Establishment of crop variety trials by Syngenta became standardized and considerably more efficient over the past two years as the company purchased a fleet of 22 PowerPlant research planters from Iowa-based, family-run manufacturer Almaco.
Why it matters: More efficient variety testing capabilities mean it’s possible for improved genetics to be commercialized more quickly than in the past.
One of those planters is stationed at the company’s Arva research farm, and operator Bryan Van Oostveen chatted recently with Farmtario about the benefits brought by the PowerPlant and opportunities for enhancement to Syngenta’s crop trial testing network in Ontario.
Read Also
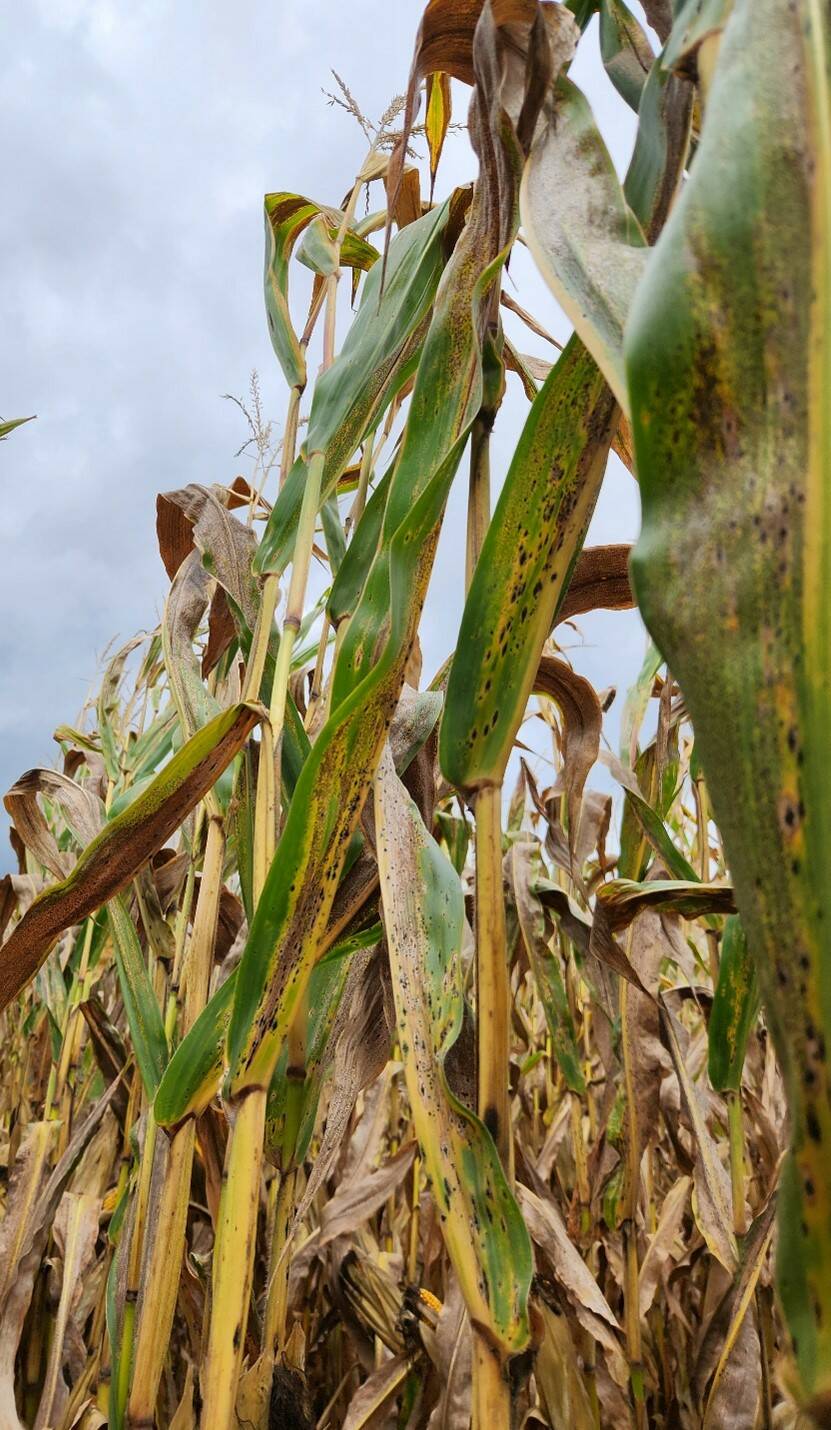
Tar Spot firmly planted in Ontario corn
Scouting is critical for mitigating impact on tar spot, as well as timely fungicide application.
