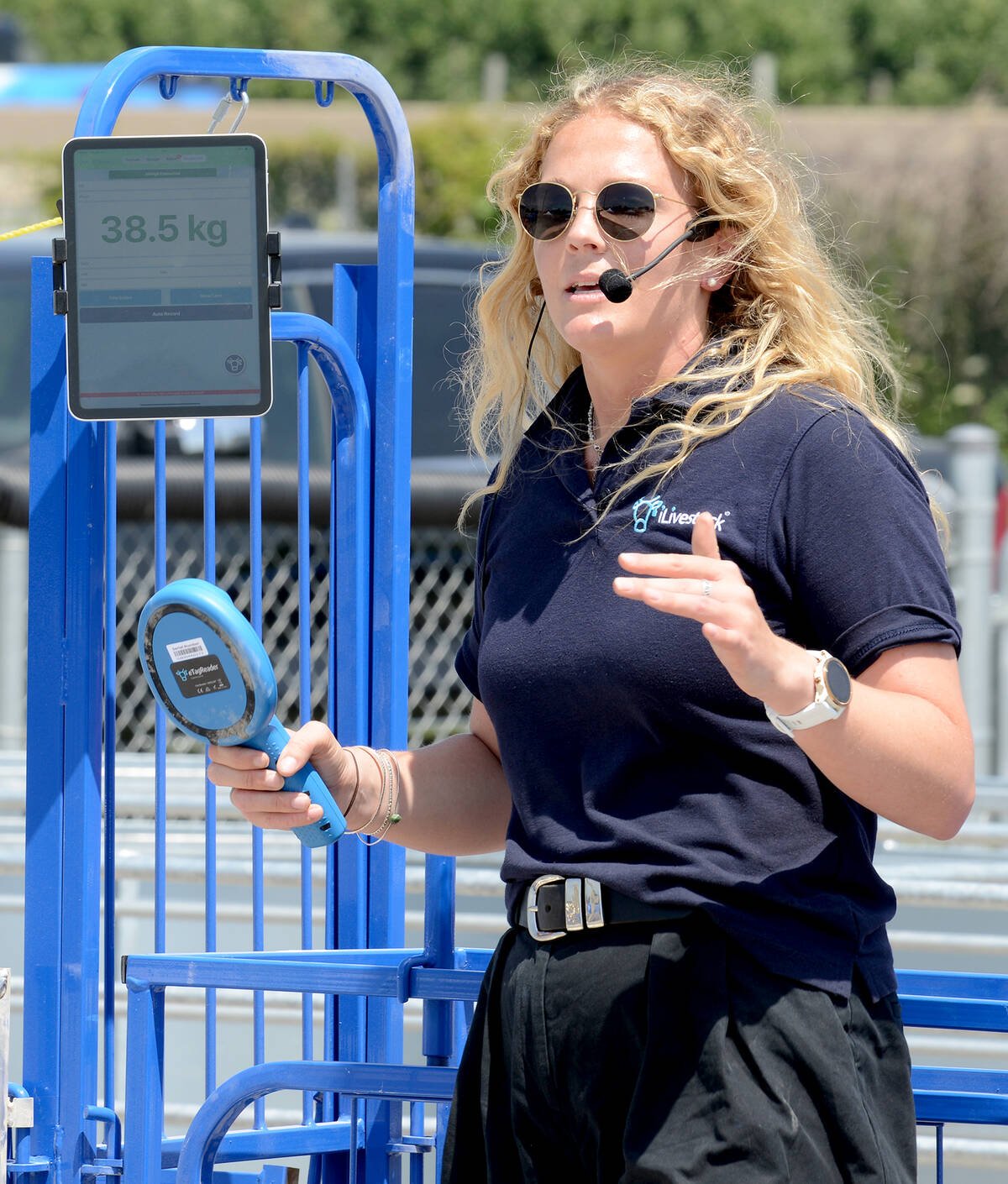
Track, Treat and Trace: iLivestock software comes to Canada’s Outdoor Farm Show
Discover how iLivestock’s all-in-one farm management software — offered through Weber Farm Services — is helping Canadian cattle and sheep producers digitally manage breeding, treatment, weighing and traceability at Canada’s Outdoor Farm Show.
“That is basically the basis of how this virus gets into these barns most of the time.”
Nikkel spoke during a Dec. 7 Manitoba Pork Council-led town hall meeting. The province reported more than 20 cases of porcine epidemic diarrhea (PED) in 2021, while Ontario reported eight cases.
Nikkel said the Progressive Group has experienced 35 cases of PED in its barns over the years. When cases were traced, the two most common methods of spread were aerosol and movement of PED-positive pigs into a farm. Loadout docks at barns were the third-highest route of transmission.
In 2018 and 2019, the company tested dust in the attics and air-intakes of barns with breaking PED cases. Some were positive for the virus.
“We recognized dust is probably a significant form or method of spread of this virus,” Nikkel said.
PED viruses can attach to water vapour and dust particles in the barn and be blown out with exhaust fans. They may then spread to more dust, water vapour, mud and snow.
Nikkel said reports show the virus can remain viable on dry feed for a week, and likely would have a similar lifespan on dust. Cool temperatures may allow it to survive longer. The goal is to reduce the contaminated dirt that barns pull in.
By the time they reach barns, most livestock transports have significant amounts of dust on the rear of their trailers, which then touch the barn, Nikkel said. That dust can be limited by ensuring all panels are in place on a clean truck en route to a farm.
It is also good practice to rinse the rear of livestock trailers with disinfectant before they back into the dock. Some commercial haulers carry a sprayer with disinfectant for this purpose, Nikkel said, but it’s advisable to have a backup sprayer on hand.
He also suggested disinfecting the outside of the loadout dock before any trailer arrives.
Provincial veterinarian Glen Duizer said commercial washers take three times as long to clean trailers as producers do, so the latter should take more time at the job if they wash their own trailers.
It’s a good practice to simply assume that PED is in the farmyard and driveway and act accordingly. Nikkel said the Progressive Group has begun dust-proofing farm lanes and loadout dock areas with calcium. He also suggested spreading hydrated lime over the dock area to kill pathogens that may drop from a trailer or from drivers’ boots and clothing if they’re not changing them as they should.
Keep loadout docks’ bumpers and seals in good condition because they can collect manure and straw, he added.
Turn off the vacuum
Farms can also reduce the loadout area’s vacuum effect. Ideally, producers would reverse the vacuum and pressurize the loadout room, said Nikkel, though he recognized that’s not always possible.
This could be done by using fans installed in the interior hallway wall or attic and blowing into the loadout room. The loadout interior door would be closed to pressurize the room, otherwise the loadout fans would compete with fans in the main barn.
It’s good practice to move pigs into the loadout room, close the hallway door, pressurize the loadout room and then open the loadout dock door, Nikkel said. If workers need to bring in more pigs, they should close the loadout door before reopening the hallway door.
If the loadout room can’t be pressurized, Nikkel suggested minimizing the vacuum effect by closing as many doors as possible in the barn and moving as many pigs as possible into the hall before opening the loadout door.
Even then, it’s best to have backup biosecurity measures in place, he added. He suggested treating the loadout room as a separate space from the rest of the barn, designating staff to work in that room during shipping and receiving, and requiring them to use separate clothes, coveralls and boots in that area.
Ideally, the loadout room would have its own pressure washer line hookup so the wand and hose aren’t dragged through the barn.
Geralyn Wichers is a reporter with the Manitoba Co-operator. Her article appeared in the Dec. 16, 2021 issue.