Glacier FarmMedia – Replacing leaking seals on machines is one of the most common on-farm repairs. It isn’t particularly difficult, but not getting a replacement seal seated correctly means wasted time, effort and money. Here are a few tips to make sure the replacement goes in properly and, most importantly, stops the leak.
First, pay attention to where the old seal was seated prior to removing it. The component housing may be designed to allow the seal to bottom out. When the seat goes as deep as it can, you’ll hear the tone of the hammer blows change, and you will feel the resistance.
However, not all housings are designed this way. With some, you may need to simply stop driving the seal in when it’s flush with the edge of the housing or in the same position as the old one was.
Read Also
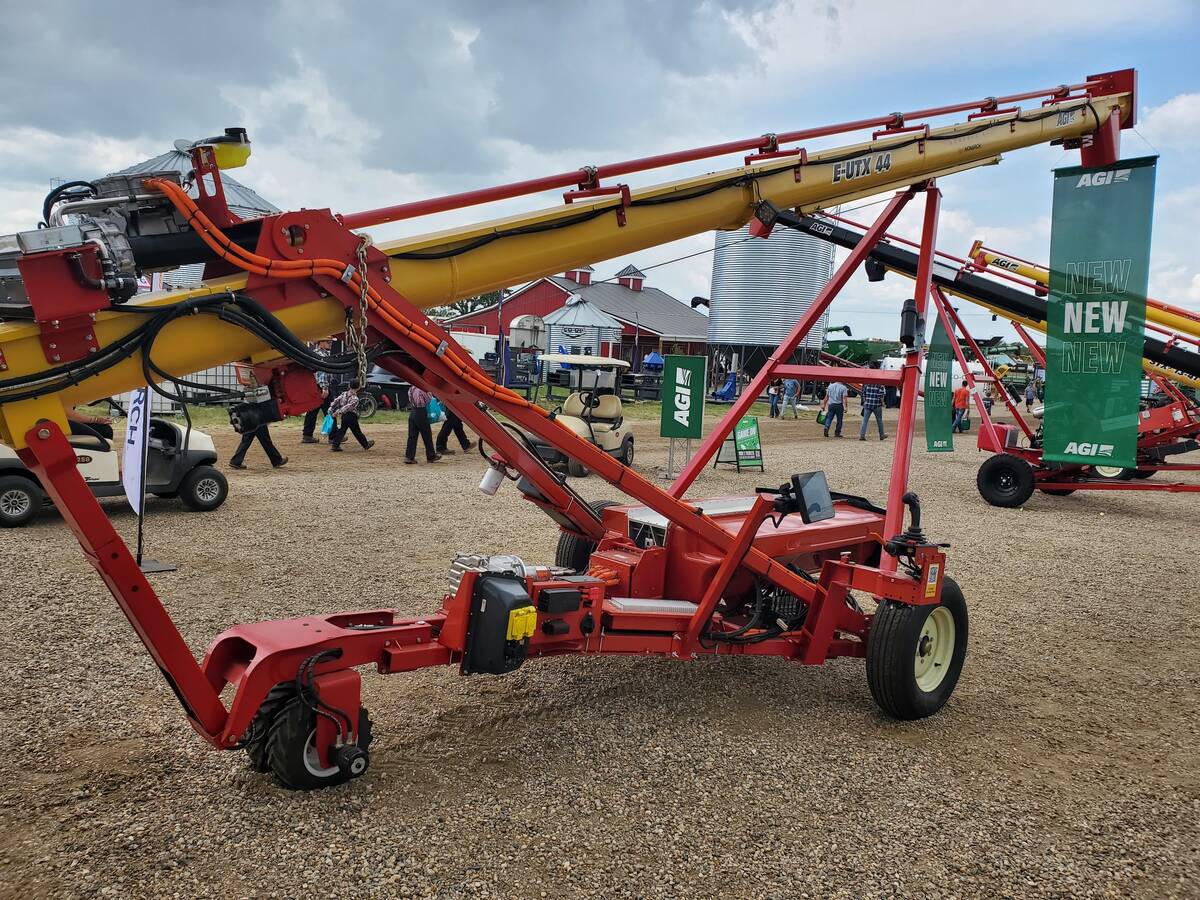
AGI unveils Smart Auger prototype
AGI showed its prototype E-UTX Smart Auger at this summer’s Ag in Motion 2025 farm show near Langham, Sask.
