Canadian-developed technology is making feed bin management easier, safer and more efficient.
BinSentry, founded in Waterloo about seven years ago, is installing about 2,500 new sensors per month across North America, with a new deal with Cargill providing an entry into the Brazilian market.
Why it matters: Accurate bin inventory means less guesswork for farmers and feed mills and reduces the chance of feed outages.
The technology can mean better outcomes in emergencies, such as the floods that hit the Fraser Valley in British Columbia in 2021, says Derek Fadden, feed planner and logistics analyst with Ritchie-Smith Feeds in Cranbrook, B.C.
Read Also
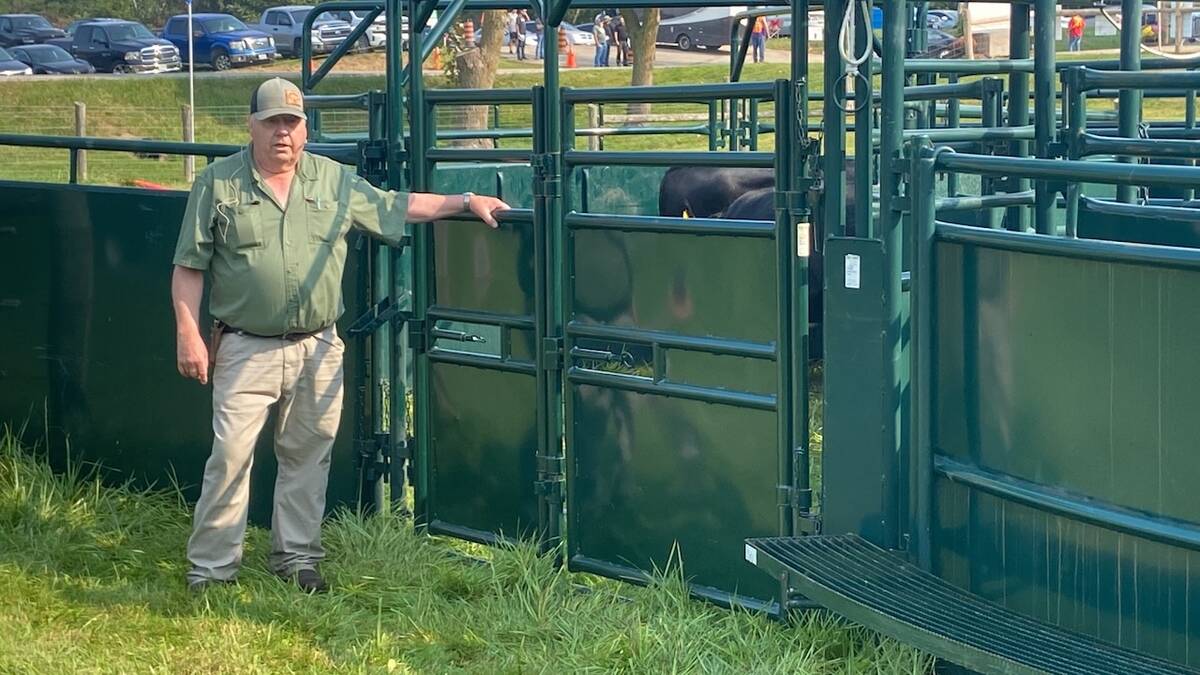
Livestock demos feature the latest in handling and management
Livestock demonstrations feature the latest in handling and management at Canada’s Outdoor Farm Show 2025.
As flood waters rose, there was chaos for the concentration of dairy and poultry producers in the valley, including severe challenges getting them feed.
Fadden added one of the challenges was knowing which barns were out of feed.
There was a lot of running to farms when there was an opening in the flood or when the farm deemed it needed feed. BinSentry sensors, which use time-of-flight cameras to monitor what is actually in bins, would have made that process more efficient.
BinSentry is an Ontario ag tech success story. The company has evolved from an idea in the minds of two University of Guelph graduates to changing how feed is managed across North America in seven years.
BinSentry maintains its only office in Waterloo, even though Ben Allen, now the company’s CEO, is based in Austin, Texas.
The company uses artificial intelligence to learn more about the management of feed and the cost of not managing it precisely.