“I’ve heard we’re seeing a 30 per cent improvement” in the efficiency of the company’s research and development pipeline, Van Oostveen said as he prepared to begin harvesting soybeans from the Arva station’s fields on Sept. 19.
This year, that harvesting takes place on an older-style combine but also on the horizon – thanks to a major Syngenta investment in North American crop trial modernization – is a fleet of new Almaco plot combines.
For the casual observer, the most noticeable change from Van Oostveen’s previous plot-planting work is that he’s now the only operator on the unit. In the past, depending on whether it was a four-row or eight-row plot, he operated the tractor while either one or two technicians rode on the research planter and manually opened envelopes full of seed to dump them in the appropriate rows.
With the PowerPlant, plastic “clamshell” cartridges carrying a unique bar-code identifier are loaded into the planter at the edge of the field, the on-board computer is programmed using GPS to open the cartridges at the appropriate location, and Van Oostveen is the only operator as the unit completes the planting.
“We always have a second person in the field for safety reasons,” he explained, adding that person can also use the time to set up the next batch of cartridges to be loaded into the planter.
During the challenging planting season of 2024, the fully automated nature of the PowerPlant offered the particular advantage of allowing for continued operation in darkness.
Van Oostveen recalled that the persistence of rain in the forecast last spring meant field operation windows were frequently compressed but being able to work into the evening and night allowed Syngenta to effectively establish all its planned 18 corn plot trials in Ontario – on cooperating farms stretching from Wallaceburg to Sunderland.
The PowerPlant can also be driven faster than the previous unit.
“With the old system,” Van Oostveen noted, “we were limited by only being able to go as fast as someone could comfortably open the (seed) packets and deposit them in the planter.”
Perhaps less visible to the casual observer but equally important when comparing to the previous research planting system are the automated features of the PowerPlant where the implement meets the soil.
“This system has been built in a way that it represents what farmers are using on their farms today,” Syngenta product placement specialist Matt Rundle told visitors during the grand re-opening of the Arva research station celebrated earlier this year following two years of interior renovations.
The PowerPlant was an added feature for the tour that day.
The PowerPlant includes GPS capabilities from Ag Leader, well-known in commercial crop farming circles. For Van Oostveen, that means remote control of the trash-whippers where previously they had to be manually adjusted as field conditions changed.
And manually checking to determine the necessary level of hydraulic down-pressure is now a thing of the past.
“With the Ag Leader system, that’s all running from sensors and it’s automatically adjusted as you go down the field,” the research equipment operator explained.
With different elements of the machine powered either by the tractor’s hydraulics, electrically through a generator on the tractor, or by air from a compressor in the tractor, there’s significant complexity in maintaining precise depth and seed drop.
But Van Oostveen said the enhanced precision afforded by the new machine will “reduce end-row effects and increase the uniformity of our plots.”
From a crop testing perspective, however, by far the biggest improvement of the PowerPlant is its use of and generation of data.
The bar-coded seed cartridges mean far less chance for human error in establishing the plots. Thanks to an on-board modem (assuming there’s internet connectivity in the field), Syngenta’s research department gets information about the planting operation in real time as the seed goes in the ground.
By the time Van Oostveen gets off the tractor, that data has been compiled into a report for the Arva team.
“That’s something we didn’t even dream of 15 years ago.”
Thanks to the GPS capabilities, the traditional follow-up task of plant stand analysis has also been transformed. Where a team of technicians would formerly have been dispatched to the field trials several weeks after planting to assess plant stands – a process open to human error or subjectivity – Syngenta’s Ontario team now uses a laser unit mounted on an all-terrain utility vehicle that follows the exact GPS-generated route that the planter followed.
“These investments will improve the quality of the data we’re using for those decisions and improve the efficiency of bringing varieties to market,” Rundle told the Arva grand re-opening audience.
Rundle explained the majority of the varieties being planted in research plots are new varieties not yet introduced commercially. In a process that can take five years in total for bringing a new variety to market, if a variety is in a research plot it’s still possible it will be up to two years away from commercial introduction.
But the plots also have “comparison checks” with existing NK varieties to fine-tune the knowledge about the yet-to-be-introduced varieties regarding maturity or projected yield, and there are “competitive checks” within the plots for varieties sold by competitors.