Before trying to install the seal, ensure the surface of the component is thoroughly cleaned, with all dirt and grease removed. Take a small flat-blade screwdriver and dig out any grime in the corner of the groove housing where the seal will sit. Allowing some debris to remain on the mating surface will prevent the seal from seating properly, and that will translate into a leak.
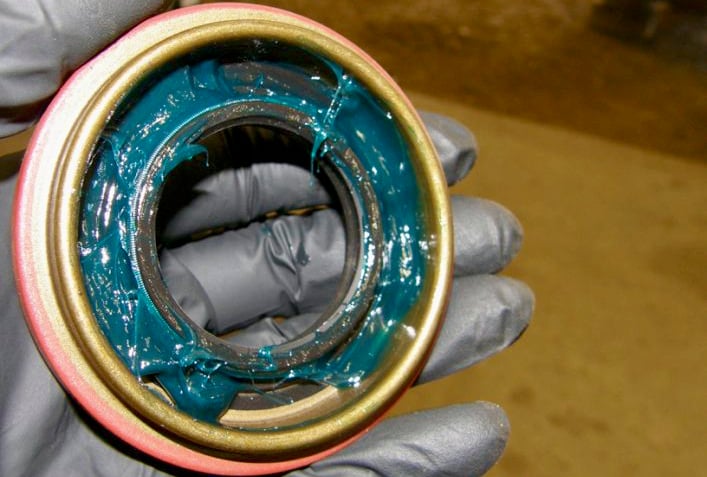
Next, check the shaft for pitting or other damage that could harm the rubber sleeve in the seal. If the shaft has a keyway, placing some tape over the keyway can help prevent its square edges from cutting the seal rubber. A light coat of lubricant on the shaft will allow the rubber sealing surface to slide easily.
If the shaft is badly pitted or worn significantly where the seal will ride, replacing the seal without repairing or replacing the shaft will be a waste of time because it won’t stop the leak.
Behind the rubber sleeve in a seal is a small spring running around the entire opening. It keeps the rubber sleeve held tightly against the shaft. When pounding in the seal, a hard blow can cause that spring to pop out of place, which will make the seal pretty much useless.
To help stabilize the spring in position, an old mechanic’s trick is to put some grease around it to help hold it in place.
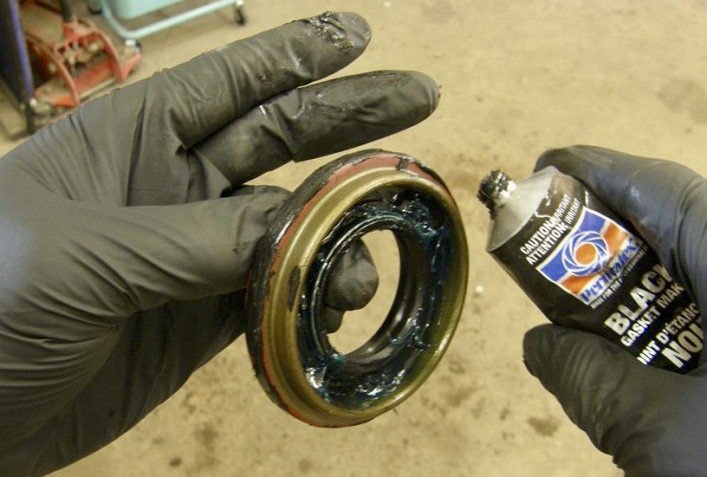
A seal driver kit will help you install the seal evenly and free of damage and would likely be a good investment. If you don’t have one, use a large socket or piece of pipe that is as close as possible to the same diameter as the outside edge of the seal. And don’t get carried away with the hammer. Light taps are adequate. Striking the seal too hard could deform it.
If the opening on the component housing looks a bit rough or uneven, coating the outer surface of the seal with RTV sealant can help prevent leaks there.
– This article was originally published at Grainews.