“It was started by two founders that were really good at IoT (Internet of Things),” says Allen. They recognized that animal feed is one of the largest supply chains on the planet, but had fundamental challenges with bin management.
Farmers have for generations managed their feed bins by tapping them with a mallet or climbing them to estimate feed supply. Neither is accurate, nor safe.
“It’s like driving your truck with no gas gauge,” says Allen. “You’d get really good at pumping the tank to try and hear how hollow it was. That’s how we run the animal feed supply chain globally is with guys with no gas gauges and those inefficiencies ripple through the supply chain like crazy.”
Imperfect data means more trips with trucks to top off the bins.
“With accurate data you can say ‘Hey, I don’t need eight tonnes today, I need a full semi load in in 72 hours,’” he added.
“That’s cheaper logistics.”
BinSentry aggregated data to solve bigger problems for the industry once bin sensor installations passed 10,000.
What Allen calls slide outages are an unseen problem in the sector. Slide outages happen when no one knows the exact moment the slide needs to be changed from an empty to a full bin. Feed efficiency, critical to profitable hog and poultry growth and agriculture climate impact, take a hit in that period before the slide is moved and that’s a hidden cost.
BinSentry figured out that 70 per cent of the time animals were out of feed, it was because of a slide issue, and it correlates well with feed conversion ratios. Allen says the industry only knows about 20 to 30 per cent of the feed outage problems that occur.
“We believe we’ve solved that problem for the global industry and people just don’t know it.”
The industry spends a lot of money on precise nutrition formulation and genetics, but feed outages compromise that investment.
“It’s a fixable problem if you have our tech,” says Allen.
A big problem that took a while to solve
Bin monitoring by mallet and ladder are poor ways to monitor bins, but there are reasons the practice has taken so long to improve.
Anyone who’s made a trip up a bin to unlodge feed knows that it doesn’t follow the rules of other materials. Feed doesn’t have predictable piling characteristics like sand. Liquids are self-levelling.
“Animal feed doesn’t have a clean angle of repose and isn’t self-levelling,” says Allen.
Some have put scales under bins, but that’s a more expensive fix and involves lifting and lowering bins and calibration.
BinSentry uses time-of-flight cameras that give an accurate three-dimensional view of the pile of feed. He says they are more accurate than sonar or lasers, and it’s only in the past four years that the cameras were good enough to do the job.
Shipping across North America and now into Brazil and installing 2,500 sensors per month means the company has moved to a commercial scale. Allen doesn’t like BinSentry being called a startup company anymore.
They distribute through feed retailers, meaning farmers who want the technology shouldn’t call BinSentry; they should call their feed company. Clients include Wallenstein Feeds in Ontario, Maple Leaf Foods in Manitoba and Hanor, one of the leading pork-producing integrators in the United States.
Ritchie-Smith, the British Columbia feed company, is rolling out BinSentry sensors to its feed clients in the Fraser Valley. That’s the second phase of introduction of the sensor for the company as it first tried them at its Sure Crop Feeds mill in Grindrod, B.C.
They started with 75 sensors and grew to 300 on farms after six months.
“We very quickly saw what it could do, that it was reliable, that it was accurately predicting what’s in bins,” says Dave Dieleman, general manager and CEO of Ritchie-Smith Feeds.
Trucking efficiency has improved and better understanding of when feed is needed has meant they can get more production out of the Sure Crop Feeds mill, which was nearing capacity.
In the Fraser Valley, the Ritchie-Smith mills are in the unique position of having most of their clients for the Abbotsford mill within an hour’s drive. Most of the farms have one bin as they are well-served by feed companies.
“We weren’t sure if we’d see the same kind of economic benefit as a result,” says Dieleman.
However, the number of out-of-feed events, especially on holidays and weekends, has declined significantly. The company is better able to manage poultry end-of-flock feed returns closely, resulting in fewer trucks on the road, a significant savings for the company.
The farmer is mostly taken out of the ordering equation. The order desk at the feed mill can see how much feed is in the bin and schedules a truck as needed.
That’s made Fadden’s job, as a feed planner, simpler.
He used to have to manage the margin of error of the poor estimates he received to make sure bins weren’t underfilled or over overfilled.
“The sensors gave me direct eyes into every bin,” he says.